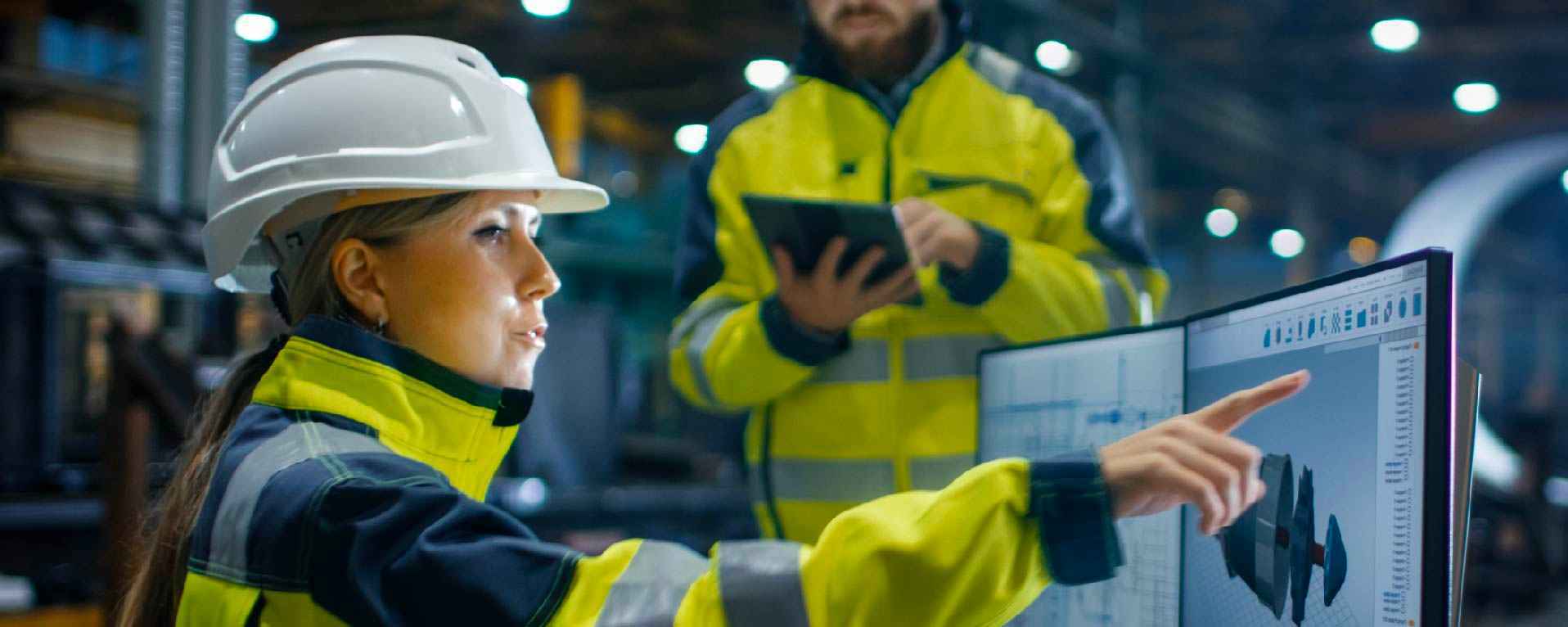
How Facility Managers Use CMMS for Better Inventory Management
Discover how CMMS inventory management helps facility teams track parts, reduce waste, and automate reorders for smoother maintenance operations.
Solutions
Workplace Management Solutions
Real Estate Management Solutions
Maintenance Management Solutions
Energy Management Solutions
Engineering Document Management Solutions
Asset Management Solutions
Automate campus scheduling for classes, meetings, and exams with our EMS software.
Plan and manage conferences effortlessly with EMS software to impress guests and streamline operations.
Boost workplace flexibility and maximize space use with seamless desk and room booking.
Organize workplace or campus events smoothly, creating memorable experiences.
Optimize workspace, manage allocations efficiently, and reduce costs with our space management solutions.
Deliver projects on time and within budget by improving communication, collaboration, and efficiency with our software.
Streamline lease accounting for ASC 842, IFRS, and GASB compliance.
Manage leases efficiently by tracking key dates, analyzing costs, and ensuring compliance.
Centralize data and analytics for better insights, faster negotiations, and revenue growth.
Centralize facility and asset maintenance, automate work orders, and ensure compliance with our CMMS software.
