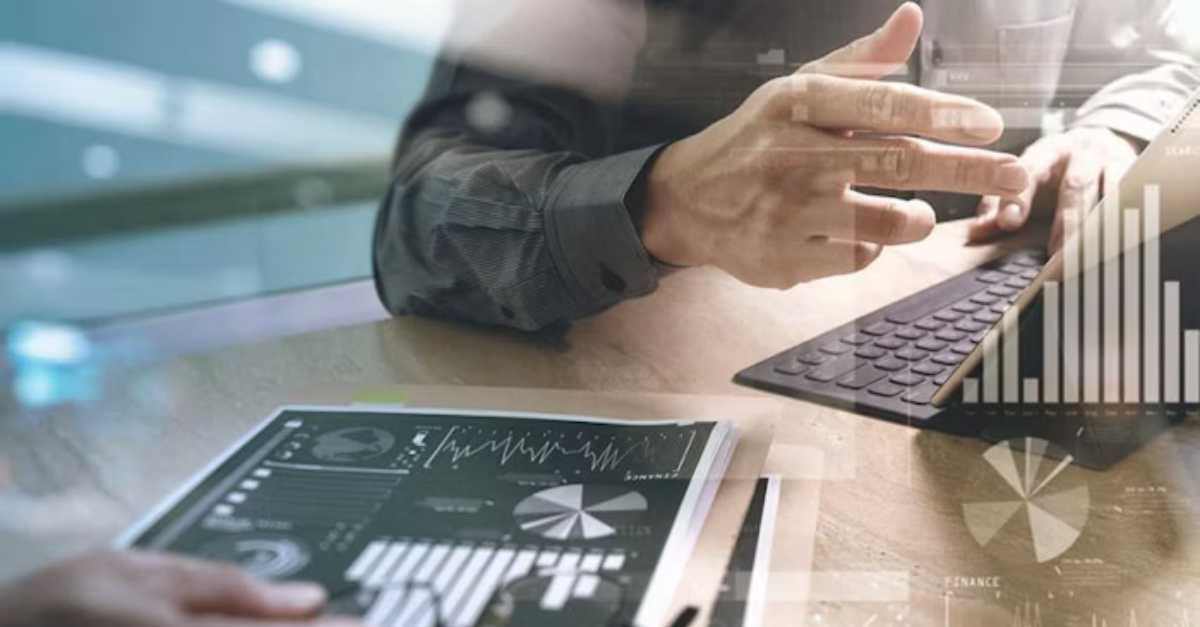
Capital Plans to Innovate & Drive the Customer Experience
Learn how to build a capital plan that addresses your facility's most urgent needs by allowing Accruent’s CMMS and capital planning solutions to ...
Solutions
Workplace Management Solutions
Real Estate Management Solutions
Maintenance Management Solutions
Energy Management Solutions
Engineering Document Management Solutions
Asset Management Solutions
Automate campus scheduling for classes, meetings, and exams with our EMS software.
Plan and manage conferences effortlessly with EMS software to impress guests and streamline operations.
Boost workplace flexibility and maximize space use with seamless desk and room booking.
Organize workplace or campus events smoothly, creating memorable experiences.
Optimize workspace, manage allocations efficiently, and reduce costs with our space management solutions.
Deliver projects on time and within budget by improving communication, collaboration, and efficiency with our software.
Streamline lease accounting for ASC 842, IFRS, and GASB compliance.
Manage leases efficiently by tracking key dates, analyzing costs, and ensuring compliance.
Centralize data and analytics for better insights, faster negotiations, and revenue growth.
Centralize facility and asset maintenance, automate work orders, and ensure compliance with our CMMS software.
Extend asset life, reduce downtime, and prevent costly repairs with data-driven monitoring.
Prevent equipment failures and extend asset life by detecting and addressing issues early.
Make sustainable, cost-efficient energy decisions by monitoring and optimizing power consumption.
Remotely monitor and control equipment with real-time data to predict issues, boost efficiency, and reduce downtime.
Easily share and collaborate on documents, creating a single source of truth for engineers and contractors.
