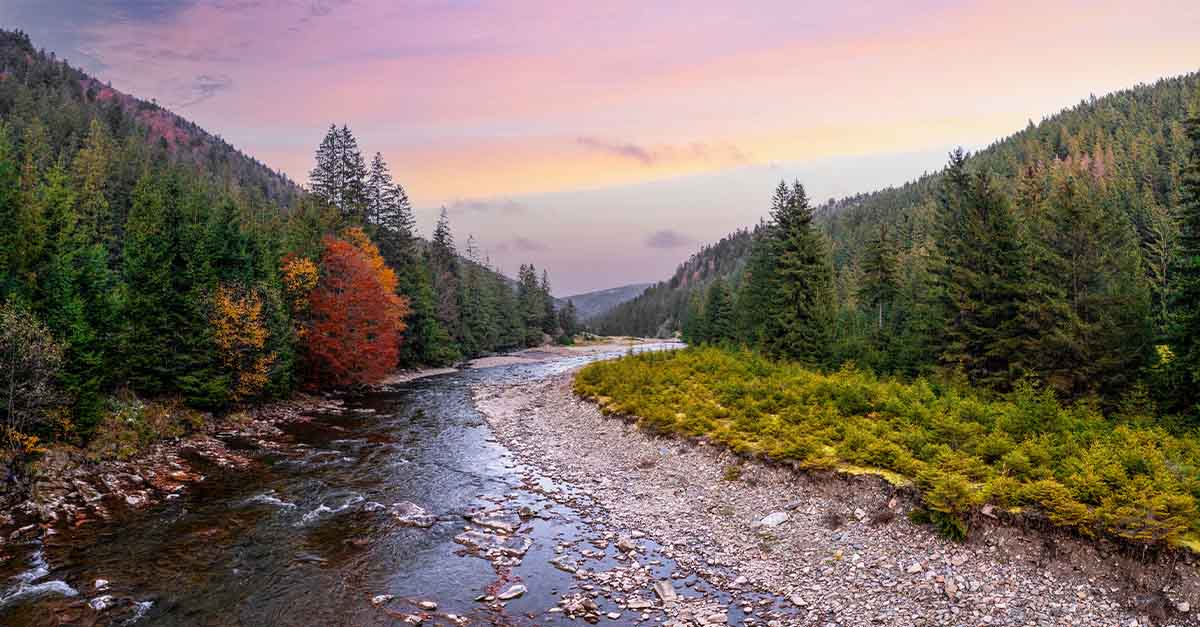
How Northern Water Transformed Operations with Maintenance Connection
Discover how Northern Water improved record-keeping, maintenance, reimbursements, and safety for critical infrastructure with Maintenance Connection.
Solutions
Workplace Management Solutions
Real Estate Management Solutions
Maintenance Management Solutions
Energy Management Solutions
Engineering Document Management Solutions
Asset Management Solutions
Automate campus scheduling for classes, meetings, and exams with our EMS software.
Plan and manage conferences effortlessly with EMS software to impress guests and streamline operations.
Boost workplace flexibility and maximize space use with seamless desk and room booking.
Organize workplace or campus events smoothly, creating memorable experiences.
Optimize workspace, manage allocations efficiently, and reduce costs with our space management solutions.
Deliver projects on time and within budget by improving communication, collaboration, and efficiency with our software.
Streamline lease accounting for ASC 842, IFRS, and GASB compliance.
Manage leases efficiently by tracking key dates, analyzing costs, and ensuring compliance.
Centralize data and analytics for better insights, faster negotiations, and revenue growth.
Centralize facility and asset maintenance, automate work orders, and ensure compliance with our CMMS software.
Extend asset life, reduce downtime, and prevent costly repairs with data-driven monitoring.
Prevent equipment failures and extend asset life by detecting and addressing issues early.
Make sustainable, cost-efficient energy decisions by monitoring and optimizing power consumption.
Remotely monitor and control equipment with real-time data to predict issues, boost efficiency, and reduce downtime.
Easily share and collaborate on documents, creating a single source of truth for engineers and contractors.
Manage and analyze assets across their lifecycle to schedule maintenance, reduce downtime, and extend lifespan.
Improve visibility, automate work orders, and ensure compliance for efficient facility and asset management.
Resources
Browse our full library of resources all in one place, including webinars, whitepapers, podcast episodes, and more.
Support
Looking for access to technical support, best practices, helpful videos, or training tools? You’ve come to the right place.
About Accruent
Get the latest information on Accruent, our solutions, events, and the company at large.
Table of contents
Different plants onboarded
Assets in the system
Maintenance plans
CAREL is one of the main global manufacturers of control solutions for air conditioning, cooling and heating, and air quality improvement systems. Founded in Italy in 1973 for the construction of electrical cabinets, the company soon expanded its offerings, producing electrical components for HVAC (Heating, Ventilation, and Air Conditioning) that allow users to better control conditioning systems.
Starting in the 1990s, the company expanded through various new plants, acquisitions, and branches. Today, CAREL offers components, electric panels, inverters, and valves for the control of cooling gases.
One of the main benefits of the implementation is the visibility of the process at the Group level, thanks to maintenance plans standardized across all production sites.”
-Franco Faletti, Group Production Engineering Manager, and Alberto Mazzetto, TPM Leader
Before implementing a dedicated CMMS solution across locations and plants, CAREL faced opportunities for improvement, including:
CAREL’s modernization efforts are largely shaped and driven by the technologies they utilize. In 2023, they adopted Maintenance Connection CMMS (Computerized Maintenance Management System) to organize and improve the efficiency of their maintenance systems through a Group vision.
After a thorough evaluation and selection of possible partners, Maintenance Connection was chosen as the most suitable solution for the company. Then, a multi-disciplinary team devoted to the software implementation was created in conjunction with One Team and Accruent.
CAREL, supported by One Team, developed the first pilot project to implement the setup of the software in its headquarters, subsequently exporting the same model to six other factories.. In seven months, the system was set up and operationalized in seven plants total, including more than four thousand assets and over five hundred maintenance plans, with local translation for each plant.
There are many key benefits that the Maintenance Connection implementation has delivered to CAREL:
As of today, CAREL is working on adding spare parts management and skill matrices functionalities.
Another important objective for the future is the application of Artificial Intelligence to improve the management of information derived from manuals and data observed in the field. This will optimize the maintenance process and help effectively manage potential failures.
Discover how Northern Water improved record-keeping, maintenance, reimbursements, and safety for critical infrastructure with Maintenance Connection.
Discover how Maintenance Connection helped Watson-Marlow enhance operational efficiency, streamline workflows, and drive collaboration across teams.
A Leading Agricultural Cooperative Maximizes Equipment Uptime and Justifies Asset Purchasing With Maintenance Connection.
Subscribe to stay up to date with our latest news, resources and best practices