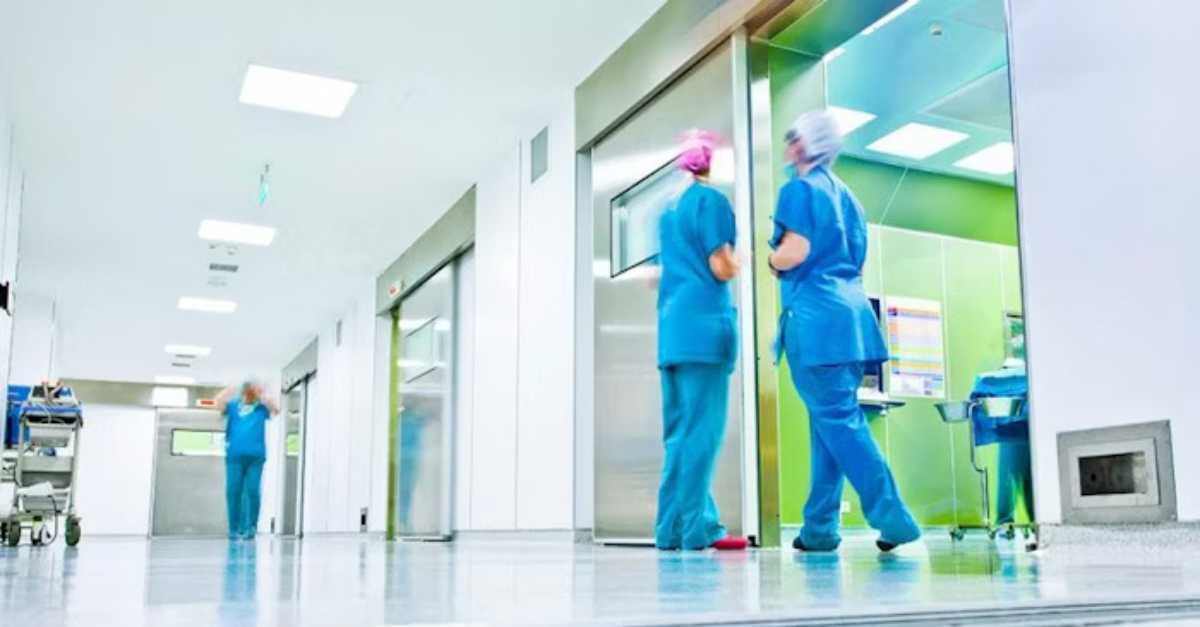
Why EOC Rounds in Healthcare are Important
Discover how to implement an EOC Rounds Program – and learn why it can help you maximize safety for everyone in your healthcare facility.
Solutions
Workplace Management Solutions
Real Estate Management Solutions
Maintenance Management Solutions
Energy Management Solutions
Engineering Document Management Solutions
Asset Management Solutions
Automate campus scheduling for classes, meetings, and exams with our EMS software.
Plan and manage conferences effortlessly with EMS software to impress guests and streamline operations.
Boost workplace flexibility and maximize space use with seamless desk and room booking.
Organize workplace or campus events smoothly, creating memorable experiences.
Optimize workspace, manage allocations efficiently, and reduce costs with our space management solutions.
Deliver projects on time and within budget by improving communication, collaboration, and efficiency with our software.
Streamline lease accounting for ASC 842, IFRS, and GASB compliance.
Manage leases efficiently by tracking key dates, analyzing costs, and ensuring compliance.
Centralize data and analytics for better insights, faster negotiations, and revenue growth.
Centralize facility and asset maintenance, automate work orders, and ensure compliance with our CMMS software.
Extend asset life, reduce downtime, and prevent costly repairs with data-driven monitoring.
Prevent equipment failures and extend asset life by detecting and addressing issues early.
Make sustainable, cost-efficient energy decisions by monitoring and optimizing power consumption.
Remotely monitor and control equipment with real-time data to predict issues, boost efficiency, and reduce downtime.
Easily share and collaborate on documents, creating a single source of truth for engineers and contractors.
Manage and analyze assets across their lifecycle to schedule maintenance, reduce downtime, and extend lifespan.
Improve visibility, automate work orders, and ensure compliance for efficient facility and asset management.
Resources
Browse our full library of resources all in one place, including webinars, whitepapers, podcast episodes, and more.
Support
Looking for access to technical support, best practices, helpful videos, or training tools? You’ve come to the right place.
