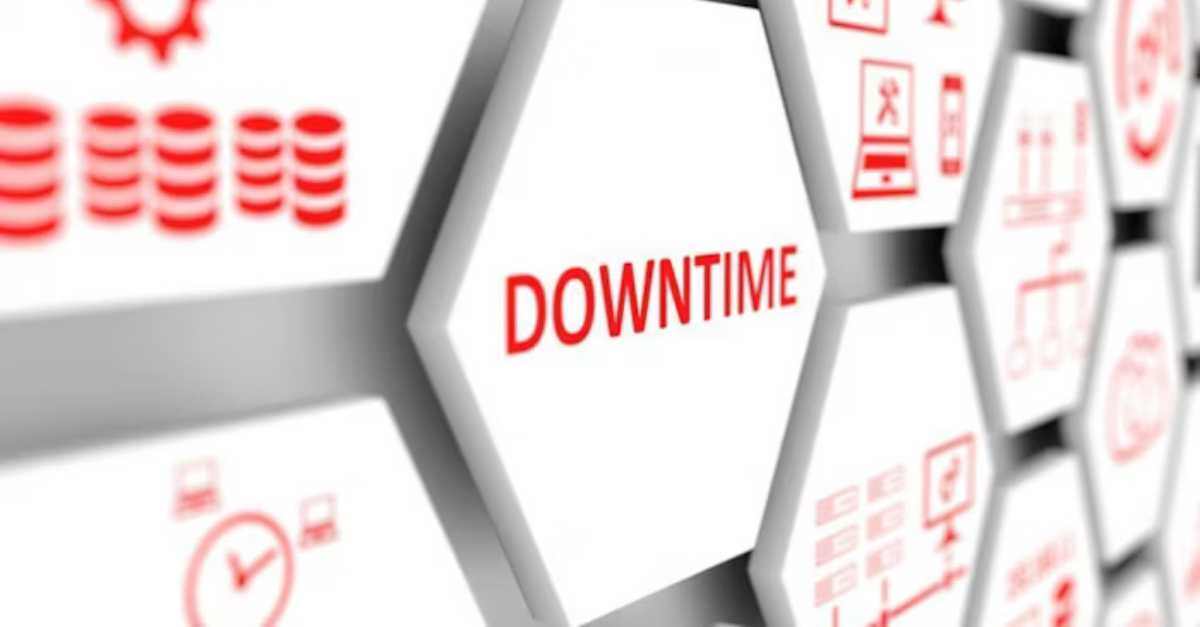
Reducing the Cost of Unplanned Downtime in Utilities
The rising cost of downtime in utilities just keeps growing. Leverage an engineering document management solution to turn the tide on this ...
Solutions
Workplace Management Solutions
Real Estate Management Solutions
Maintenance Management Solutions
Energy Management Solutions
Engineering Document Management Solutions
Asset Management Solutions
Automate campus scheduling for classes, meetings, and exams with our EMS software.
Plan and manage conferences effortlessly with EMS software to impress guests and streamline operations.
Boost workplace flexibility and maximize space use with seamless desk and room booking.
Organize workplace or campus events smoothly, creating memorable experiences.
Optimize workspace, manage allocations efficiently, and reduce costs with our space management solutions.
Deliver projects on time and within budget by improving communication, collaboration, and efficiency with our software.
Streamline lease accounting for ASC 842, IFRS, and GASB compliance.
Manage leases efficiently by tracking key dates, analyzing costs, and ensuring compliance.
Centralize data and analytics for better insights, faster negotiations, and revenue growth.
Centralize facility and asset maintenance, automate work orders, and ensure compliance with our CMMS software.
Extend asset life, reduce downtime, and prevent costly repairs with data-driven monitoring.
Prevent equipment failures and extend asset life by detecting and addressing issues early.
Make sustainable, cost-efficient energy decisions by monitoring and optimizing power consumption.
Remotely monitor and control equipment with real-time data to predict issues, boost efficiency, and reduce downtime.
Easily share and collaborate on documents, creating a single source of truth for engineers and contractors.
Manage and analyze assets across their lifecycle to schedule maintenance, reduce downtime, and extend lifespan.
Improve visibility, automate work orders, and ensure compliance for efficient facility and asset management.
Resources
Browse our full library of resources all in one place, including webinars, whitepapers, podcast episodes, and more.
Support
Looking for access to technical support, best practices, helpful videos, or training tools? You’ve come to the right place.
About Accruent
Get the latest information on Accruent, our solutions, events, and the company at large.
Learn how to create a seamless document handover process to avoid expensive project delays, rework, and even industrial accidents.
Table of contents
In our previous blog, Where do Project Managers Fit in Asset Lifecycle Information Management?, we discuss how in asset lifecycle information management, the number of changes and documents to track is extensive. We’re digging further into the challenges that arise from the handover process between engineering firms and owner-operators.
At the root of this problem is that larger, multi-national engineering, procurement, and construction firms are the ones who determine how information is provided, and smaller firms do not have the resources or expertise to provide the data in that manner. This disparity leaves the owner-operator with the ongoing challenge of getting the information about their newly commissioned facility into some sort of order, so they can operate in a safe, compliant, and efficient manner.
On average, an owner-operator unexpectedly spends 2-4% of the project cost to correct and reproduce missing operations and maintenance information manually, according to Ken Bever's "Problems with Information Handover". Even slightly reducing that percentage would represent a significant reduction of this unaccounted-for cost. If the correct operations and maintenance information is provided from the beginning, the safety of operations, which is an absolute priority for all asset-heavy companies is considered an additional benefit.
Owner-operators need to clearly define what they want from their suppliers in terms of data. For example, expectations about formatting data or classifying information should be clear from the beginning.
The handover process is never easy and can be costly. When expectations about specific formatting and classifications are involved, contractors justify an additional (large) fee to these meet demands because it’s considered “custom.” If these contractors have standards that work for most customers, it makes sense to charge more to do “extra work.” This approach causes most purchasing departments to settle for lower expectations in order to bring down the costs. Therefore, the cycle of pain continues.
Solving the expectations problem means all parties working together towards a strategy that benefits not just the long-suffering operations and maintenance department. If everyone involved (owner-operators, contractors, engineers, etc.) agrees on a common standard to use when defining and exchanging asset information, then everyone involved can see the benefits.
Adding contextual information about the data is a great starting point. By providing context, the receiver is aligned to understand what they have been given and does not need to waste time rebuilding what has already been stated. If the contextual information is standardized across industries, then stakeholders can build systems and processes that reduce risks and costs through improvements to data quality, automation and repeatable use of the systems and methods. For example, the Capital Facilities Information Handover Standard (CFIHOS) is an organization within the oil and gas industry dedicated to providing common solutions for asset information.
For over 30 years, Accruent has supported the process manufacturing industry by standardizing and improving the asset information handling process. Using accurate, interoperable data, our software solution, Meridian Portal, provides opportunities for our customers to transform project delivery.
The adoption of industry standards throughout the supply chain can benefit everyone. The handover of information does not have to be a costly or painful process, and with the right solution and expectations laid out – can be overcome.
Find out more about how Accruent can help project managers with Asset Lifecycle Information Management or schedule a demo today!
The rising cost of downtime in utilities just keeps growing. Leverage an engineering document management solution to turn the tide on this ...
Discover how transitioning from 2D to 3D can revolutionize how your business operates. Learn the top six benefits that can be realized from embracing ...
Explore how centralized data, resource allocation and process improvements can positively impact profitability in your organization.
Subscribe to stay up to date with our latest news, resources and best practices