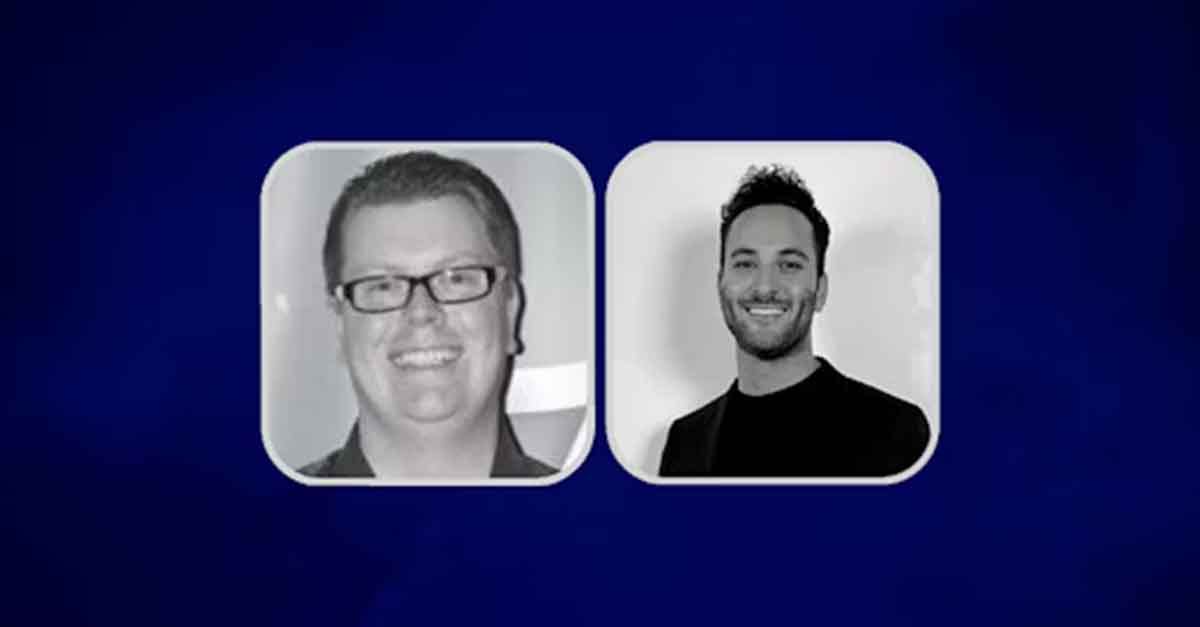
Collaborating to Solve Cross-Industry Pain Points: A Conversation with Meelad Nikpourian and Eric Cook
Here from Meelad Nikpourian and Eric Cook about the power of collaboration to solve cross-industry pain points.
Solutions
Workplace Management Solutions
Real Estate Management Solutions
Maintenance Management Solutions
Energy Management Solutions
Engineering Document Management Solutions
Asset Management Solutions
Automate campus scheduling for classes, meetings, and exams with our EMS software.
Plan and manage conferences effortlessly with EMS software to impress guests and streamline operations.
Boost workplace flexibility and maximize space use with seamless desk and room booking.
Organize workplace or campus events smoothly, creating memorable experiences.
Optimize workspace, manage allocations efficiently, and reduce costs with our space management solutions.
Deliver projects on time and within budget by improving communication, collaboration, and efficiency with our software.
Streamline lease accounting for ASC 842, IFRS, and GASB compliance.
Manage leases efficiently by tracking key dates, analyzing costs, and ensuring compliance.
Centralize data and analytics for better insights, faster negotiations, and revenue growth.
Centralize facility and asset maintenance, automate work orders, and ensure compliance with our CMMS software.
Extend asset life, reduce downtime, and prevent costly repairs with data-driven monitoring.
Prevent equipment failures and extend asset life by detecting and addressing issues early.
Make sustainable, cost-efficient energy decisions by monitoring and optimizing power consumption.
Remotely monitor and control equipment with real-time data to predict issues, boost efficiency, and reduce downtime.
Easily share and collaborate on documents, creating a single source of truth for engineers and contractors.
