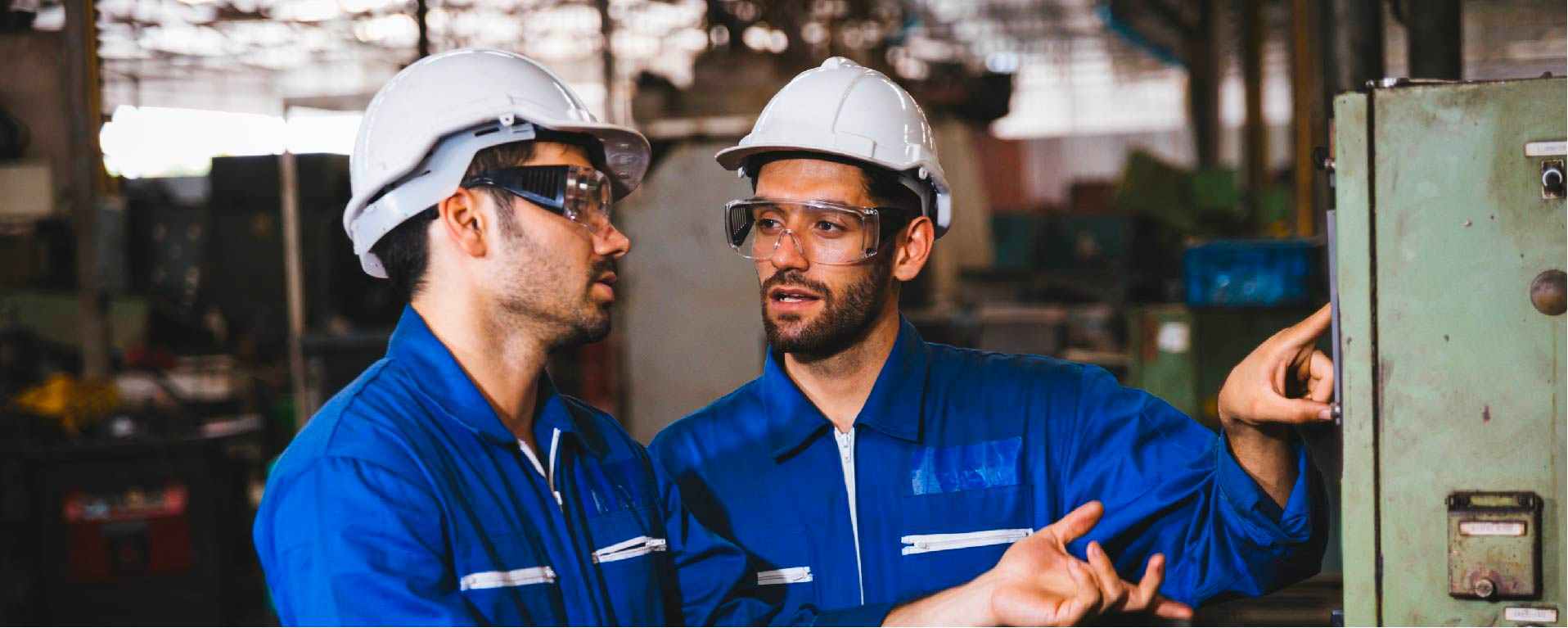
How Preventive Maintenance Schedules Benefit Your Company
Preventive maintenance is crucial for any manufacturing organization, helping to drive down costs, improve efficiency and more. Here's how to get it ...
Solutions
Workplace Management Solutions
Real Estate Management Solutions
Maintenance Management Solutions
Energy Management Solutions
Engineering Document Management Solutions
Asset Management Solutions
Automate campus scheduling for classes, meetings, and exams with our EMS software.
Plan and manage conferences effortlessly with EMS software to impress guests and streamline operations.
Boost workplace flexibility and maximize space use with seamless desk and room booking.
Organize workplace or campus events smoothly, creating memorable experiences.
Optimize workspace, manage allocations efficiently, and reduce costs with our space management solutions.
Deliver projects on time and within budget by improving communication, collaboration, and efficiency with our software.
