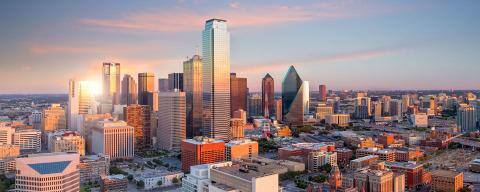
How Lucky Eagle Casino Reduced Maintenance Costs with a CMMS
Learn how Lucky Eagle Casino streamlined work order management and reduced maintenance costs with Maintenance Connection.
Solutions
Workplace Management Solutions
Real Estate Management Solutions
Maintenance Management Solutions
Energy Management Solutions
Engineering Document Management Solutions
Asset Management Solutions
Automate campus scheduling for classes, meetings, and exams with our EMS software.
Plan and manage conferences effortlessly with EMS software to impress guests and streamline operations.
Boost workplace flexibility and maximize space use with seamless desk and room booking.
Organize workplace or campus events smoothly, creating memorable experiences.
Optimize workspace, manage allocations efficiently, and reduce costs with our space management solutions.
Deliver projects on time and within budget by improving communication, collaboration, and efficiency with our software.
Streamline lease accounting for ASC 842, IFRS, and GASB compliance.
Manage leases efficiently by tracking key dates, analyzing costs, and ensuring compliance.
Centralize data and analytics for better insights, faster negotiations, and revenue growth.
Centralize facility and asset maintenance, automate work orders, and ensure compliance with our CMMS software.
Extend asset life, reduce downtime, and prevent costly repairs with data-driven monitoring.
Prevent equipment failures and extend asset life by detecting and addressing issues early.
Make sustainable, cost-efficient energy decisions by monitoring and optimizing power consumption.
Remotely monitor and control equipment with real-time data to predict issues, boost efficiency, and reduce downtime.
Easily share and collaborate on documents, creating a single source of truth for engineers and contractors.
Manage and analyze assets across their lifecycle to schedule maintenance, reduce downtime, and extend lifespan.
Improve visibility, automate work orders, and ensure compliance for efficient facility and asset management.
Resources
Browse our full library of resources all in one place, including webinars, whitepapers, podcast episodes, and more.
Support
Looking for access to technical support, best practices, helpful videos, or training tools? You’ve come to the right place.
About Accruent
Get the latest information on Accruent, our solutions, events, and the company at large.
The latest Maintenance Connection capabilities can help organizations increase equipment lifespan, establish maintenance schedules, and more.
Table of contents
Professionals in asset-heavy industries face many day-to-day challenges with maintenance operations, including unnecessary downtime, decreased labor efficiency, low visibility into work orders and low asset lifecycle.
Reactive maintenance practices and outdated legacy systems can exacerbate these concerns, making it difficult to track asset histories, schedule PMs or effectively execute preventive maintenance.
To efficiently address these concerns, Accruent has released Maintenance Connection CMMS system. Now, Maintenance Connection v8.9 – the latest evolution of Maintenance Connection available to on-premise customers – offers exciting new added functionality. These improvements can help asset-heavy businesses to effectively reach overarching goals and:
Effective preventive maintenance software is the key to any successful CMMS implementation, allowing for streamlined operations and increased ROI.
Companies with ineffective preventive maintenance will see costly consequences, including reduced safety, increased unplanned downtime and reduced asset lifecycle. They’ll also have lower visibility into parts inventory and work order history, and they will fail to consistently focus on high-priority work.
With effective preventive maintenance, on the other hand, business see benefits like:
To help strengthen such capabilities, we’re enhancing the automated generation of preventive maintenance work orders to speed up generation time. Now, PM generation can be anywhere from 2 to 10 times faster than it was previously, depending on configuration and other variables.
This makes it even easier for businesses to create work orders, prioritize them, and gather any data they need for bigger-picture insights.
A CMMS can help maintenance departments better meet safety initiatives and comply with regulatory, industry, geographic and other audits:
Two new preferences have been added that give customers even more control over how many record changes are kept in audit history. Previously, audit history was capped at 500,000 record changes. Now, customers can raise that ceiling using time or record-based retention policies to meet their particular audit history needs and to ensure that they always have the right information at hand to maintain compliance.
A top-tier CMMS tool can help give you peace of mind when it comes to the health of your team and the safety of your assets by:
With this latest feature update, users can now be required to record readings for meters or specifications before marking a work order task as complete. This additional check can help ensure that there are no oversights when it comes to asset function and process validation that the work has been appropriately completed. In the big picture, this can improve plant safety and uptime.
Maintenance Connection v8.9 also includes over 70 enhancements and fixes to the Maintenance Connection, MC Express and the Maintenance Connection API.
These include:
Learn how Lucky Eagle Casino streamlined work order management and reduced maintenance costs with Maintenance Connection.
In many cases, reactive maintenance is more costly - and less efficient - than preventive maintenance. Here's how to eliminate unnecessary reactive ...
Are you doing everything you can to keep maintenance costs to a minimum? Here are 5 effective ways to cut costs and optimize your maintenance plans.
Subscribe to stay up to date with our latest news, resources and best practices