Manage and analyze assets across their lifecycle to schedule maintenance, reduce downtime, and extend lifespan.
Improve visibility, automate work orders, and ensure compliance for efficient facility and asset management.
Resources
Browse our full library of resources all in one place, including webinars, whitepapers, podcast episodes, and more.
Support
Looking for access to technical support, best practices, helpful videos, or training tools? You’ve come to the right place.
About Accruent
Get the latest information on Accruent, our solutions, events, and the company at large.
Hear from Accruent Solutions Consultant Jason Kraus about the power of Meridian EDMS and how it solves real pain points for customers in the field.
In this conversation with Industrial Talk’s Scott MacKenzie, Accruent Solutions Consultant Jason Kraus talks about the Meridian EDMS solution and how it helps our customers with their engineering document management needs. Specifically, he dives into:
Join the conversation!
Welcome to the Industrial Talk podcast with Scott MacKenzie. Scott is a passionate industry professional dedicated to transferring cutting-edge, industry-focused innovations and trends while highlighting the men and women who keep the world moving. So put on your hard hat, grab your work boots, and let's go!
01:34
Alright, once again, thank you very much for joining industrial talk and your continued support of a platform that is dedicated to industrial professionals all around the world. You're bold, you're brave, you dare greatly you're changing lives. You're changing the world as we speak. That's why we celebrate you on this platform. And we are broadcasting on-site. This is Accruent Insights which is a user community that is passionate about solving problems, identifying, collaborating, and just having a good time. It's all good. And we are at the Gaylord in Nashville, Tennessee, and it's the size of a small state. Did you get lost here, Jason?
02:21
Everything every night coming in. It's just, it's amazing. It's wonderful. But it's the type of place I'd never thought you'd ever see - a jungle inside of a hotel.
02:29
Can you imagine managing this asset?
02:32
Think about just cooling it in the Tennessee summer, to how many cubic yards of air to those things have to turn over every hour?
02:39
That and and it's an atrium, which is a greenhouse. That's what it is. It's just a greenhouse. And you walk out there and you get chilled.
02:48
Yeah. There's there's spots where it's like, “This is entirely too cold for a plant that looks like it’s growing bananas to be right next to me.”
02:55
like oh, my gosh, yeah, I know. I wouldn't want to just sort of crack open the here's the utility bill. Here it is. Oh, my gosh, they ran out of room on it. Exactly. They get their money, that's for sure. All right. For the listeners out there, Jason, give us a little background on who you are. Sure,
03:13
I am what's called a Solution Consultant with Accruent on the asset management side of the house. And the solution consultants in other organizations. They're called sometimes sales engineers, which is funny because I'm really neither sales nor an engineer. But I'm part of the sales team that helps our customers understand their technical needs, business fit, lay it help them lay out a roadmap to that goal that they’re after with technology and different elements like that. So
03:39
do you focus on a specific technology versus, you know, yep,
03:44
Yes, sir. My focus right now is around our Meridian product, which is engineering document management, project lifecycle management, especially for owner-operators, the people that are out there trying to keep these complicated industrial pieces of equipment running. You know, care and feeding evergreening of documentation and things like that. And the Meridian product has got a very long lifecycle. It's been on the market in one form or fashion for 30 years. So, you're talking software solutions, 30-year-old software solution, you'd back up you know how far that is. And when it was, you know, came into inception in Europe for some utility operators is how it was originally conceived. You know, it's, it's got a long shelf life, and customers all over the globe. So,
04:26
So take us through what it is.
04:31
So it is really focused around managing a lot of CAD files, models, data files, equipment, data files, equipment data files, equipment information, manage OEM manuals, OEM technical specs, you know, other engineering documentation that you've derived, as you've gone through and calculated your pump curves and your other elements like that related to pieces of equipment, and then storing them in a way that the people that are changing and updating the processes can make that change accurately and effectively and do it once and do it right, or the team in the field, those men and women there, they're going to find the right document, before they head out into the field the first time or even when they're in the field using our mobile device the right time, the first time making those updates with what they see in the field with red lines and things like that, which then starts that loop back through engineering to make sure things are accurate as they go through those processes.
