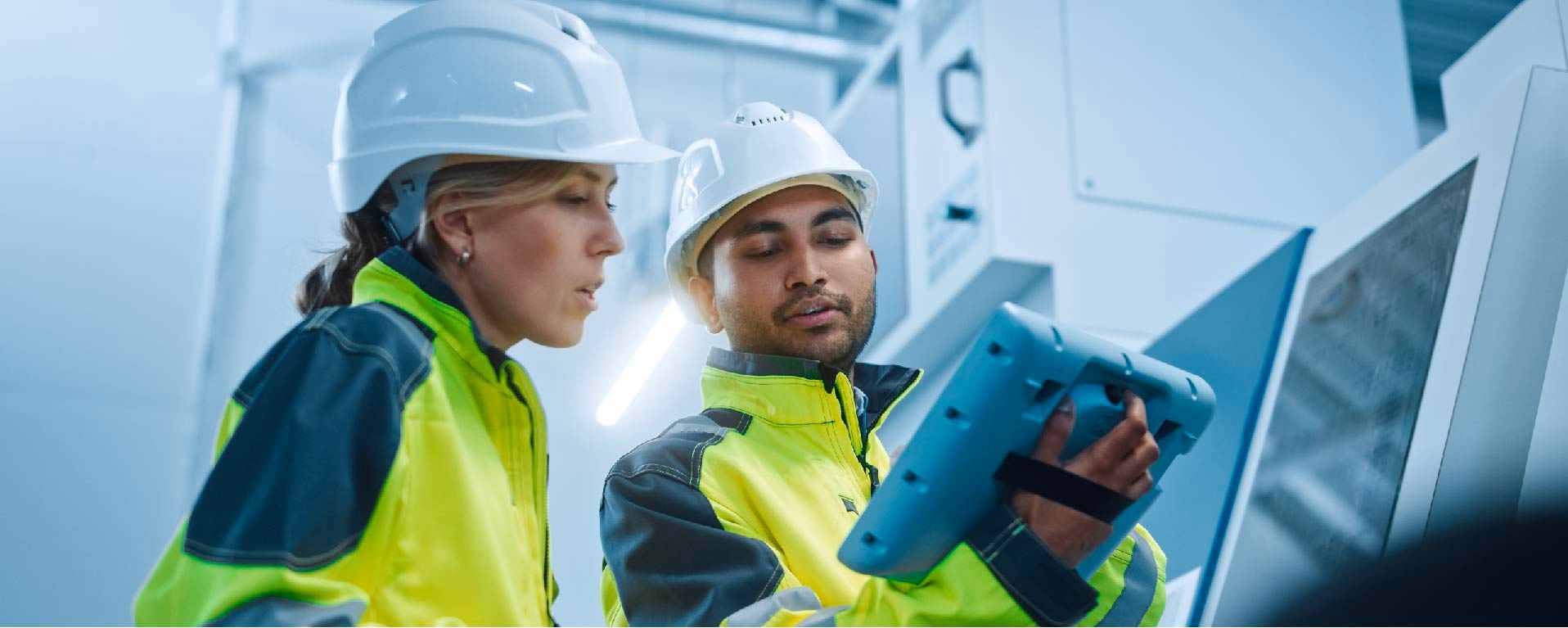
How Maintenance Managers Extend Asset Life and Decrease Downtime with CMMS
The right CMMS can help your organization minimize downtime and extend asset life. Here's how.
Solutions
Workplace Management Solutions
Real Estate Management Solutions
Maintenance Management Solutions
Energy Management Solutions
Engineering Document Management Solutions
Asset Management Solutions
Automate campus scheduling for classes, meetings, and exams with our EMS software.
Plan and manage conferences effortlessly with EMS software to impress guests and streamline operations.
Boost workplace flexibility and maximize space use with seamless desk and room booking.
Organize workplace or campus events smoothly, creating memorable experiences.
