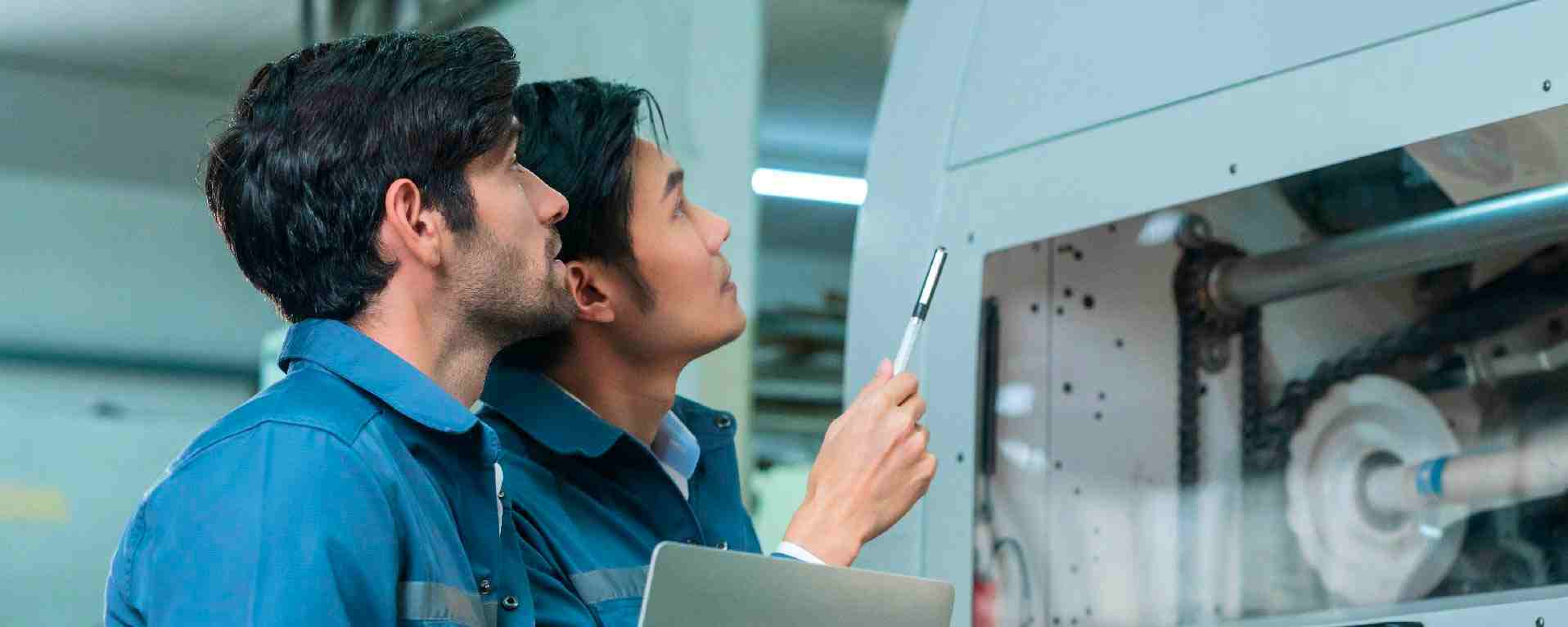
How to Calculate Equipment Downtime
Getting a handle on your equipment downtime can help your reduce costs, maximize efficiency and optimize operations. Here's how to calculate your ...
Solutions
Workplace Management Solutions
Real Estate Management Solutions
Maintenance Management Solutions
Energy Management Solutions
Engineering Document Management Solutions
Asset Management Solutions
Automate campus scheduling for classes, meetings, and exams with our EMS software.
Plan and manage conferences effortlessly with EMS software to impress guests and streamline operations.
Boost workplace flexibility and maximize space use with seamless desk and room booking.
Organize workplace or campus events smoothly, creating memorable experiences.
Optimize workspace, manage allocations efficiently, and reduce costs with our space management solutions.
Deliver projects on time and within budget by improving communication, collaboration, and efficiency with our software.
Streamline lease accounting for ASC 842, IFRS, and GASB compliance.
Manage leases efficiently by tracking key dates, analyzing costs, and ensuring compliance.
Centralize data and analytics for better insights, faster negotiations, and revenue growth.
Centralize facility and asset maintenance, automate work orders, and ensure compliance with our CMMS software.
Extend asset life, reduce downtime, and prevent costly repairs with data-driven monitoring.
Prevent equipment failures and extend asset life by detecting and addressing issues early.
Make sustainable, cost-efficient energy decisions by monitoring and optimizing power consumption.
Remotely monitor and control equipment with real-time data to predict issues, boost efficiency, and reduce downtime.
Easily share and collaborate on documents, creating a single source of truth for engineers and contractors.
Manage and analyze assets across their lifecycle to schedule maintenance, reduce downtime, and extend lifespan.
Improve visibility, automate work orders, and ensure compliance for efficient facility and asset management.
Resources
Browse our full library of resources all in one place, including webinars, whitepapers, podcast episodes, and more.
Support
Looking for access to technical support, best practices, helpful videos, or training tools? You’ve come to the right place.
About Accruent
Get the latest information on Accruent, our solutions, events, and the company at large.
Looking to invest in a CMMS? Here are 5 key criteria that will help you evaluate vendors and find the best system for your organization.
Once a company makes the decision to invest in a computerized maintenance management system (CMMS), the next step is evaluating vendors to determine which system is the best fit.
