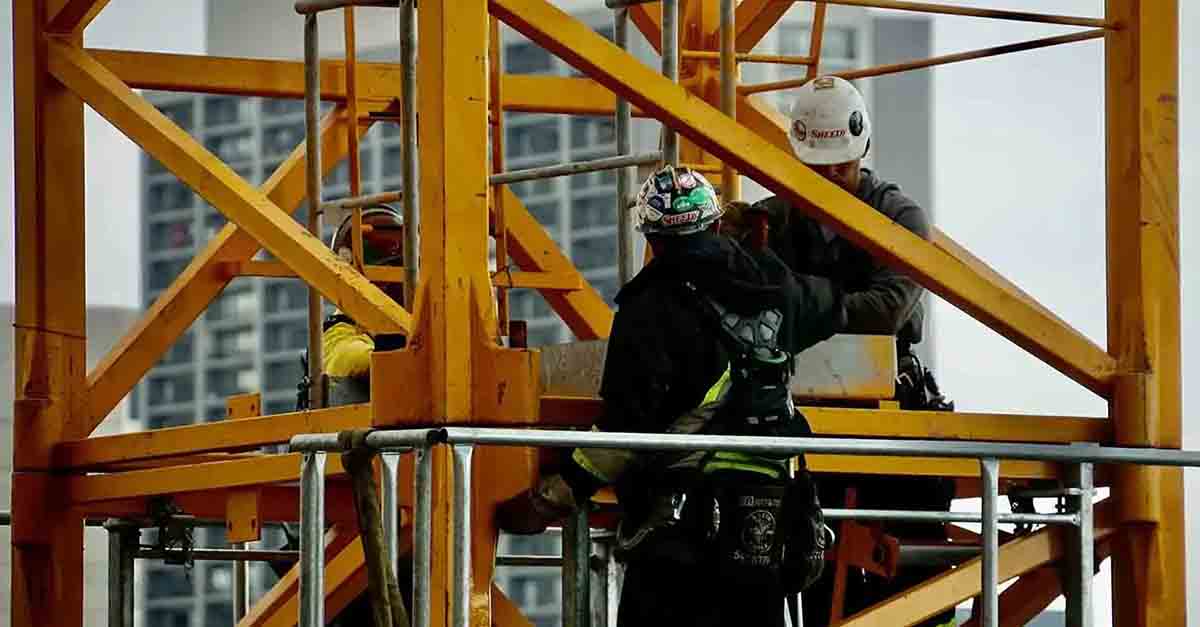
How To Develop A Preventive Maintenance Program
Learn how to develop a robust preventive maintenance program. Explore step-by-step guidelines and expert tips to streamline maintenance operations.
Solutions
Workplace Management Solutions
Real Estate Management Solutions
Maintenance Management Solutions
Energy Management Solutions
Engineering Document Management Solutions
Asset Management Solutions
Automate campus scheduling for classes, meetings, and exams with our EMS software.
Plan and manage conferences effortlessly with EMS software to impress guests and streamline operations.
Boost workplace flexibility and maximize space use with seamless desk and room booking.
Organize workplace or campus events smoothly, creating memorable experiences.
Optimize workspace, manage allocations efficiently, and reduce costs with our space management solutions.
Deliver projects on time and within budget by improving communication, collaboration, and efficiency with our software.
Streamline lease accounting for ASC 842, IFRS, and GASB compliance.
Manage leases efficiently by tracking key dates, analyzing costs, and ensuring compliance.
Centralize data and analytics for better insights, faster negotiations, and revenue growth.
Centralize facility and asset maintenance, automate work orders, and ensure compliance with our CMMS software.
Extend asset life, reduce downtime, and prevent costly repairs with data-driven monitoring.
Prevent equipment failures and extend asset life by detecting and addressing issues early.
Make sustainable, cost-efficient energy decisions by monitoring and optimizing power consumption.
