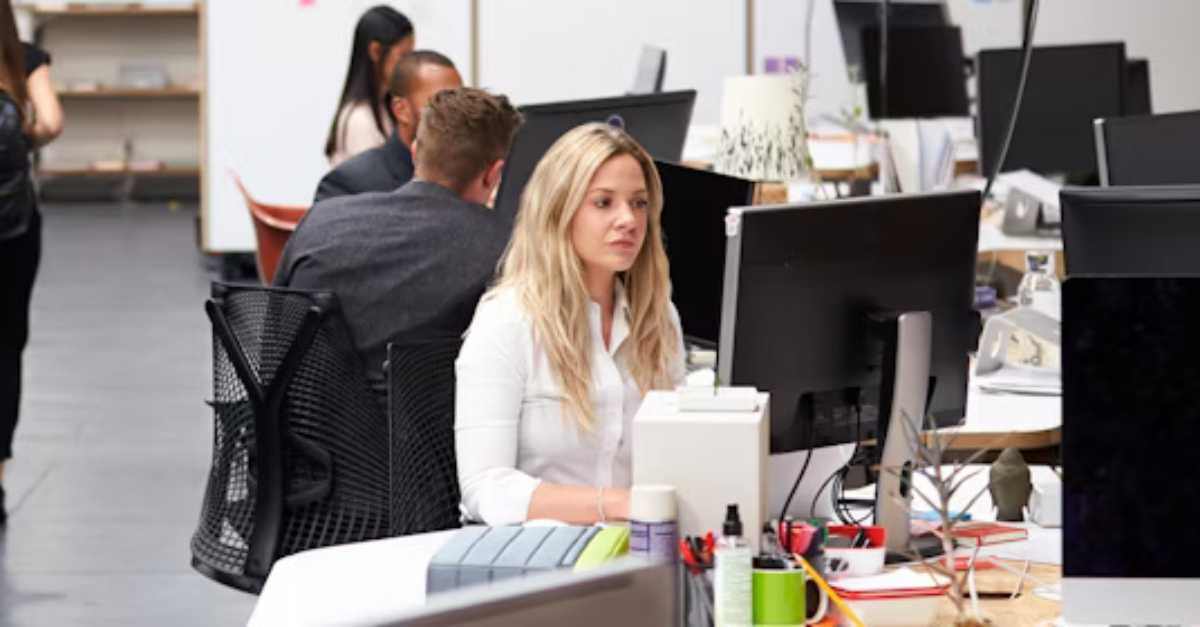
Maximizing Efficiency: The Role of Data in Space Planning and Management
Optimize space management with data-driven insights. Maximize data efficiency, reduce costs, and stay competitive with smart tech solutions and key ...
Solutions
Workplace Management Solutions
Real Estate Management Solutions
Maintenance Management Solutions
Energy Management Solutions
Engineering Document Management Solutions
Asset Management Solutions
Automate campus scheduling for classes, meetings, and exams with our EMS software.
Plan and manage conferences effortlessly with EMS software to impress guests and streamline operations.
Boost workplace flexibility and maximize space use with seamless desk and room booking.
Organize workplace or campus events smoothly, creating memorable experiences.
Optimize workspace, manage allocations efficiently, and reduce costs with our space management solutions.
Deliver projects on time and within budget by improving communication, collaboration, and efficiency with our software.
Streamline lease accounting for ASC 842, IFRS, and GASB compliance.
Manage leases efficiently by tracking key dates, analyzing costs, and ensuring compliance.
Centralize data and analytics for better insights, faster negotiations, and revenue growth.
Centralize facility and asset maintenance, automate work orders, and ensure compliance with our CMMS software.
Extend asset life, reduce downtime, and prevent costly repairs with data-driven monitoring.
Prevent equipment failures and extend asset life by detecting and addressing issues early.
Make sustainable, cost-efficient energy decisions by monitoring and optimizing power consumption.
Remotely monitor and control equipment with real-time data to predict issues, boost efficiency, and reduce downtime.
Easily share and collaborate on documents, creating a single source of truth for engineers and contractors.
Manage and analyze assets across their lifecycle to schedule maintenance, reduce downtime, and extend lifespan.
Improve visibility, automate work orders, and ensure compliance for efficient facility and asset management.
Resources
Browse our full library of resources all in one place, including webinars, whitepapers, podcast episodes, and more.
Support
Looking for access to technical support, best practices, helpful videos, or training tools? You’ve come to the right place.
About Accruent
Get the latest information on Accruent, our solutions, events, and the company at large.
Your CMMS is only as powerful as the data within it. Learn how to make sure that data is clean, useful, and relevant to your team.
A computerized maintenance management system (CMMS) can accurately be described as “a single source of truth” for all of your business-critical information. The idea is that, with all of your information synchronized in one centralized system, your business can more effectively schedule and record maintenance activities, thereby increasing efficiency, reducing downtime, budgeting more effectively, prioritizing work orders, and making data-driven decisions with much less downtime, mistakes and employee frustration.
But what information needs to be part of your CMMS for it to function effectively -- and what data can you leave out?
Here is what you should know.
