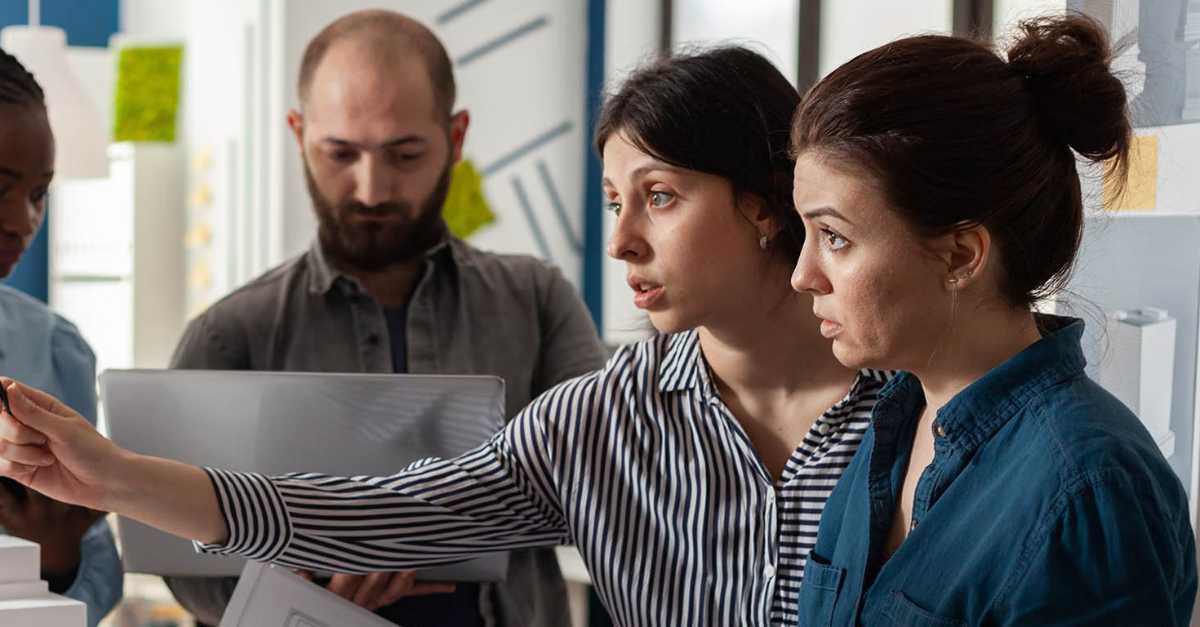
Navigating the Changing Global Workplace
Get a deeper look at the ever-changing workplace and what’s affecting the people, places, and assets you manage.
Solutions
Workplace Management Solutions
Real Estate Management Solutions
Maintenance Management Solutions
Energy Management Solutions
Engineering Document Management Solutions
Asset Management Solutions
Automate campus scheduling for classes, meetings, and exams with our EMS software.
Plan and manage conferences effortlessly with EMS software to impress guests and streamline operations.
Boost workplace flexibility and maximize space use with seamless desk and room booking.
Organize workplace or campus events smoothly, creating memorable experiences.
Optimize workspace, manage allocations efficiently, and reduce costs with our space management solutions.
Deliver projects on time and within budget by improving communication, collaboration, and efficiency with our software.
Streamline lease accounting for ASC 842, IFRS, and GASB compliance.
Manage leases efficiently by tracking key dates, analyzing costs, and ensuring compliance.
Centralize data and analytics for better insights, faster negotiations, and revenue growth.
Centralize facility and asset maintenance, automate work orders, and ensure compliance with our CMMS software.
Extend asset life, reduce downtime, and prevent costly repairs with data-driven monitoring.
Prevent equipment failures and extend asset life by detecting and addressing issues early.
Make sustainable, cost-efficient energy decisions by monitoring and optimizing power consumption.
Remotely monitor and control equipment with real-time data to predict issues, boost efficiency, and reduce downtime.
Easily share and collaborate on documents, creating a single source of truth for engineers and contractors.
Manage and analyze assets across their lifecycle to schedule maintenance, reduce downtime, and extend lifespan.
Improve visibility, automate work orders, and ensure compliance for efficient facility and asset management.
Resources
Browse our full library of resources all in one place, including webinars, whitepapers, podcast episodes, and more.
Support
Looking for access to technical support, best practices, helpful videos, or training tools? You’ve come to the right place.
About Accruent
Get the latest information on Accruent, our solutions, events, and the company at large.
Ensure assets are contributing to, not detracting from, the profitability of your towers. See how to better manage your depreciable and non-depreciable assets.
Table of contents
As you track and manage your towers and lease agreements more efficiently, you also need to track, manage and maintain your depreciable and non-depreciable assets. Your infrastructure lifecycle management system should allow you to manage and track equipment moves, replacements and losses as well as automate and track routine and ad hoc maintenance to ensure your assets are contributing to, not detracting from, the profitability of your towers.
Theft of tower equipment is an unfortunate, yet prevalent, reality with considerable costs to tower companies. Your system should allow you to quickly compare the equipment that should be at a site with what is actually at the site and what equipment vendors have invoiced you for. This allows you to identify, investigate and address suspicious activity, such as sites and vendors with higher-than-normal occurrences of losses.
Tracking equipment inspection records, planned maintenance, and other scheduled activities in spreadsheets is time consuming and cumbersome. Moving your preventive maintenance data and processes into an automated system helps to ensure that equipment is inspected and maintained in compliance with environmental and safety regulations and lease agreements, on a precise schedule with consistent process steps. This has the added benefit of extending the life of your assets, leading to decreased reactive work, lower asset failure rates and cost savings.
Manually processing maintenance work is inefficient. Using an infrastructure lifecycle management system, you can automatically dispatch jobs to your vendors, saving valuable time and resources. Processing your work orders through an automated system has the added benefit of capturing work data that can be used to look for trends that may help you to discover maintenance needs more quickly. The same system can then deliver process steps and documentation to ensure work is completed consistently and readily, and to allow workers in the field to provide immediate updates directly into the system.
Tracking the details of all of your assets, inspections, repair history and estimated costs associated with repairs and replacement, is too critical to juggle through spreadsheets. Moving asset information into a single system that includes location, cost history, warranty information and other vital asset documentation allows you to access information about assets more efficiently, and make more informed maintenance decisions.
One of the most important aspects of moving data and processes into an infrastructure lifecycle management system is the ability to access data on all of your assets from one system, giving you accurate, efficient reporting. This type of reporting allows you to watch for key indicators of problems, such as an increase in work orders that may indicate that a particular asset might have serious problems, or an increase in energy usage that may indicate theft of diesel fuel. Your system should allow you to see those key indicators in a summary view and then easily drill down into your data to uncover the source of the problem and determine the best course of action to resolve it quickly.
Get a deeper look at the ever-changing workplace and what’s affecting the people, places, and assets you manage.
Discover how to streamline management of real estate, assets, maintenance, and spaces with an integrated workplace management solution.
See how Seattle City Light Utilities implemented Meridian EDMS to attain document versioning control and data integrity over its 100 years’ worth of ...
Subscribe to stay up to date with our latest news, resources and best practices