Optimize workspace, manage allocations efficiently, and reduce costs with our space management solutions.
Deliver projects on time and within budget by improving communication, collaboration, and efficiency with our software.
Streamline lease accounting for ASC 842, IFRS, and GASB compliance.
Manage leases efficiently by tracking key dates, analyzing costs, and ensuring compliance.
Centralize data and analytics for better insights, faster negotiations, and revenue growth.
Centralize facility and asset maintenance, automate work orders, and ensure compliance with our CMMS software.
Extend asset life, reduce downtime, and prevent costly repairs with data-driven monitoring.
Prevent equipment failures and extend asset life by detecting and addressing issues early.
Make sustainable, cost-efficient energy decisions by monitoring and optimizing power consumption.
Remotely monitor and control equipment with real-time data to predict issues, boost efficiency, and reduce downtime.
Easily share and collaborate on documents, creating a single source of truth for engineers and contractors.
Manage and analyze assets across their lifecycle to schedule maintenance, reduce downtime, and extend lifespan.
Improve visibility, automate work orders, and ensure compliance for efficient facility and asset management.
Resources
Browse our full library of resources all in one place, including webinars, whitepapers, podcast episodes, and more.
Support
Looking for access to technical support, best practices, helpful videos, or training tools? You’ve come to the right place.
About Accruent
Get the latest information on Accruent, our solutions, events, and the company at large.
Want to know exactly how a CMMS implementation will impact your ROI? Here's how to make the calculations.
For any company, the most important question when implementing something new is, “Will this increase my ROI? If so, how?” After all, lowering costs and increasing profit margins is ultimately the bottom line, and if something is not going to make your company money, it is simply not worth it to decision-makers and C-level executives.
That is certainly true of any new technology that is adopted. And there seems to be a constant tug-of-war in the modern workplace between trying something new, better – and potentially costly — and sticking with the legacy systems you already know.
Oftentimes, the legacy system wins: with many new tools, the price tag can seem prohibitive and the risk high, particularly when things like ease-of-use, integrability with your current systems, and ROI are unclear.
This should not be the case with a computerized maintenance management system (CMMS). When implemented correctly, a robust CMMS can ultimately increase ROI and simplify operations by eliminating major inefficiencies like unscheduled downtime, a high time-to-repair, and low transparency into asset maintenance activity.
Do not just take our word for it. Here is how to definitively calculate the ROI of your CMMS:
There is a simple formula for calculating CMMS ROI: (CMMS value – CMMS cost) / CMMS cost
To effectively calculate these values, you need to know three things:
When plugging in the numbers for this formula, finding the CMMS cost can be fairly straightforward. Determining CMMS value, on the other hand, can be slightly more difficult to find.
If you do not have the bandwidth to fully calculate ROI, you can get a decent estimate by referring to studies on preventive maintenance (PM). A robust, full-featured CMMS will automate and streamline PM efforts, so looking at the benefits of strong preventive maintenance practices can give you some idea of CMMS ROI. Here are some preliminary numbers to reference:
An effective CMMS can save you money directly or indirectly by saving time or improving outputs. There are six key areas of your maintenance operations that you can look at to get a holistic understanding of your CMMS ROI:
Reactive maintenance can, among other things, reduce safety, increase unplanned downtime and reduce asset lifestyle. Unfortunately, it remains common practice in companies without a CMMS, as these companies usually have important asset data recorded on paper or in outdated, disparate legacy systems that make it difficult to track asset histories, schedule PMs or execute preventive maintenance.
Solving this issue with a CMMS — and thereby increasing asset lifecycle — can decrease both labor costs and the cost of unexpected breakdowns.
To determine annual savings due to increased asset lifecycle, divide the total cost of an asset by the lifespan.
For example, if an asset costs $75,000 and it is used for ten years, the cost per year is $7,500. Extending that asset’s life by six months would create a savings of $3,750.