Manage and analyze assets across their lifecycle to schedule maintenance, reduce downtime, and extend lifespan.
Improve visibility, automate work orders, and ensure compliance for efficient facility and asset management.
Resources
Browse our full library of resources all in one place, including webinars, whitepapers, podcast episodes, and more.
Support
Looking for access to technical support, best practices, helpful videos, or training tools? You’ve come to the right place.
About Accruent
Get the latest information on Accruent, our solutions, events, and the company at large.
Discover how Accruent solutions can help your facilities management teams solve their most pressing recurring pain points.
Whether it's resolving maintenance issues or completing large-scale projects on time and on budget, facilities management initiatives are critical to the customer experience. But facilities management teams and budgets are increasingly stretched thin trying to perform the same enterprise-wide initiatives with fewer people and funds.
Accruent is partnering with some of our largest facilities management customers to develop innovative solutions that will save maintenance teams time and money. Here are two of the biggest challenges facilities management teams are facing and how organizations can solve them with new product features from Accruent.
There are many factors that go into prioritizing work orders, including how the issue will affect the customer experience, cost, potential lost revenue, and reputation. But this information is not typically housed in standard asset management software. With most software, priority is determined by one of two factors: the priority assigned by the user who created the work order, or a static calculation based on the work order category and problem type.
The issue, of course, is that the store or office managers might not have the big-picture view that allows them to prioritize appropriately. Low-priority work orders are then treated as emergencies and high-impact work orders languish under a prioritization and SLA that does not reflect the urgency it requires.
Before Dynamic Work Order Prioritization, the only mechanisms to prioritize work orders were either too rigid or too flexible. Retailers know that there is a wealth of information that could go into the priority of a work order; the information just was not available in most CMMS or asset management solutions.
For instance, a work order at a flagship store should take higher priority than the same type of work order at a store with a fraction of the revenue and foot traffic. To help clients make the most of limited budgets, Accruent developed a new prioritization feature in our facilities management solution. Users can now take advantage of a simple business rule builder that uses existing product and user-defined fields to prioritize work orders effectively and objectively.
For example, a customer can create a site attribute for store revenue, which can be used to prioritize a work order. This means customers can prioritize work orders based on impact and severity to consistently ensure their dollars are going toward work that impacts their bottom line.
To learn more about what your organization can do to prioritize work orders, check out our facilities management solution.
Frequently, when a service provider goes on-site to fix a problem, it is difficult to find where the problem is, or they need to get directions from a store or site manager to find the broken item. Since the work order was generated from data at the controller level, the store/site manager usually needs to hunt down the broken item. This wastes time that could be better spent on other issues and causes service providers to bill for additional time on-site.
Accruent has developed a new site layout feature in its IoT remote monitoring platform, that relies on a site or store map to visually show maintenance teams where the problem lies. With the new site layout functionality, we’ve eliminated the need for service providers and maintenance teams to interrupt store managers or waste time searching for broken items. Instead they follow the map in the work order directly to the location of the problem.
Site layout can also be used to empower store managers to investigate issues on-site before calling in a work order by showing them where to find the problem and providing them with troubleshooting steps. This cuts back on the use of third-party service providers and saves on maintenance costs.
Learn more about site layout and other features we have within our IoT Remote Monitoring platform.
Accruent is continuously innovating to better serve our customers and help them achieve next level savings and efficiencies in their processes. Work order prioritization and site layout will help organizations eliminate unnecessary expenditures, lower technician time-on-site, reduce staff disruptions and contribute to better-allocated resources.
To learn more about Maintenance Connection and Observe, request a demo!
Learn how to build a capital plan that addresses your facility's most urgent needs by allowing Accruent’s CMMS and capital planning solutions to ...
Discover three ways Accruent’s FAMIS 360 facilities asset management solution can help you react, plan and prepare for a safe and clean future at ...
Accruent offers its third of seven tips to helping facilities management (FM) teams save time, costs and energy to become a strategic contributor.
Subscribe to stay up to date with our latest news, resources and best practices