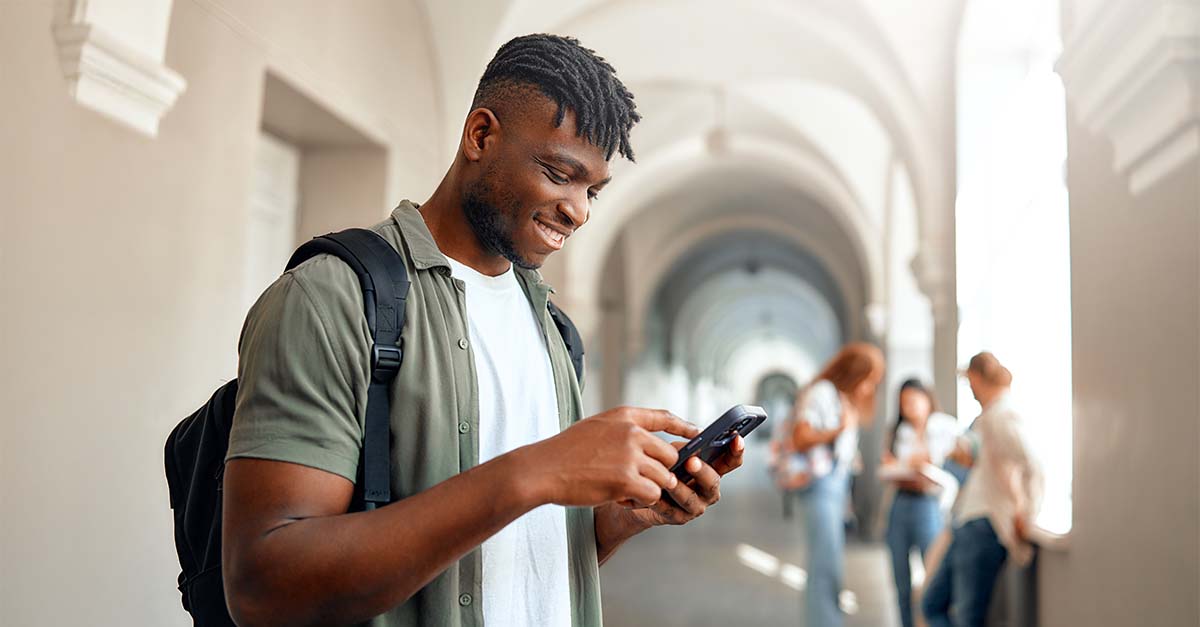
How the University of Regina Improved Maintenance and Operations with FAMIS 360
Discover how Northern Water improved record-keeping, maintenance, reimbursements, and safety for critical infrastructure with Maintenance Connection.
Solutions
Workplace Management Solutions
Real Estate Management Solutions
Maintenance Management Solutions
Energy Management Solutions
Engineering Document Management Solutions
Asset Management Solutions
Automate campus scheduling for classes, meetings, and exams with our EMS software.
Plan and manage conferences effortlessly with EMS software to impress guests and streamline operations.
Boost workplace flexibility and maximize space use with seamless desk and room booking.
Organize workplace or campus events smoothly, creating memorable experiences.
Optimize workspace, manage allocations efficiently, and reduce costs with our space management solutions.
Deliver projects on time and within budget by improving communication, collaboration, and efficiency with our software.
Streamline lease accounting for ASC 842, IFRS, and GASB compliance.
Manage leases efficiently by tracking key dates, analyzing costs, and ensuring compliance.
Centralize data and analytics for better insights, faster negotiations, and revenue growth.
Centralize facility and asset maintenance, automate work orders, and ensure compliance with our CMMS software.
Extend asset life, reduce downtime, and prevent costly repairs with data-driven monitoring.
Prevent equipment failures and extend asset life by detecting and addressing issues early.
Make sustainable, cost-efficient energy decisions by monitoring and optimizing power consumption.
Remotely monitor and control equipment with real-time data to predict issues, boost efficiency, and reduce downtime.
Easily share and collaborate on documents, creating a single source of truth for engineers and contractors.
Manage and analyze assets across their lifecycle to schedule maintenance, reduce downtime, and extend lifespan.
Improve visibility, automate work orders, and ensure compliance for efficient facility and asset management.
Resources
Browse our full library of resources all in one place, including webinars, whitepapers, podcast episodes, and more.
Support
Looking for access to technical support, best practices, helpful videos, or training tools? You’ve come to the right place.
About Accruent
Get the latest information on Accruent, our solutions, events, and the company at large.
Learn how Masters Gallery Foods selected Maintenance Connection and obtained immediate results by automating maintenance requests and reporting.
Table of contents
A family-owned company operating a multi-acre campus, Masters Gallery Foods is a leading national cheese supplier with one of the largest privately held cheese inventories in the United States. The company’s state-of-the-art manufacturing and distribution facility produces more than 200 million pounds of product a year and boasts numerous packaging lines to serve private label, retail, and foodservice customers around the world.
Prior to implementing Maintenance Connection, Masters Gallery Foods was using a computerized maintenance management system (CMMS) that was hard to use, offered no mobility, and had limited reporting. The team also used spreadsheets and often encountered unplanned maintenance. The company wanted to engage in asset maintenance proactively, gain a transparent view into the metrics to help attain organizational goals, and automate day-to-day maintenance tasks.
Masters Gallery Foods selected Maintenance Connection as its new CMMS and looked to obtain immediate results by automating maintenance requests and reporting. Automated reporting enables the company to measure and improve key metrics such as on-time preventive maintenance completion, wrench time to administration time, and planned vs unplanned maintenance.
Using Maintenance Connection, Masters Gallery Foods has focused on decreasing unplanned maintenance. With 2,000+ preventive maintenance schedules, the company has achieved an 85% planned maintenance to 15% unplanned maintenance split. With access to information on mobile devices, technicians are now able to improve response times and work as efficiently as possible.
Discover how Northern Water improved record-keeping, maintenance, reimbursements, and safety for critical infrastructure with Maintenance Connection.
Learn how Bay Area Hospital streamlined compliance, simplified maintenance request management and maximized transparency with Maintenance Connection.
Discover how a CMMS helps keep assets fully managed, improve equipment lifespan, increase preventive maintenance, eliminate downtime, and lower costs.
Subscribe to stay up to date with our latest news, resources and best practices