A centralized, collaborative, real-time CMMS system can help users:
Ultimately, this can reduce downtime, particularly unplanned downtime.
Of course, the real cost of unplanned downtime can be difficult to calculate, as it can impact many other aspects of your business, including labor costs, productivity and asset lifespan, so start by looking at a single asset to get an estimate.
For example, say one of your assets was disabled. The repair parts cost $4,000 and the unforeseen labor to fix it cost $1,000. You are fairly certain the issue could have been avoided with a CMMS, and this kind of breakdown happens twice a year.
In this instance, your estimated annual savings would be approximately $10,000.
A CMMS can help you automate inventory management with features like stock level notifications, item lookup and automatic part usage tracking. This can reduce things like carrying cost of obsolete items and the cost of emergency orders if you do not have something on hand.
To calculate parts and inventory savings, you must know:
For example, say that you have $3,000 worth of useless inventory in a month and you have to spend $2,000 ordering emergency parts. You are confident that a CMMS would give you the insight you need to reduce such situations. Your monthly savings could be $5,000 a month, or $60,000 a year.
CMMS solutions often give both technicians and administrators more structure, easy access to important asset information, and uninterrupted, accurate communication. This can increase productivity and reduce labor costs over time. To effectively calculate productivity gains, you must know:
For example:
The calculation, then, would be 45 * 10 * 1 * 66 = $29,700 in savings per quarter.
In the same vein, you can lower annual utility costs. HVAC systems are generally responsible for more than 40% of total energy use in a commercial building. Scheduled preventive maintenance can allow your HVAC systems to operate at maximum efficiency, which can use 15% to 20% fewer resources like gas, electricity and water.
To then calculate savings, find the total amount your organization spends on utilities and compare that number to the expected cost if assets like HVAC units were operating at peak efficiency. For many businesses, this can translate to thousands of dollars in savings.
Companies in many industries are frequently audited by the government or by regulatory agencies, and those who cannot provide the right documentation or maintain compliance can face heavy fines.
A CMMS will provide preventive maintenance checklists, schedules and historical maintenance records at a glance, and having access to this information can help companies like yours maintain compliance and pass these audits.
Now that you have some understanding of internal factors to calculate, you must also look at the cost of a CMMS. When calculating CMMS cost, you must take into account:
This information is generally available on your CMMS provider’s website. Many providers charge per user, so you will have to multiply price per user by the number of users to get the full cost.
CMMS implementations can be complex, and they can cost both time and money. Most companies have thousands of assets that they need help importing, and CMMS providers are usually happy to do so for a fee. These costs must be calculated.
There is also money that goes into training and onboarding your technicians and relevant team members until they are comfortable with the software. This is an absolutely essential part of effective CMMS implementation – if your employees do not use the tool properly, it can ultimately cost you money rather than save.
To calculate the cost of onboarding, you must consider how many hours it will take to onboard, hourly salary, and the number of personnel that you need to onboard.
Do you need new devices – like tablets or smartphones – to make full use of the mobile functionality of a CMMS? If so, this must also be taken into account.
Ultimately, a powerful CMMS will always yield a positive ROI if it is implemented correctly and if your team is properly onboarded. Using the calculations above, you can prove this for yourself.
A robust CMMS system can provide your business with a single source of truth for all information that your facility and maintenance management teams need. It can also help companies like yours plan, track, measure, and optimize everything to do with preventive maintenance and work order management so you can develop better maintenance practices, stay organized, and ultimately save time and money.
Want to see how a CMMS can save money for your business? Try our Savings Calculator.
Plan your investment with our CMMS pricing guide.
The right CMMS can help your organization minimize downtime and extend asset life. Here's how.
Learn how a successful CMMS implementation can help you overcome reactive maintenance inefficiencies and maximize your overall return on investment ...
Learn how Maintenance Connection helped The New York Times automate reports, allocate resources, and improve labor productivity.
Subscribe to stay up to date with our latest news, resources and best practices