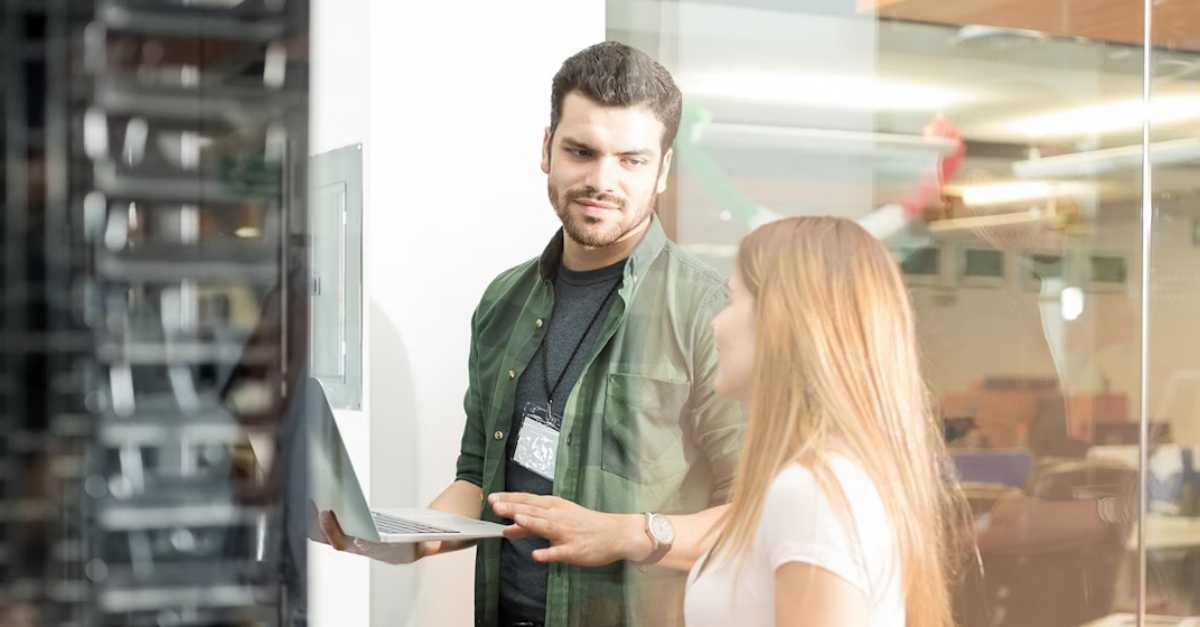
How the IoT Impacts Maintenance Management
IoT will continue to have a massive impact in the maintenance management field - and it's a technology that you shouldn't sleep on.
Solutions
Resources
Browse our full library of resources all in one place, including webinars, whitepapers, podcast episodes, and more.
Support
Looking for access to technical support, best practices, helpful videos, or training tools? You’ve come to the right place.
About Accruent
Get the latest information on Accruent, our solutions, events, and the company at large.
As manufacturers digitally transform, their maintenance practices also need to evolve. Shifting to proactive forms of maintenance makes sense, but to do it effectively, they need to use a computerised maintenance management system. Here are five reasons why.
Manufacturing computerised maintenance management systems (CMMS) have been around for decades. Yet, while not considered the latest in smart manufacturing technologies, CMMS is just as much a part of today’s smart manufacturing solutions as the industrial IoT and AI.
In fact, today’s CMMS are sophisticated solutions that have proven themselves over many years and the impact they’re having on manufacturing continues unabated. But as technology, manufacturing techniques, workforce skills and equipment all evolve, so does the scope of CMMS. Irrespective of the advancements made to date, there’s a long way to go for the software solution and the industry.
Here’s where the manufacturing industry stands today – and how CMMS systems continue to make an impact.
Despite advances in technology and maintenance strategies, unplanned downtime remains a big issue. According to this report, in the manufacturing industry, unplanned downtime costs approximately $260,000 per hour, with manufacturers experiencing approximately 800 hours every year. The leading cause? Ageing equipment. That said, poor or inadequate maintenance practices directly impact the bottom line, as well – one study estimated that the total annual costs associated with maintenance is approximately $222 billion.
That’s a massive financial hole that needs to be plugged and it’s indicative that much work remains to be done if manufacturers are to prevent the problems plaguing the sector. And while technology is perpetuating a raft of shiny new tools hitting the market, the reality is that doing more with existing, proven and well-established solutions is a much more likely route to success. Little surprise then that Future Market Insights predicts the CMMS market is projected to reach $4215 million by 2033, up from $1636 million by 2022.
That’s a spectacular growth rate in little over a decade. But when you consider the ways in which CMMS is continuing to transform manufacturing, it’s easy to see how it will be realised.
This is no longer a question of ‘do manufacturing companies need CMMS’? It’s quite clear, by now, that modern manufacturing organizations do need a dedicated work order management and preventive maintenance system.
The real question? Are manufacturing companies making the most out of their CMMS systems, do they have the best processes in place, and can they do more with what they’ve got? Despite the ubiquitous awareness of CMMS, the answers to these particular questions remain unequivocally opaque.
But that is where Accruent can help. Our Maintenance Connection solution is used by some of the world’s biggest manufacturers. It is designed to seamlessly integrate with your existing systems, and whether it’s work orders or inventory management, our expert team can identify precisely where a CMMS can add the most value. If you still have doubts, consider this. Boston Consulting Group analysed data in 2020 and found that digitally integrated companies’ annual earnings grew 1.8 times more than their non-digitally enabled competitors, while their enterprise value increased 2.4 times.
We want to help you realise that growth.
If you're a manufacturer looking to streamline your maintenance processes, then a computerised maintenance management system (CMMS) could be just what you need. To get started, check out these helpful resources:
If you're interested in finding out how a CMMS can benefit your organisation, get in touch with one of our experts today.
IoT will continue to have a massive impact in the maintenance management field - and it's a technology that you shouldn't sleep on.
Explore the challenges of estate management, from cost control to portfolio complexity, and discover how Accruent Lucernex provides comprehensive ...
Discover why food and beverage manufacturers experience asset downtime and learn strategies to overcome challenges and transform your processes.
Subscribe to stay up to date with our latest news, resources and best practices