About Accruent
Get the latest information on Accruent, our solutions, events, and the company at large.
Is a CMMS or an EAM most appropriate for your organization? What are the main distinctions between the two? Here's everything you need to know.
Table of contents
If you’ve made the decision to deploy a robust asset management tool for your business, you’re likely on the right track. The right software can empower your organization with data-driven insight, actionable information and powerful preventive maintenance capabilities.
And, if you’ve done your research, you likely already know that the two main players here are computerized maintenance management systems (CMMS) and enterprise asset management (EAM) software. But the lines between these tools are admittedly blurred, and there’s a ton of overlap that may hinder your ability to make a clear and effective decision between the two.
Here’s everything you need to know about CMMS, EAM and how to determine which tool is the best fit for your business.
Though the terms CMMS and EAM are often used interchangeably – and both tools can help organizations automate operations and move from reactive to preventive maintenance strategies – it’s important to note that the systems are not the same.
When they first came into existence decades ago, CMMS systems aimed to replace manual work and paper records in four key areas: work orders, preventive maintenance, inventory control and equipment history. But the first CMMS tools were primitive and inefficient data storage tools, and it was difficult to even run reports, let alone effectively analyze the data at hand. This has all changed.
Today, enterprise CMMS software focuses specifically on maintenance and centralizing information to facilitate and automate maintenance during the operational part of an asset’s lifecycle. In other words, a CMMS system exists to help you understand how your assets are doing now and what you should plan for in the future to maximize your uptime and revenue.
More specifically, a CMMS can provide your team with:
What’s more, many modern CMMS systems are using machine learning and AI developments to expand their predictive maintenance capabilities. Ultimately, this kind of physical asset insight can help your business increase efficiency, connect systems, improve team management, budget effectively, prioritize work orders, reduce downtime and more – all from one centralized, easy-to-use system.
That said, the core function of a CMMS remains to help businesses effectively execute work orders and optimize their maintenance operations during the operational part of the asset lifecycle.
As it relates to EAM, a CMMS can actually fit under the EAM umbrella and can be considered to be a component of a broader EAM system.
Enterprise Asset Management (EAM) software, on the other hand, provides a wider range of features to track, manage, and analyze asset performance and costs through the whole asset lifecycle, from acquisition to disposal.
Along with containing a CMMS component, a robust EAM solution can also provide features outside of preventive maintenance. Possible features include:
This broad suite of capabilities gives asset managers full transparency into the historical and present state of assets so they can report to other departments, optimize asset performance, reduce their total cost of ownership and more.
So which tool do you need for your business?
In recent years, this question has become more difficult to answer because there can be a significant amount of overlap between the two tools. Thanks, in part, to Wi-Fi, the internet and rising IoT capabilities, modern CMMS systems can offer enterprise-wide solutions that make them suitable for a multi-site business – just like an EAM.
Additionally, many CMMS systems – including Accruent’s Maintenance Connection – now offer EAM-type functionality and have the ability to easily merge with providers that strengthen their offerings considerably.
In short, you can find a CMMS system that is robust enough to offer EAM-type functionality – and you can certainly handle CMMS-level needs with an EAM.
That said, just because you can doesn't mean that you should. After all, you don’t want to simply “make something work” – you want to find the tool that is best suited to meet your technological capabilities, budget restraints and scope.
Ultimately, computerized maintenance management systems are dedicated, streamlined tools for managing maintenance operations and they’re not exclusively designed to provide extended functionality beyond that scope. If you have smaller maintenance operations and need a simple and effective way to manage your work orders, records and spare parts, this may be the ideal solution for you. Plus, CMMS software is usually much less costly than a more powerful EAM.
Enterprise asset management software, on the other hand, is often used by companies that have outgrown their CMMS system. If your organization has hundreds of physical assets and asset managers – along with complex systems and operations across multiple sites – then it may be time for you to make the switch.
Or don’t choose at all! Accruent’s Maintenance Connection solution can serve as both a CMMS or a full-function EAM. Watch a demo now.
Plan your investment with our CMMS pricing guide and ROI calculator.
Discover how to implement an EOC Rounds Program – and learn why it can help you maximize safety for everyone in your healthcare facility.
An enterprise asset management (EAM) system can help your organization drive maintenance improvement and increase your ROI. Here's how.
Is your healthcare organization up-to-date with The Joint Commission's latest PM compliance standards? Here's everything you need to know.
Subscribe to stay up to date with our latest news, resources and best practices