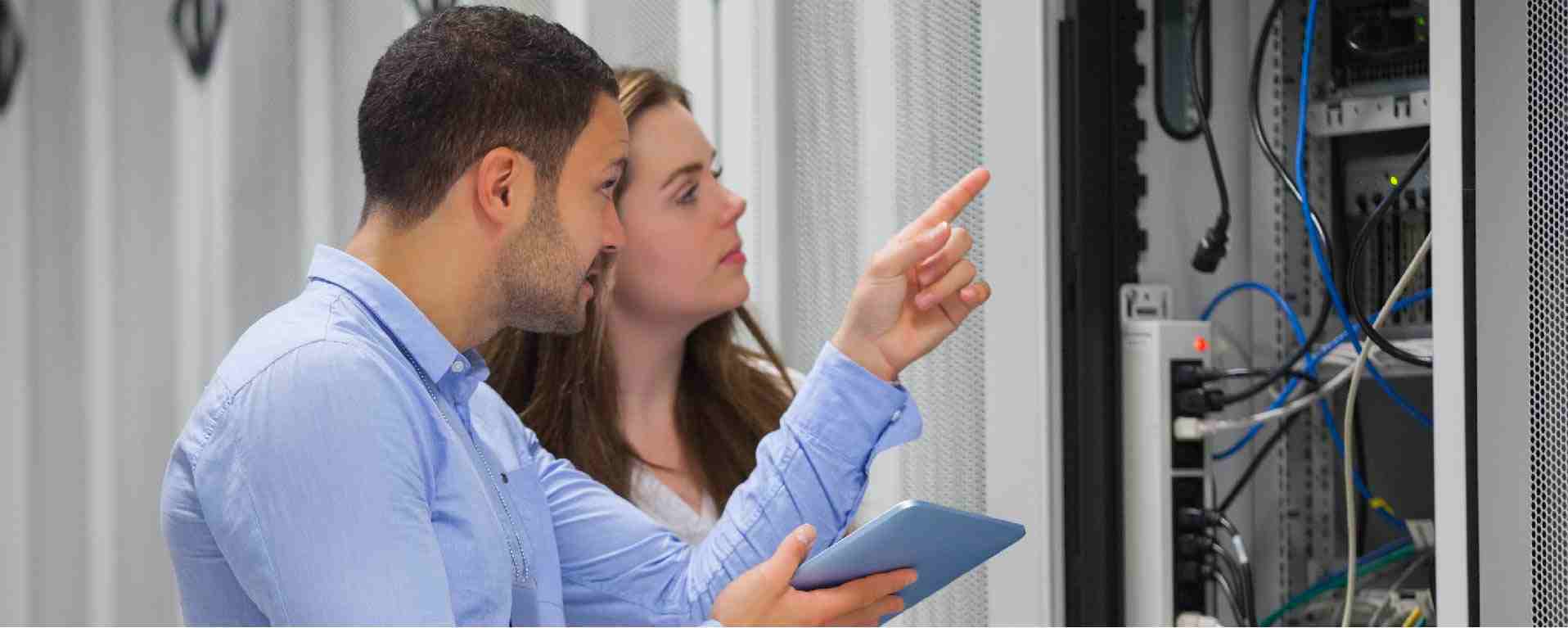
How to Measure CMMS ROI & Performance
Want to know how to measure your true CMMS ROI and performance? Here's how to get the numbers.
Solutions
Workplace Management Solutions
Real Estate Management Solutions
Maintenance Management Solutions
Energy Management Solutions
Engineering Document Management Solutions
Asset Management Solutions
Automate campus scheduling for classes, meetings, and exams with our EMS software.
Plan and manage conferences effortlessly with EMS software to impress guests and streamline operations.
Boost workplace flexibility and maximize space use with seamless desk and room booking.
Organize workplace or campus events smoothly, creating memorable experiences.
Optimize workspace, manage allocations efficiently, and reduce costs with our space management solutions.
Deliver projects on time and within budget by improving communication, collaboration, and efficiency with our software.
Streamline lease accounting for ASC 842, IFRS, and GASB compliance.
Manage leases efficiently by tracking key dates, analyzing costs, and ensuring compliance.
Centralize data and analytics for better insights, faster negotiations, and revenue growth.
Centralize facility and asset maintenance, automate work orders, and ensure compliance with our CMMS software.
Extend asset life, reduce downtime, and prevent costly repairs with data-driven monitoring.
Prevent equipment failures and extend asset life by detecting and addressing issues early.
Make sustainable, cost-efficient energy decisions by monitoring and optimizing power consumption.
Remotely monitor and control equipment with real-time data to predict issues, boost efficiency, and reduce downtime.
Easily share and collaborate on documents, creating a single source of truth for engineers and contractors.
Manage and analyze assets across their lifecycle to schedule maintenance, reduce downtime, and extend lifespan.
Improve visibility, automate work orders, and ensure compliance for efficient facility and asset management.
Resources
Browse our full library of resources all in one place, including webinars, whitepapers, podcast episodes, and more.
Support
Looking for access to technical support, best practices, helpful videos, or training tools? You’ve come to the right place.
About Accruent
Get the latest information on Accruent, our solutions, events, and the company at large.
Discover five key performance indicators for maintenance departments and identify benchmarks to improve performance and safety.
By Rick Joslin, Senior Advisor, Healthcare Strategy & Senior Solutions Architect, Healthcare
Implementing and using a computerized maintenance management system (CMMS) can provide critical data values that assist maintenance managers in identifying, distributing, and correcting deficiencies as well as managing scheduled maintenance requirements.
