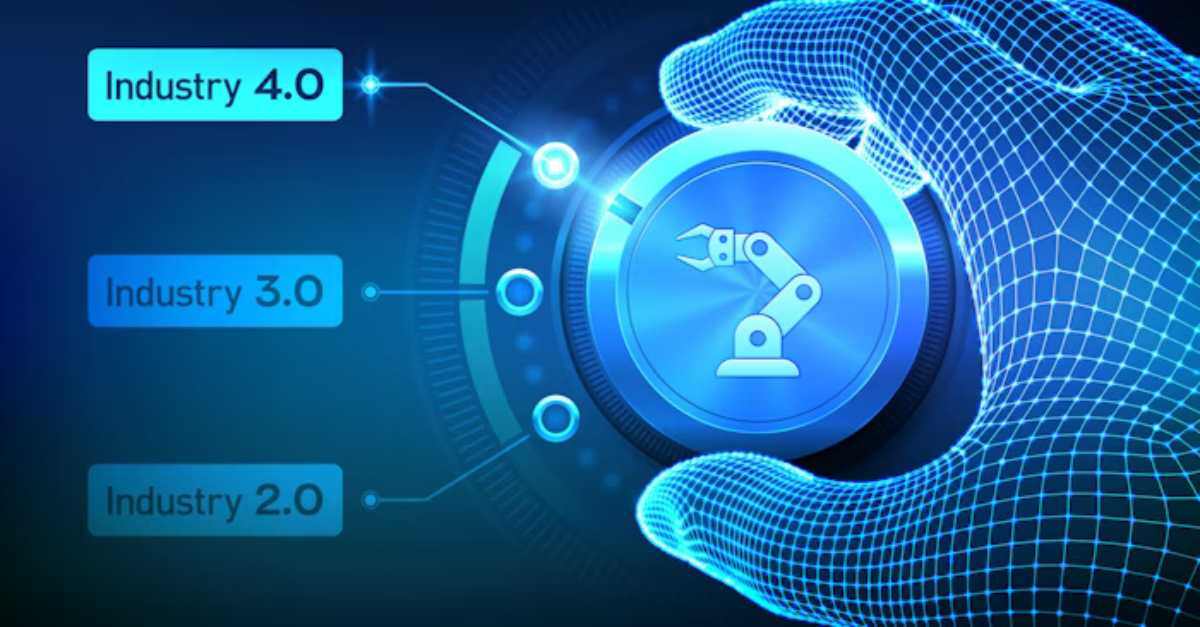
Industry 4.0: What it Means and How to Get it Right
Industry 4.0 literacy has become crucial for manufacturing organizations. Here's how to increase buy-in and invest in tools that really work.
Solutions
Workplace Management Solutions
Real Estate Management Solutions
Maintenance Management Solutions
Energy Management Solutions
Engineering Document Management Solutions
Asset Management Solutions
Automate campus scheduling for classes, meetings, and exams with our EMS software.
Plan and manage conferences effortlessly with EMS software to impress guests and streamline operations.
Boost workplace flexibility and maximize space use with seamless desk and room booking.
Organize workplace or campus events smoothly, creating memorable experiences.
Optimize workspace, manage allocations efficiently, and reduce costs with our space management solutions.
Deliver projects on time and within budget by improving communication, collaboration, and efficiency with our software.
Streamline lease accounting for ASC 842, IFRS, and GASB compliance.
Manage leases efficiently by tracking key dates, analyzing costs, and ensuring compliance.
Centralize data and analytics for better insights, faster negotiations, and revenue growth.
Centralize facility and asset maintenance, automate work orders, and ensure compliance with our CMMS software.
Extend asset life, reduce downtime, and prevent costly repairs with data-driven monitoring.
Prevent equipment failures and extend asset life by detecting and addressing issues early.
Make sustainable, cost-efficient energy decisions by monitoring and optimizing power consumption.
Remotely monitor and control equipment with real-time data to predict issues, boost efficiency, and reduce downtime.
Easily share and collaborate on documents, creating a single source of truth for engineers and contractors.
Manage and analyze assets across their lifecycle to schedule maintenance, reduce downtime, and extend lifespan.
Improve visibility, automate work orders, and ensure compliance for efficient facility and asset management.
Resources
Browse our full library of resources all in one place, including webinars, whitepapers, podcast episodes, and more.
Support
Looking for access to technical support, best practices, helpful videos, or training tools? You’ve come to the right place.
About Accruent
Get the latest information on Accruent, our solutions, events, and the company at large.
In grocery, reducing energy spend can translate directly to decreased waste and increased profit. Here's how to get it right.
Table of contents
Now you are ready to move your organization beyond these types of projects. Consider the benefits of an energy management system that interfaces with your controls systems to help reduce energy costs while maintaining the customer experience.
An energy management system gives you information with key recommendations to change your business process and drive savings.
Industry 4.0 literacy has become crucial for manufacturing organizations. Here's how to increase buy-in and invest in tools that really work.
The right IoT tools can help healthcare organizations overcome their most complex logistical challenges. Here's how to get it right.
Get hybrid work right by learning how to balance employee preferences with overall business goals — and see how the right technology can help.
Subscribe to stay up to date with our latest news, resources and best practices