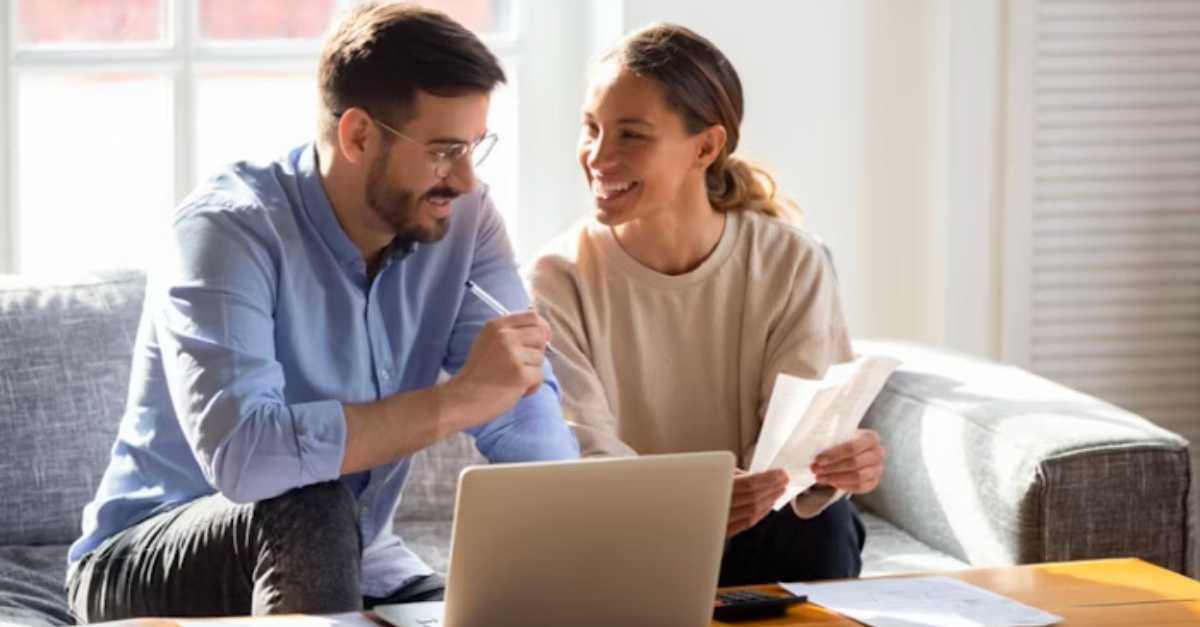
Preparing for Implementation: Accruent’s Lx Contracts
What can you expect from your Lx Contracts implementation? Prepare your organization so you can meet compliance goals, centralize data, and boost ...
Solutions
Workplace Management Solutions
Real Estate Management Solutions
Maintenance Management Solutions
Energy Management Solutions
Engineering Document Management Solutions
Asset Management Solutions
Automate campus scheduling for classes, meetings, and exams with our EMS software.
Plan and manage conferences effortlessly with EMS software to impress guests and streamline operations.
Boost workplace flexibility and maximize space use with seamless desk and room booking.
Organize workplace or campus events smoothly, creating memorable experiences.
Optimize workspace, manage allocations efficiently, and reduce costs with our space management solutions.
Deliver projects on time and within budget by improving communication, collaboration, and efficiency with our software.
Streamline lease accounting for ASC 842, IFRS, and GASB compliance.
Manage leases efficiently by tracking key dates, analyzing costs, and ensuring compliance.
Centralize data and analytics for better insights, faster negotiations, and revenue growth.
Centralize facility and asset maintenance, automate work orders, and ensure compliance with our CMMS software.
Extend asset life, reduce downtime, and prevent costly repairs with data-driven monitoring.
Prevent equipment failures and extend asset life by detecting and addressing issues early.
Make sustainable, cost-efficient energy decisions by monitoring and optimizing power consumption.
Remotely monitor and control equipment with real-time data to predict issues, boost efficiency, and reduce downtime.
Easily share and collaborate on documents, creating a single source of truth for engineers and contractors.
Manage and analyze assets across their lifecycle to schedule maintenance, reduce downtime, and extend lifespan.
Improve visibility, automate work orders, and ensure compliance for efficient facility and asset management.
Resources
Browse our full library of resources all in one place, including webinars, whitepapers, podcast episodes, and more.
Support
Looking for access to technical support, best practices, helpful videos, or training tools? You’ve come to the right place.
About Accruent
Get the latest information on Accruent, our solutions, events, and the company at large.
You’ve planned for today’s workload. But what about tomorrow, next week or next year? Learn what it takes to improve retail operations in the long-term.
Retail stores contain a variety of equipment and use many contractors, from plumbing, lighting, refrigeration, HVAC, etc. Some of these contractors may only be authorized to work on certain equipment or in certain geographies.
When managing a network of contractors becomes too complex, grocery and retail chains can turn to contractor management systems.
Contractor management systems reduce duplicate work orders, unnecessary service calls, invoicing errors and inaccurate time reporting. Ultimately, these systems help you get the right technicians on-site faster to resolve issues and make preventive maintenance easier.
For further information on how to improve service processes, contact us today.
What can you expect from your Lx Contracts implementation? Prepare your organization so you can meet compliance goals, centralize data, and boost ...
Complex calculations. Audit trails. Reporting needs. Find out why spreadsheets aren't built to handle lease accounting requirements — and what ...
GASB 87 Implementation Guide Information On This Page: What is GASB 87 When Does GASB 87 Need to Be Implemented? Implementation Guide: How Can ...
Subscribe to stay up to date with our latest news, resources and best practices