Streamline lease accounting for ASC 842, IFRS, and GASB compliance.
Manage leases efficiently by tracking key dates, analyzing costs, and ensuring compliance.
Centralize data and analytics for better insights, faster negotiations, and revenue growth.
Centralize facility and asset maintenance, automate work orders, and ensure compliance with our CMMS software.
Extend asset life, reduce downtime, and prevent costly repairs with data-driven monitoring.
Prevent equipment failures and extend asset life by detecting and addressing issues early.
Make sustainable, cost-efficient energy decisions by monitoring and optimizing power consumption.
Remotely monitor and control equipment with real-time data to predict issues, boost efficiency, and reduce downtime.
Easily share and collaborate on documents, creating a single source of truth for engineers and contractors.
Manage and analyze assets across their lifecycle to schedule maintenance, reduce downtime, and extend lifespan.
Improve visibility, automate work orders, and ensure compliance for efficient facility and asset management.
Resources
Browse our full library of resources all in one place, including webinars, whitepapers, podcast episodes, and more.
Support
Looking for access to technical support, best practices, helpful videos, or training tools? You’ve come to the right place.
About Accruent
Get the latest information on Accruent, our solutions, events, and the company at large.
Do you know how to establish an effective reliability and maintenance policy? Read on to learn the five basic steps to outlining and implementing a plan.
When it comes to your preventive maintenance program, you can experience substantial gains early on by simply becoming less focused on reactive issues and more focused on preventing breakdowns from happening. For instance, it’s no secret that a strong preventive maintenance program can nearly eliminate unscheduled downtime and improve the quality of work from your team.
Without a long-term vision, you may be selling your team short. Understanding where you want your maintenance organization to be in the next three or five years can ensure that you are aligned with the broader goals and objectives of the organization, as well as ensure that your maintenance activities are contributing to that success.
Developing a reliability and maintenance policy can help you drive this vision forward and cement your success within the organization.
A reliability and maintenance policy serves as an internal communication document for the entire organization to understand the goals of your preventive maintenance program and how you measure success.
A reliability and maintenance policy includes essential details, such as:
Creating and implementing a reliability and maintenance policy will take time, as there are several key stakeholders that will have to be involved throughout the process. However, once in place, it provides clear objectives and KPIs to measure your team’s success.
Understanding exactly how you are conducting preventive maintenance and where you may have gaps in your process can help you determine where you want to be in one year, three years or even five years. Having a clear outline of this will help drive the direction of your reliability and maintenance policy. As part of this, you should have an understanding of preventive maintenance processes already in place and their current performance.
Once you understand where you are, know where you want to go. In doing so, you can clearly see where you need to measure your team and preventive maintenance program to gauge success. Understanding your KPIs early on can help you use benchmarks to have a consistent way to evaluate your progress along the way.
Potential KPIs that your team can manage:
An improvement plan serves as the crux for your reliability and maintenance policy. It can also be the most difficult part of the policy to create, as it does require you to take an honest look at where your team can improve.
When you are putting together your improvement plan, involve stakeholders across the organization to understand where they see gaps in your processes and areas for improvement.
Most reliability and maintenance policies address a finite period of time. Common timelines include one, three and five years. Understanding internal processes and what’s preferred by your organization can determine the appropriate timeline. In addition, knowing your gaps and expectations for improvement can drive your timeline as well.
Unlike other programs within the maintenance team, this type of policy works best when you have buy-in from other stakeholders within the organization. It can help give the organization more visibility into your team and their contributions to the business’ goals. Because of this, bringing external stakeholders within the policy development process can ensure that you are in line with expectations and able to contribute to the broader objectives of the organization.
Preventive maintenance is crucial for any manufacturing organization, helping to drive down costs, improve efficiency and more. Here's how to get it ...
Explore how a planned preventive maintenance program can help you optimize your operations and reduce your most frustrating recurring pain points.
How comprehensive asset intelligence, effective preventive maintenance, and efficient labor scheduling can lead to success in the chemical industry.
Subscribe to stay up to date with our latest news, resources and best practices