Remotely monitor and control equipment with real-time data to predict issues, boost efficiency, and reduce downtime.
Easily share and collaborate on documents, creating a single source of truth for engineers and contractors.
Manage and analyze assets across their lifecycle to schedule maintenance, reduce downtime, and extend lifespan.
Improve visibility, automate work orders, and ensure compliance for efficient facility and asset management.
Resources
Browse our full library of resources all in one place, including webinars, whitepapers, podcast episodes, and more.
Support
Looking for access to technical support, best practices, helpful videos, or training tools? You’ve come to the right place.
About Accruent
Get the latest information on Accruent, our solutions, events, and the company at large.
Discover the essential strategies for achieving maintenance management excellence in the manufacturing industry. Learn how to leverage maintenance management software to optimize operations and drive cost efficiency.
Table of contents
Imagine an automotive manufacturing plant where a key piece of assembly line machinery suddenly halts production. Is there a maintenance management plan in place? If not, there is a massive risk of significant loss of resources.
This scenario illustrates the importance of maintenance management. The right program can diagnose the issue while implementing strategies to prevent it from happening again. The goal is to minimize downtime while safeguarding the production schedule.
Now, in the modern production world, advanced maintenance management software offers organizations ways to automate and tap new levels of production and efficiency.
Maintenance management is a strategic approach within the manufacturing sector focused on the upkeep and optimal functioning of equipment and facilities. At its core, it integrates planning, tracking, and execution of maintenance activities to prevent downtime and extend the lifespan of manufacturing assets.
Key components include scheduled preventative maintenance, timely repairs, and efficient resource allocation – all aimed at enhancing operational efficiency. Reducing equipment failures and optimizing maintenance schedules significantly reduces costs. This uninterrupted production process means maintenance management is a particularly important variable in achieving excellence.
Don’t wait for a crisis to reduce costs."— Harvard Business Review
To ensure the durability, efficiency, and longevity of equipment, organizations must establish an effective maintenance management program. Not sure where to begin? Here are seven strategies to refine maintenance operations. The goal here is to curb downtime while improving overall performance.
This proactive strategy schedules regular upkeep to avert equipment failures. Doing so prevents breakdowns while extending the life of an asset. It is a simple, straightforward way to enhance longevity and reliability. Think of it as the bedrock of overall effective maintenance management. Scheduled maintenance can significantly reduce the likelihood of unexpected equipment downtime.
Why not prevent disaster before it happens? Leveraging advanced analytics and machine learning, this method forecasts potential equipment malfunctions before they occur. This allows for precision in maintenance planning. Predictive maintenance minimizes unexpected breakdowns to help maintain continuous production flow.
Conditions drive decisions – and data is empowering. By continuously monitoring equipment in real-time, different maintenance actions are triggered by the actual state of the machinery. This avoids any unnecessary resource waste due to a preset schedule. The condition-based approach is specific and targeted. It ensures maintenance is as effective as possible.
Prioritize what needs to be done and when. Utilizing RCM means basing maintenance decisions on the needs of an organization. This approach tailors specific strategies and decisions based on the unique demands and risks of each piece of equipment. The methodology helps organizations focus their efforts on where they will have the most significant impact. In addition, it encourages cost-effective decision-making.
TPM utilizes and engages the entire workforce in maintenance activities – from the shop floor to management. The goal here is to foster a shared responsibility for equipment care through active involvement and preventative maintenance from all different parties. In theory, the “all in this together” mentality can lead to a culture of continuous improvement where every employee plays a significant role. Ensuring everyone wears proper protective headgear is one example of how shared safety responsibility is put into action. It can improve overall operational efficiency and workplace safety.
When failures occur, use an RCA to dig deep to uncover the underlying causes rather than addressing the symptoms. By identifying and rectifying these root causes, future failures can be prevented. It is about using hiccups as a catalyst for innovation and solidifying the overall reliability of manufacturing operations.