Having the right data in your CMMS is absolutely foundational to its functionality. The whole purpose of the tool, after all, is to provide a centralized location where relevant maintenance and asset data can be quickly accessed and analyzed to make effective preventive maintenance and supply chain decisions.
More specifically, a CMMS will help you:
In an ideal world, this will let you run flawlessly until your next planned outage, which will ultimately reduce your costs and inefficiencies. And that is how things should be.
Well, you simply cannot make these kinds of data-driven decisions without the right data – and trying to do so defeats the purpose of the tool, resulting in the same incomplete, disparate or out-of-date information that you bought a CMMS to prevent.
That is why it is important that you ensure that the right data is inputted in the right format both during initial data entry and during entry of ongoing information.
Before you even start inputting your data, conduct a Data Quality Assessment to help you better understand your data quality and where you might need some reorganization or standardization. Here, particularly when you are first inputting data, it is important to validate what is in your current system against what is really on the floor in your facility.
Now, you clearly cannot assess all your data – it is just too much information. That is why we recommend that you choose random data from a few of your most critical systems – around 5-10% of your total data – to get a sense of where you stand and how clean that data is.
If you need a starting point, we recommend you begin with assets, followed by equipment, bill of materials, and the parts list. Then, move to your job plans for repairs. This is the most critical information to have right for effective maintenance.
And remember, if this information is totally off, you will need to clean up and validate that data as you input it into your CMMS.
When it comes to fixing, cleaning and inputting your data, you should prioritize the data based on business value and asset criticality. This can help you focus most heavily on the most important data for your business. Also, be sure to loop in your experts throughout this process to make sure that your data is effectively reviewed, validated, corrected and entered into your system.
Inputting this information will allow users to easily find where a piece of equipment operates and organize these locations into hierarchies. This will allow work orders to be associated with specific locations or pieces of equipment, which can streamline execution and allow for better tracking of asset lifecycle and asset performance.
You should also include accurate, detailed records on each asset in your facility. This should include all equipment-related data, including:
This information will allow for streamlined daily operations, and it will allow your organization to make effective repair and maintenance decisions. Analytically, this information can also help you get a broader understanding of equipment downtime and the cost of each asset, which can inform your budgeting and purchasing decisions down the line.
You can also include records about your maintenance personnel and technicians, including:
This information can help you track labor costs, schedule maintenance with the right personnel and more.
An inventory control module in your CMMS will allow you to more effectively track and manage inventory, including spare parts and obsolete parts. This can be a huge time and money saver, as having an accurate understanding of your inventory can help prevent technician delays and reorders of lost parts. Details that you should add to this module includes:
For your CMMS to function effectively, you must have effective work order tracking. This should include all relevant work order information, including:
Again, the more data is included and easy-to-access in the system, the more streamlined and efficient your operations will be.
Comprehensive historical data about your facility and equipment can provide the insight needed for effective preventive maintenance and root-cause failure analysis. This data can include historical information on asset preventive maintenance, construction, additions, modification, preventive maintenance (PM) and repairs.
Having comprehensive purchasing data in your CMMS can help you track orders and manage costs when you do purchase new parts or materials. This, in turn, can increase efficiency, reduce redundancy and lower costs over time. Relevant information here can include:
Your KPI metrics will help you evaluate the success of your maintenance program and your progress toward certain goals. It is important, then, that you select and input the right KPIs into your CMMS so you always have this information readily available.
We have covered the what – but what about the how? The right information cannot just be in your CMMS – it must be there in a format that is trustworthy, accessible and fully reflective of the physical environment it represents. That requires a few considerations.
Once the right data is inputted into your CMMS, it needs to be consistently cleansed, validated and managed. This is best accomplished by a CMMS administrator whose job it is to:
Without a dedicated administrator, these tasks will fall to existing employees. This will decrease data consistency, hinder employee efficiency and increase the likelihood of data errors.
Manual, paper-based processes invite mistakes and inconsistency. You will want to replace print work orders and supporting documents, then, with a mobile CMMS tool to streamline your data and make sure that:
Here, it is important to consult your technicians and figure out a data-entry method that is intuitive and user-friendly to them. They are the ones that are going to be inputting the data, after all – so their opinion matters most.
To maintain consistency, it is important that you standardize your naming conventions, your formatting and your data structure. That way, everyone that is looking at the data or inputting it will be able to understand it and easily access the information they need.
Everyone that will be interacting with your CMMS needs to know how to use it. This requires ongoing training through training videos, articles, demos and free trials. The right vendor will offer all of these services free of charge.
With the right CMMS system in place, you can really optimize your preventive maintenance operations and eliminate surprises, unplanned downtime, and unexpected emergency failures. And you should not accept anything less.
See how Trinchero Family Estates uses their CMMS to simplify their operations using it as a single source of truth for their work order data.
Optimize space management with data-driven insights. Maximize data efficiency, reduce costs, and stay competitive with smart tech solutions and key ...
Discover why good data structure, governance, and strategy are core to effective digital transformation and how to better organize data with the ...
Explore how asset management is meeting data management challenges by leveraging a cloud software for accessibility.
Subscribe to stay up to date with our latest news, resources and best practices