05:25
I get it. Document Management has been a conversation for, well, since the beginning of time, since they were writing on papyrus. And it's always proven to be very challenging. And in the case of an industrial application, how does Meridian – there's there's some significant changes that are just happening from a technology perspective, and if it's such a legacy-type system, how do you keep it sort of nimble enough to, to use the technology and the innovation that's taking place?
05:59
Constant evolution, you know, it's the product again, started 30 years ago, it looks nothing like what it was 30 years ago. Oh, you know, it couldn't be, you know, that would look like Soviet software. something absolutely awful. But even then, the structure behind it has had to change and evolve and grow and is continuing to do so. You know, when you start talking BIM and digital twin, those sorts of elements like that, Meridian has to stay right up with those pieces, otherwise, we're going to be relegated out. And the biggest change that I've seen over the past even three years, has been the rapid acceleration of 3D modeling. You know, before, you know, it was maybe one out of five customers would say, “Hey, we're thinking about getting into the 3D space.” Now, it's 90%. And in fact, it's an oddity, if they say, “No, we really don't care about that 3d model anymore. You know, we don't want that. No.”
But that's the one thing that's really interesting about my role is I get to talk to customers, all over the country, all over the globe, and all sorts of different industries, then I've had exposure to some customers, one of them literally, they're still running a major facility with documents on sticks. Like the old records library stuck in there with blueprints hanging off of thse. Yeah, it was, it was like stepping into a time machine when they started showing me that stuff. So
07:15
this is sort of itchy, how do you take the those legacy documents? And and, and some of them are, I mean, these PNIDs are just they're, they're, well, they're lengthy, and they're out of date, monoliths lengthy and monolithic and out of date, yeah, how do you ensure that you can get them in there, updated so that it accurately reflects, you know, what's out in the field, and get it into the system that makes sense. I don't even know how you did
07:45
You eat that elephant one bite at a time, You start with digitizing first horse and scan them in, you do things like run them through OCR processes, which now make all of these old pencil lines from the 70s, human readable, some of which are going in different directions and things like that, so that you could find the document, that's probably step one, yeah, I can, it's digital, I can at least find an version of the document, right.
But, you know, now we start moving through other processes, where maybe are you going to reCAD the whole document, are you going to turn into what's called a vector where you've got, you know, a rasterized, two pieces of a document into a hybrid part where maybe I'm just recapping the southwest corner of that file. But, you know, the rest of it is still going to be the old pencil line. And systems like Meridian can manage that for those customers that really want to be very measured, and how they're changing and updating some of these files to limp their way into a fully electronic sort of formatted document.
08:42
So back to the reality is, is that, you know, today the document, right now, at noon, it's accurate. But at 12:01, it's not, you know, because that's, that's a dynamic reality. How does how does a system like Meridian, take that into account how to, because it's one thing for you, the, let's say, you're helping them do this? And then you got to let it go. And they've got to do it themselves, that they keep up with it? It can't be difficult.
No, how do you do it has to be simple. You have to have a technology platform, that one lets you find the file, lets you use it and let the democratization of data occur, so that the people in the field that have that knowledge, because they went there, and they saw where these pipes were connected, and the document’s wrong, I'm going to now using a mobile app or using our web app, I'm gonna just redraw where it is on the layer on top of that document. And that's going to flip a flag and engineering is gonna get notified that you've got something that needs some attention, you know, or things like that.
And the other element is, you know, it's not just document updates. We oftentimes forget about even just something as simple as an operator is doing their rounds or reliability technician is doing their rounds, and he or she hears something, sees something, smells something, and they just want to make a note of it to say, hey, you've got another round coming in 12 hours, if it's still loud call out on, you know, a work order. But let's check it one more time. So that's, you can use these documents and these technology elements as a shift turnover of information, a knowledge repository of things related to equipment, because, you know, otherwise, you're just gonna write it into a log sheet, and it's gonna go into a clipboard, and the next person who does their round is gonna grab the clean round sheet that they need, clip it over the top and not read your note. Yeah, but if everyone is looking at and using the same documents, you're gonna be able to democratize that information and gather it from everybody else that has added something.
