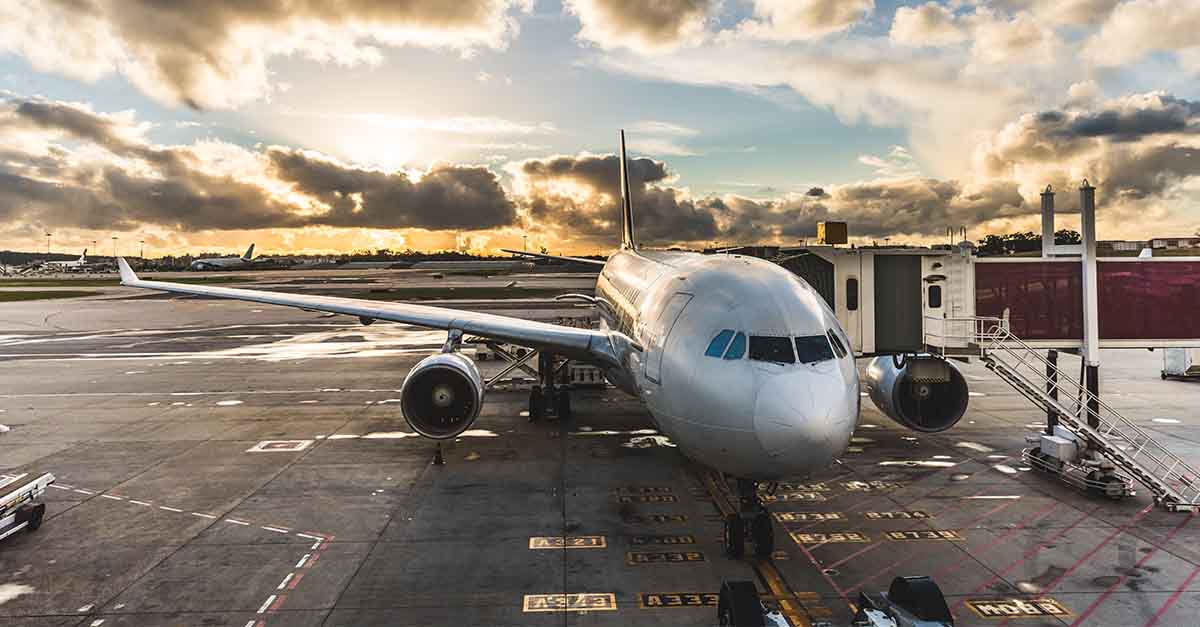
Enabling the Asset Management Processes at London Gatwick Airport to Truly Take Off
Discover how London Gatwick Airport streamlined asset and document management using Meridian for greater efficiency, accuracy, and collaboration.
Solutions
Resources
Browse our full library of resources all in one place, including webinars, whitepapers, podcast episodes, and more.
Support
Looking for access to technical support, best practices, helpful videos, or training tools? You’ve come to the right place.
About Accruent
Get the latest information on Accruent, our solutions, events, and the company at large.
Learn how L'Oreal decreased asset downtime, improved reporting and maximised asset life with Maintenance Connection CMMS.
For more than 100 years, L’Oréal has been known as the world’s largest cosmetics company. Headquartered in Clichy, Hauts-de-Seine, France, the company also has five major manufacturing facilities in the U.S, as well as 15 distribution centres across the country.
L’Oréal’s century-old business and manufacturing plants were home to thousands of employees. And as the company continued to expand across the U.S., it recognised that performance improvement was the required approach when it came to equipment maintenance.
L’Oréal realised it needed a strategy that considered both capital and maintenance team performance.
L’Oréal needed a system that would not only help track asset health, but also help the team maintain the lifespan of its equipment. Furthermore, the team wanted a system to house asset information, including information for unique equipment and products manufactured on a location-by-location basis.
In recognising that asset downtime and lack of performance tracking would hurt the plant’s progress, the L’Oréal team band together to search for a solution. Their most pressing must-haves included functionality that would allow them to:
The team went through an extensive process to vet CMMS vendors. They assembled a small group that ranked providers that met their key expectations and checklist of features in a desired system.
After careful consideration, the group landed upon Maintenance Connection’s computerised maintenance management software (CMMS).
The team relies on Maintenance Connection CMMS for:
The L’Oréal team also relies on the mobile functionality of Maintenance Connection. Now, any team member with a smart device is sent work order notifications while on the floor — without having to go back to the office to closeout past service requests.
“One factor we measure is the utilisation of our mechanics,” says Silverman. “We are always trying to bring that percentage up as high as we can. Now, one way we can do that is by not having them waste time going back to a central location to close out a work order. Everything is done remotely.”
L’Oréal leans on Maintenance Connection across its plants in the U.S. to minimise maintenance costs and maintain equipment of all types. And, with its multilingual features, the global company is planning to evaluate Maintenance Connection across additional plants.
Additionally, with the help of a Maintenance Connection’s customisable, intuitive CMMS software, the L’Oréal team can now produce detailed reports on top performance KPIs, house all asset information into one hub, increase mechanic utilisation on the floor, and decrease the risk of downtime associated with equipment breakdown. Maintenance Connection has also helped the company:
“Now, when we speak with plants that are Spanish, Portuguese or French speaking, they can evaluate the software,” explains Silverman. “We see a big advantage in the enterprise. Although we have factories all over the world, we’ve gotten to the point where we’ve narrowed down the scope of vendors that supply equipment to us to a known quantity to minimise cost and the variety of equipment throughout the organisation. And, that’s a tremendous advantage enterprise wide.”
You might also like
Discover how London Gatwick Airport streamlined asset and document management using Meridian for greater efficiency, accuracy, and collaboration.
Learn how Urban Utilities migrate over 900,000 asset records from an on-premise system to a cloud-based solution, improving the management and ...
See how BASF initiated an integration to streamline the data handover between engineering and maintenance, leading to direct access to updated assets.
Subscribe to stay up to date with our latest news, resources and best practices