Extend asset life, reduce downtime, and prevent costly repairs with data-driven monitoring.
Prevent equipment failures and extend asset life by detecting and addressing issues early.
Make sustainable, cost-efficient energy decisions by monitoring and optimizing power consumption.
Remotely monitor and control equipment with real-time data to predict issues, boost efficiency, and reduce downtime.
Easily share and collaborate on documents, creating a single source of truth for engineers and contractors.
Manage and analyze assets across their lifecycle to schedule maintenance, reduce downtime, and extend lifespan.
Improve visibility, automate work orders, and ensure compliance for efficient facility and asset management.
Resources
Browse our full library of resources all in one place, including webinars, whitepapers, podcast episodes, and more.
Support
Looking for access to technical support, best practices, helpful videos, or training tools? You’ve come to the right place.
About Accruent
Get the latest information on Accruent, our solutions, events, and the company at large.
IoT will continue to have a massive impact in the maintenance management field - and it's a technology that you shouldn't sleep on.
It’s more evident than ever that technology affects the maintenance management field. From integrated processes to automation of normal tasks, technology rapidly improves our day-to-day duties.
One trend in the maintenance industry which cannot be ignored is the move to the Internet of Things (IoT), or the Smart Factory concept (Industry 4.0). McKinsey & Company notes that by 2025, IoT applications could have $11 trillion in business impact. Another McKinsey statistic that is relevant to the maintenance management industry is as follows:
Maintenance managers want to see reductions in both cost and downtime that can be achieved with the IoT. If your company hasn’t yet reaped the benefits of IoT for maintenance management, now is the time to get started. Continue reading to learn how the IoT impacts the industry.
Maintenance managers are responsible for ensuring hundreds of assets and machines are up and running efficiently. With hundreds of assets under review, wouldn’t it be easier if they proactively alerted you of preventive schedules, readings or equipment failure?
While machines may not speak, they do systematically work together via machine-to-machine (M2M) communication. Maintenance managers use M2M techniques to collect data on KPIs like uptime, unscheduled downtime or average repair time.
Coupled with IoT sensors, M2M data helps maintenance managers gain insight on how often an asset is underperforming, or how long it’s been since the last work order was performed. Business Intelligence tools are vital for creating reports from this information which can be used to better manage equipment and maintenance. Using this data, managers can map out when downtime will occur, part needs and tie this data back to their preventive schedules to improve uptime. But, make sure to select the specific technology for your data or function need, then pilot it with excellence. It is easy to get overwhelmed in the IoT world with all the options available today.
If your inventory management plan leaves you with an unruly warehouse, inefficient employees and low stock, it may be more of a cost center than an organized strategy. The average business spends around 25% to 35% of its budget on inventory costs. And you know that poor inventory management leads to inaccurate budgets, emergency orders, unaccounted for stock and shipment delays.
Maintenance managers can improve their inventory management with the IoT. For example, managers can connect their stockrooms to track orders, incoming shipments or low stock. Then, connect your stockroom with your CMMS to automate reorders, generate inventory reports and track costs to avoid shortages and improve the budget. Some CMMS does offer an integrated inventory system which allows for less work and expense.
Preventive maintenance is beneficial in theory but can be hard to strategize and implement without accurate data. Luckily, managers can use smart technology to track certain KPIs, and incorporate hard data into preventive maintenance schedules.
Embed sensors on devices to track abnormal conditions and generate alerts when unscheduled downtime is approaching. Coordinate these sensors to communicate with your CMMS to auto-generate work orders or notifications that a repair is needed soon. The benefits of your connected CMMS range from less unscheduled downtime to more efficient technicians. Plus, it’s an easier way for managers to accurately forecast schedules. One facility now runs lights out, and labor free due to the IoT abilities and increased uptime.
You have a CMMS. Now what? Maintenance Connection integrates with systems that rely on the IoT. These integrations help managers gain visibility and intelligence into their asset health to increase profitability and decrease downtime.
Discover how CMMS inventory management helps facility teams track parts, reduce waste, and automate reorders for smoother maintenance operations.
Help your warehouse managers overcome persistent pain points like high downtime and lost profits with a purpose-built CMMS.
A modern, purpose-built CMMS solution can help your healthcare organization improve asset and equipment availability, simplify compliance, enhance ...
Subscribe to stay up to date with our latest news, resources and best practices