10:43
So what's interesting is one, again, it Okay, so we have the technology to be able to do real time updates. Okay, great, fine. Here's a line, do this, now it reflects what's actually out in the field. Two: the, the reality, sometimes what happens is that sometimes you can't do a big bang.
11:10
I mean, it would be great to say, yesterday, we weren't here yesterday pulled everything out of a drawer, but Boom, look at it on the tablet and right view it from the coffee shop,
11:21
there's got to be sort of this sort of evolution, this journey of it, because well, now this is how you access it online here. But you still have to go over to the Map Room and find it over there. Yeah,
11:32
the Map Room or the the fixed inspection vaults where they've got your tml diagrams that are still pencil.
11:39
But that's that, again, does your team help with that sort of thing?
11:45
we can, we've got partners that we can bring in that are experts in digitizing some of these things, you know, we bring them in as part of the scope of work. And they then from that perspective, they're, they're tasked with doing that piece of work that they're best enabled to do. They've got, you know, OCR programs that have machine learning and AI built in so that when the text is going in different directions, and has three different handwriting styles, they're pulling all of that text out and making the entirety of the document searchable as you're going through those processes.
12:17
When somebody's scribbling, which it would be me, trust me, I would be, like, this is so important. And I put a little red checkmark by because it's really important, but you can't read it. Does that get tagged as Scott MacKenzie? So when somebody says, hey, that I see it, it's got a little red check mark must be important, but I can't read it. Let me go talk to Scott.
12:39
Oh absolutely, yeah, when you're putting in red lines, especially in the field, it's a red line by a person at a date and time over a certain revision, because the other side of it is, that now really becomes document history that we want to maintain and our customers may need to maintain for a variety of different reasons. Some of it could be as simple as, or as complex as a legal hold situation where yes, we knew that was a problem, we noted it, we handed that document to a certain technology provider, and what was promised didn't happen. And here's our proof that we did everything as we were supposed to.
But yeah, keeping those records, keeping that audit trail of being able to tell the history and the story of these critical and, frankly, expensive documents is is a key part of the Meridian capability and, and a key part of what every organization should be after with these files. You know, it's just absolutely critical.
13:29
Can I also attach those files to the assets? So, here's a pump. Yes, this pump has had some revisions on the documents. So I'm out in the field, I'm on a mobile solution, and I'm popping it up. And I'm going, “Alright, okay, good. I got the latest and greatest. Great.” And I have a high level of confidence that that's so I can attach it to that asset?
13:53
Oh yeah, absolutely. That's one of the key things that sets Meridian apart from a lot of the other solutions. But there are a lot of ones that do that. And I had a talk yesterday where we were highlighting that probably one of the single most valuable things that you can do with these critical engineering documents, apart from ensuring that they're accurate, is to have that relationship to those assets that they cover that they're important to, and that they can jump to those points there. Because at that point in time, you've created a whole other layer of ergonomics over the top of this data, so that that team that the only thing they speak is asset ID, can find all of the information that they need across multiple disciplines, knowing one piece of data. That's that's the key thing that everyone should be going after, as far as I'm concerned, if you really have a reliability and an operations focus, you know, be that data and assets, be it a PI tag or whatever that you know, PLC, whatever that piece of information is.
14:45
That complete picture on that asset or wherever you're working at. There's no you know, some piece of information that's sort of rogue out there that might have been necessary for your work. So you want to make sure that everything is encapsulated on whatever that that wherever you're at. I got it all, and it’s a high level of trust.
15:10
Well, in my background is, before I came into the software side, I was actually a customer Meridian working in the chemicals, oil and gas industry for major Refining Company. I installed and supported this software for 400,000 barrels per day refinery. And those guys and gals working in that facility, many of them just spoke, oh, I need this document number and this document number and that document number. And that was great for that time until we had a major refit of that unit after a turnaround. And now, the PNID previously instead of maybe being updated because it was consolidated and retired. And now that knowledge that they had that internal decoder ring that they were running a facility on is broken. And so now it's a relearning, now it's stepping back through, “Okay, what are you really trying to do? How are you doing that? What's the key information that you're bringing to that, that exchange and ensuring that we've got a system that is able to do that?”