Unfortunately, many healthcare facilities management (HFM) departments are focused on solving the most recent issues and often find themselves forgetting other issues that require their attention. If your team is not monitoring what is going on in the EoC—past as well as present—trouble is sure to follow. This monitoring is critical for an HFM maintenance department to ensure the whole EoC is maintained to ensure your customers have the highest-quality experience possible.
Each organization should identify specific Key Performance Indicators (KPIs) and manage their departments towards those KPIs. Although KPIs may vary by organization, here are five that can drive improvements in departmental performance.
Ensuring your teams perform work orders as scheduled should be one of the top KPIs your organization monitors.
Within this KPI you should have two perspectives: real-time (last 30 days to date) and historical (trending over the prior 6 months). The first view will let you know how your team is doing on requests fresh in the minds of your customers. The second will let you know if there are issues of regular, repetitive tardiness when performing work orders. Either way, this measurement is the one your customers remember the most, whether or not you got things done when you said you would.
Identifying when a job should be completed—then tracking how well your team meets those dates—will help to better understand the efficiency, or lack thereof, of your maintenance workforce.
Setting scheduled completion dates can come from time-based priority codes or using the “date needed” field. Regardless of the method, ensuring your teams know how this is done and informing your customers of the schedule will help enforce measurements and keep your teams focused on customer-service.
HFM departments should monitor how well their teams complete their jobs as assigned within established guidelines. To this end, HFM departments should augment overdue analytics with active monitoring of any work request that has been open more than a specific number of days. Generally focused on unscheduled work (non-PMs), each type of work request can have various thresholds, but few work requests should be open more than 14 days without management being involved.
Common, general timeframes are:
If you do not have this measurement—often referred to as Service Level Agreements or SLAs—you should implement them. SLAs let your team know the expectation of their performance, gives your customers an expectation of service and allows you to move the HFM department into a service-orientated organizational asset.
In the example above, it is likely that some of the overdue work orders have been maintained or performed, but the paperwork was lost in the process. Other requests may also need some research into their current state. Either way, unless you measure, review and enforce each individual work order, it can be difficult to see if your team is getting things done in a timely fashion.
Come see us at ASHE Booth 637 on July 14-17, 2019 in Baltimore.
Measuring how long it takes your team to perform certain processes is critical to transforming HFM departments into a customer-focused entity. Turnaround time—in any of its forms—is a measurement that speaks volumes about the efficiency of your department. We use the term “turnaround” to identify the measurement related to the life of a work request.
Turnaround time is typically broken into three key areas, listed in the order they are most commonly found:
Each area requires different processes and expectations, and each build upon the prior level. Completion and turnaround times are normally measured in days (completion time should be measured against any SLAs in place) while response times are usually measured in minutes.
Turnaround time is by far the most common measurement and is an indicator of how well your HFM maintenance staff can execute established policies and procedures from start to finish. Response times can illustrate how well your staffing levels can meet the service\maintenance demands of the organization and its environment, while completion times can show how well your total HFM team—organizational staff, vendors, suppliers—work together to get a job done.
Knowing how much time your team has available, how much time they spent completing jobs and how much time they need to perform scheduled maintenance in the future will ensure your HFM department has a plan to meet the maintenance needs of your EoC.
Measuring past expenditures of labor hours and combining this with decision-making data is critical to the smooth and successful operation of any HFM department. We will look at three forms of labor analysis and identify the benefits of each.
Most HFM departments will measure the time spent on activities by their department in various fashions. Here are the most common:
Tallying how your teams are using their time—and regularly addressing issues related to time—will help ensure the time your department does have is well utilized.
Every HFM department repeats recurring activities and should have a close estimation of the time needed. This measurement involves scheduled events—such as preventive maintenance, planned events, inspections and other regularly occurring and repetitive activities involving your team.
This measurement combines what you spent (on average per month) and what you need (next 12 months) before providing analytics of how well you can meet those expected needs.
Your HFM department may need to develop, train and enforce new processes to ensure you can take advantage of these metrics, but once done, they provide immense value to planning manpower assignments.
For example, say you have 10 FTEs in your HFM department providing an average of 1,600 hours for a month. If you know you need 900 hours for PMs and you average 700 hours for repairs, you can determine how losing a single FTE for a week will affect your maintenance efforts and allow you to plan for additional vendor support. These measurements also support manpower justification, maintenance budget, and other departmental planning efforts.
Every HFM maintenance department has a backlog of work to be accomplished. However, the trick is to maintain and manage a healthy backlog. Backlog management requires a department to know how many internal resource hours they have available to them—both full-time and part-time employees—so they can gauge how to distribute their workload, and how much vendor\contractor time will be needed.
A key component to backlog management is to strive to maintain the FIFO process and avoid the more-common LIFO process. FIFO (First In, First Out) means the older requests are worked on first, where the LIFO (Last In, First Out) goes after the most recent requests first. LIFO will almost always lead to aged, forgotten and incomplete requests.
Developing performance indicators and identifying measurable departmental metrics are key factors in progressing towards a customer-focused value-based HFM department. Using these KPIs as a starting point will help your team deliver quality service while ensuring a safe EoC for everyone.
To further understand how to measure and use your KPIs, contact us today.
Want to know how to measure your true CMMS ROI and performance? Here's how to get the numbers.
Explore the key performance indicators to track to ensure your management software is increasing your organization’s productivity.
Explore how to identify and develop key performance indicators and success metrics for your organization.
Subscribe to stay up to date with our latest news, resources and best practices