Defining CMMS selection criteria upfront is invaluable in streamlining the process and increasing the probability that the chosen CMMS will help a company to achieve their maintenance goals. Many factors influence a company’s maintenance priorities such as the size of operations, number of technicians, types of assets, etc. There is no “one size fits all” approach to CMMS selection, but the five key criteria to consider are:
These are certainly not the only criteria on which CMMS vendors should be evaluated, but they are areas that have a significant impact when it comes to long-term CMMS success.
The more complicated a CMMS is the greater the chance of failure. A complicated system is not necessarily the one with the most functionality, but instead refers to how the functionality is presented within the workflow of the system. Is it easy to transition from one screen to the next? Is the interface and workflow intuitive?
For organizations that are not currently using a CMMS, adopting software that changes how workers do their job can be intimidating to those inexperienced with technology. A CMMS that rates high in ease of use should have the capability to ease users into the system. For example, if there is extraneous information that will not be used by a company, can it be turned off?
To be thorough in evaluating ease of use, all users should be a part of the process. If technicians find a system difficult to use, they will not readily adopt it, which diminishes the value of the CMMS. Involve technicians and other key stakeholders in reviewing the user interface, workflow and other key features to ensure they are bought into the system.
Mobile functionality within a CMMS is valuable, as 50% of technicians now use a mobile device for work orders.¹ The power that a mobile CMMS provides means that while working on equipment in the field, a technician can complete the necessary tasks for the maintenance and repair efficiently:
Labor efficiency gains combined with more accurate maintenance performance metrics are a strong combination that enhance the overall value of a CMMS.
All mobile CMMS software is not created equal. Some tie users to a particular type of device. Device-agnostic mobile applications give users the flexibility to have diverse mobile devices and to change devices in the future without additional costs.
Even if mobility functions will not be implemented initially, the opportunity to add this capability later can be valuable.
A good CMMS not only helps companies manage their maintenance programs, but also serves as a repository for historical asset and maintenance work order information. To take advantage of the data, companies must convert it into actionable intelligence that drives continuous improvement. This process starts with establishing metrics and reporting that companies can then act upon to improve results. A good CMMS makes it easy for each user to extract and analyze data in the way that makes it most useful for them.
Companies have varied reporting needs at all levels of their organization. For example, an Operations VP responsible for multiple sites might want the ability to compare each site’s monthly maintenance spend on similar equipment. A maintenance supervisor at one of those sites might want to look at an asset’s average repair time. Flexible and configurable reporting is essential to an effective CMMS.²
Maintenance Connection's effective CMMS reporting provides a thorough library of reports that can deliver a good starting point. However, robust reporting must also offer the flexibility for companies to tailor reports to their specific needs. Reporting is a great vehicle to increase the value of a CMMS by enabling better informed business decisions.
There are two main scalability considerations to assess. The first is how the system fits a company. For instance, if the company has ten maintenance technicians, one operating unit, and one hundred assets, a CMMS with a complicated hierarchical structure might not be the best choice.
The second scalability consideration is the ability of a system to grow with an organization’s needs. If a company is rolling out a CMMS at one site, but may want to roll out to other locations in the future, they need to consider how easy or difficult a system’s design may make that expansion process.
While a vendor’s CMMS software is core to the selection and buying process, the vendor organization is equally important. Good vendors are partners with their customers in implementation, training and ongoing support. Implementation services are a natural part of a CMMS project. Thorough vendors acknowledge this and include these costs upfront. Companies should be able to ask vendors for a clear implementation plan with expected timeframes before starting a CMMS project. Companies can ask to meet potential resources that might be working on their project.
Training can take many forms and is not just a one-time activity. Any suggested formal training should be outlined clearly by the vendor and should define the duration, number of users that can be included in the sessions, the materials that will be provided, etc. Besides formal training, companies may want to inquire about online training options and other training resources that are available to users on a continuous basis.
As part of their proposals, CMMS vendors typically include how training will be conducted, how much it costs, what resources are available and any additional training options. If this information is not part of the original proposal, companies may want to ask for it.
Once a CMMS is in place, questions will arise, and the vendor’s support team is critical to helping companies work through any issues. A strong support team has 24/7 coverage and works quickly to resolve issues, escalating them when necessary. The support team also works with a vendor’s engineering and product management teams to identify any bug fixes needed based on collective customer feedback.
Companies considering a CMMS purchase will want to define their maintenance program goals first, then create their own list of CMMS selection criteria. The five key CMMS selection criteria above are core elements that can help differentiate one vendor’s CMMS from another. By asking the right questions upfront, companies can narrow their potential CMMS options quickly to those that best fit their needs.
With a narrowed potential CMMS list, companies can ask for a list of clients actively using the vendor’s CMMS to get an idea of the adoption within their industry and with similar sized companies. Companies may also want to look at online reviews and ask for references to get a better idea of the positives and negatives associated with each CMMS they are considering.
Learn about L’Oréal’s CMMS vendor evaluation process and why they chose Maintenance Connection. Ready to get started? Schedule a demo today!
Plan your investment with our CMMS pricing guide and ROI calculator.
Getting a handle on your equipment downtime can help your reduce costs, maximize efficiency and optimize operations. Here's how to calculate your ...
When choosing a CMMS, it's important to know what costs you can expect and what implementation you can afford. Here's what you need to know.
Want to know how to measure your true CMMS ROI and performance? Here's how to get the numbers.
Subscribe to stay up to date with our latest news, resources and best practices