16:05
See, and if you ever look at a refinery, it just looks like it's a collection of pipes, and more pipes and I always had this conversation with somebody because I had, “Look at that rusty old pipe that's still on that rack? She said still being used? How do you know that that's being used? How do you know? How do you know what's going on? Why is that critical? Right? Rusty pipe on that rack? That's probably been there since you know, the ‘50s.”
16:41
Yeah, that's that's a and that's another strength, a bit of Meridian as well as because it's going to manage through those changes. But we have a concept that we brought to the market called concurrent engineering where a document can be checked out to multiple projects and changed independently across those different elements. And a lot of software solutions do that.
The there's ones that say, oh, no, why would you ever want to do that? And the answer is, multiple people are changing these documents. And you can either give them a platform that's going to enable them to make those changes, or they're going to work outside of your platform. Because what happens is, you hire intelligent people, do it on purpose, and then you give them a tough job to do. And if you don't give them the right tool to do it, they're going to work around you or invent their own tool that may not conform to your vision of how they should be doing work. But the reality is, I have key documentation that needs to be changed by multiple people at a given time. Wouldn't it be nice if I had a system that allowed those threads to happen? But then put checks in place and had tools to let me overlay those two documents and see where did they actually change? You know, things along the journey?
17:47
Because it's a journey, it has to be. You have to have the mindset that this is important. It's important to the operations. It's going down that road anyway, whether I like it or not, yeah, we got to do it. So let's do it. But don't expect it to be this big bang. And like, yesterday, we were in the file cabinets and today it's all digital, and I just I like I can appreciate that passion. But it doesn't work that way.
18:16
No, you're right. And it takes it's a process. There's, you know, organizational change management is its own discipline for a very good reason. And having gone through that change management and pushing it forward, you know, the on a monthly basis. It's like monetization on monthly, it's daily sometimes. Yeah, you know, and sometimes, you know, people are hesitant to do a lot of that, because then you become the face of the change. And if it's unpopular with somebody, what happens with that?
18:45
No, but if you passionately believe about things, and you know, you're going to improve it, even the you know, you they may be, you know, a resident in Missouri, and they're gonna hit a Show Me State moment with you. But if you show them that it's going to improve. I think people get along with you really well.
19:03
You're wonderful. How do they get a hold of you?
19:07
Reach out to us through accruent.com. Let's talk about Meridian. There's a demo button right there. Schedule a demo. Let's take some time, take an hour and see if there's work here for us if there's improvements to make.
19:20
All right, his name is Jason. Accruent is a company we are broadcasting from Accruent Insights user community that is destined to solve problems. I'm trying to find out more words to be able to say because it's pretty cool. They're they're collaborating behind you act if there's a big time active. Alright, we're gonna have all the contact information for Jason out on an industrial talk. So if you're not reach out, you will not be disappointed. We will be right back.
19:46
You're listening to the Industrial Talk Podcast Network.
19:56
All right. His name is Jason Kraus. He is a solution consultant with Accruent, and as you can tell, document management was the center of the conversation. And boy, do we need document management. I mean that grabbing that tiger by the tail is a real challenge. So, glad that there's a product called Meridian out there that allows for at least managing those documents. Three days, the world is just wide open when it comes to all these. There's just, there's just ton of stuff happening out there. All right, once again, Industrial Talk platform is for you industrial content creators. Go out to industrial talk, say hey, collaborate. There's a big old button right there. Want to collaborate, and then you'll get the stick. We're looking for podcasts. We're looking for videos, we're looking for blogs to be featured on the industrial talk.com location. So be bold, be brave, dare greatly. Contact Jason. Change the world. We're gonna have another great conversation coming from this conference shortly.
You might also like
Here from Meelad Nikpourian and Eric Cook about the power of collaboration to solve cross-industry pain points.
Hear from Accruent CIO Marvin Clark about the changing landscape of asset management, the role that emerging technologies will play, and how the ...
Hear from the Jacobs Engineering team about document management best practices, how to maintain clean foundational data, and what trends to look out ...
Subscribe to stay up to date with our latest news, resources and best practices