Modern technology transforms maintenance management. CMMS is sophisticated software that centralizes maintenance data, automates maintenance scheduling, and tracks performance metrics. This advanced technology solution enables better resource allocation, detailed reporting, and improved decision-making. It is about simplifying and streamlining maintenance management, transforming it into a competitive advantage.
Download the Free Maintenance KPIs Guide to track performance, improve operations, and keep your maintenance strategy on point.
Maintenance management software – particularly Computerized Maintenance Management Systems (CMMS) – offers organizations a simple, straightforward way to get proactive with their manufacturing operations. Advanced technology transforms the traditional approach to maintenance by digitizing processes and centralizing data. The integration of tech into maintenance routines offers several benefits.
For instance, CMMS software provides much-needed transparency. The real-time insights into maintenance activities, equipment status, and performance metrics provide data for informed decision-making. Further, work order software can automate scheduling and tracking which reduces manual effort while minimizing the potential for human error.
Moreover, preventative, and predictive maintenance strategies are ingrained into the DNA of a CMMS. The ability to analyze historical data and current operational parameters means the system can forecast potential equipment failures. That means an extension of the equipment’s lifespan while optimizing maintenance costs.
It is about improved efficiency, enhanced asset reliability, and significant cost savings. The right CMMS is a strategic investment in the future of manufacturing.
Long-term benefits of implementing automation include increased profitability, accountability, productivity, and flexibility."— Forbes Business Council
Accruent Maintenance Connection is an industry-leading CMMS. The goal of the software is to revolutionize the way organizations handle their maintenance operations. As a comprehensive platform, Maintenance Connection offers a suite of tools designed to improve every aspect of maintenance management.
Key features include the following:
Implementing Accruent Maintenance Connection can significantly streamline maintenance operations for organizations. Organizations can customize the software to their specific workflows and integrate it with other enterprise systems.
The preventative maintenance software automates scheduling and work order management removing time suck on staff. Its comprehensive compliance support and advanced asset lifecycle management ensure an overall optimization of an organization’s asset portfolio.
Accruent Maintenance Connection aims to be more than just another CMMS. Instead, it is designed to meet the challenges of tomorrow – today. It is building towards a smarter, more efficient maintenance management system of the future.
Advanced technology like Accruent Maintenance Connection is a major step towards operational excellence within the maintenance management space. This CMMS solution is designed to enhance and streamline strategies, operations, and more.
Want to know how? Request a demo or contact the Accruent sales team for more information on building towards a future that is data-driven, efficient, and empowering.
Maintenance management can be broadly categorized into several types, including preventive, predictive, and condition-based maintenance. Preventive maintenance is scheduled regularly, predictive maintenance relies on data to forecast needs, and condition-based maintenance is based on equipment needs.
There are multiple core functions of maintenance management. They include scheduling regular maintenance, managing repairs, ensuring equipment reliability, optimizing maintenance tasks, and improving overall operational efficiency. What these functions aim to do is minimize downtime while extending the lifespan of assets.
In operations management, maintenance refers to the practices and processes utilized to keep equipment running efficiently and safely. What this means in practice is routine inspections, repairs, replacements, and upgrades that prevent equipment failure. The goal is the smooth operation of manufacturing processes.
Total maintenance management (TMM) is a comprehensive approach that uses all aspects of maintenance management to improve equipment reliability and operational performance. TMM uses proactive maintenance strategies, employee involvement, and continuous improvement practices to achieve optimal asset performance and overall efficiency.
Learn how to develop a robust preventive maintenance program. Explore step-by-step guidelines and expert tips to streamline maintenance operations.
A CMMS or computerized maintenance management system is software that helps plan, monitor, & report maintenance tasks, track work orders & ...
Learn how to calculate and track maintenance KPIs effectively. Understand key metrics to improve maintenance performance and operational efficiency.
Subscribe to stay up to date with our latest news, resources and best practices