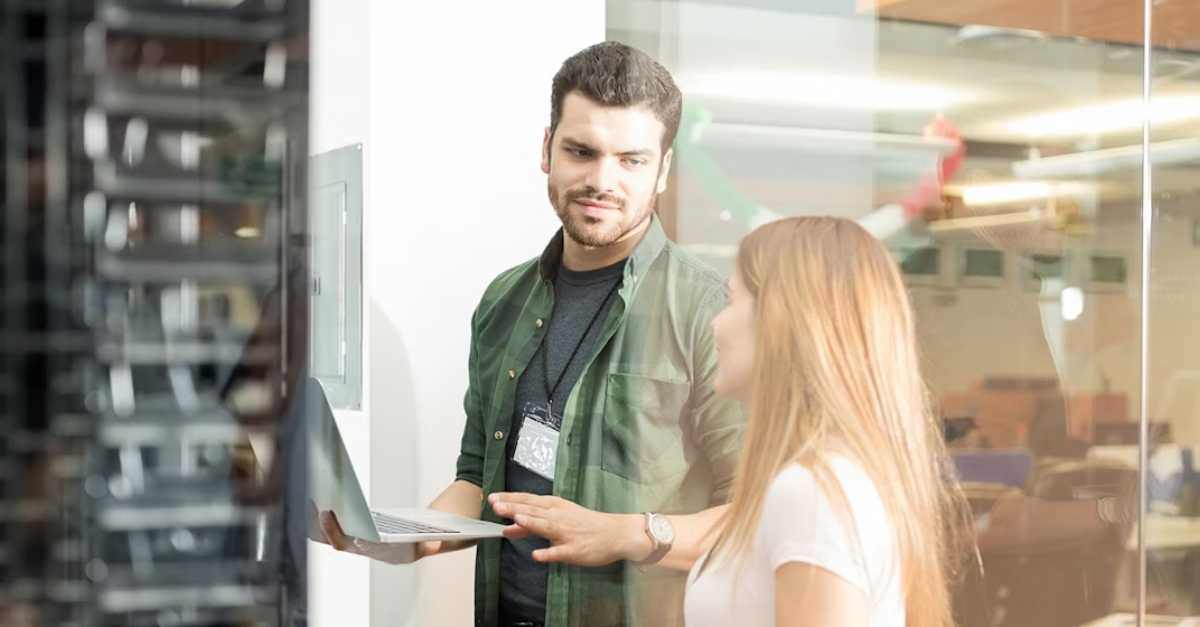
How the IoT Impacts Maintenance Management
IoT will continue to have a massive impact in the maintenance management field - and it's a technology that you shouldn't sleep on.
Solutions
Workplace Management Solutions
Real Estate Management Solutions
Maintenance Management Solutions
Energy Management Solutions
Engineering Document Management Solutions
Asset Management Solutions
Automate campus scheduling for classes, meetings, and exams with our EMS software.
Plan and manage conferences effortlessly with EMS software to impress guests and streamline operations.
Boost workplace flexibility and maximize space use with seamless desk and room booking.
Organize workplace or campus events smoothly, creating memorable experiences.
Optimize workspace, manage allocations efficiently, and reduce costs with our space management solutions.
Deliver projects on time and within budget by improving communication, collaboration, and efficiency with our software.
Streamline lease accounting for ASC 842, IFRS, and GASB compliance.
Manage leases efficiently by tracking key dates, analyzing costs, and ensuring compliance.
Centralize data and analytics for better insights, faster negotiations, and revenue growth.
Centralize facility and asset maintenance, automate work orders, and ensure compliance with our CMMS software.
Extend asset life, reduce downtime, and prevent costly repairs with data-driven monitoring.
Prevent equipment failures and extend asset life by detecting and addressing issues early.
Make sustainable, cost-efficient energy decisions by monitoring and optimizing power consumption.
Remotely monitor and control equipment with real-time data to predict issues, boost efficiency, and reduce downtime.
Easily share and collaborate on documents, creating a single source of truth for engineers and contractors.
Manage and analyze assets across their lifecycle to schedule maintenance, reduce downtime, and extend lifespan.
Improve visibility, automate work orders, and ensure compliance for efficient facility and asset management.
Resources
Browse our full library of resources all in one place, including webinars, whitepapers, podcast episodes, and more.
Support
Looking for access to technical support, best practices, helpful videos, or training tools? You’ve come to the right place.
About Accruent
Get the latest information on Accruent, our solutions, events, and the company at large.
Inventory management is a huge task for any manufacturing team, and it can be costly and time-consuming when executed ineffectively. Here's how a CMMS can help.
Managing inventory is a labor-intensive task that requires accuracy and efficiency. Statistics show that sales representatives typically spend 65% of their time on non-customer facing activities, such as inventory control.
As consumer demands change and inventory levels fluctuate, inventory management within a facility is critical for staying ahead of the market and competition.
Read on to learn three ways CMMS helps facility managers automate inventory control with features like comprehensive inventory reporting, barcoding and min/max planning.
A Computerized Maintenance Management System (CMMS) streamlines inventory management by automating and centralizing key processes. It provides real-time visibility into inventory levels, tracks parts usage, and integrates with maintenance workflows to ensure that the right parts are available when needed. By reducing manual tracking and minimizing stockouts or overstock situations, a CMMS enhances operational efficiency and supports proactive maintenance strategies.
Inventory reports are an integral part of actively managing a facility. If too much inventory is stocked, the facility risks high carrying costs, or the chance that products may become outdated or devalued. To bring overhead costs down and keep a better pulse on inventory, managers use reporting tools to track progress, predict trends and manage maintenance budgets.
With CMMS software, facility managers are able to retrieve reports quickly and effortlessly for analysis. Not only does this simplify communication between facility managers and technicians, but it also reduces equipment downtime and improves inventory management. When used to its fullest potential, the CMMS becomes a central database for all maintenance-related expenses and operations.
Comprehensive inventory reporting is a proactive way for facility managers to control inventory and align budgets with set expectations. The result? Less asset downtime when maintenance is properly scheduled. From there, the facility manager is able to forecast budgets and reduce unnecessary spending.
There are several factors facility managers consider when determining how much inventory to maintain in stock. A large inventory can have several notable disadvantages including illiquidity, markdowns and obsolescence. However, understocking can be just as dangerous, as you run the risk of missing out on sales and losing consumer loyalty. Plus, the maintenance team may suffer if an emergency work order comes in that requires out-of-stock inventory to fulfill it.
CMMS features, such as barcode scanning, improve management efficiency and productivity by eliminating manual data processes. With barcoding technology, facility managers are able to accurately record every aspect of a transaction. This reduces data-transcription errors common with paper records.
Barcoding technology also provides a quick way for facility managers to link work orders, perform inventory counts, and receive purchase orders. Not only does this eliminate error, but it also saves time and money.
The ability to properly forecast customer demand is essential for inventory turnover rates. To optimize inventory, facility managers can rely on CMMS features such as min/max inventory ordering. This is frequently referred to as Economic Order Quantity (EOQ), the number of units that a company should add to inventory with each order to minimize variable inventory costs.
Min/max inventory planning gives facility managers the ability to monitor inventory levels and calculate appropriate reorders. As inventory is continually replenished, fewer shortages are bound to occur. This increases inventory turnover rates and satisfies customer demand. It also aids in spare parts management.
Mix/max inventory planning also reduces the chances of inventory stockout. This means that with no inventory, production comes to a halt. As a result, the facility is unable to complete work orders, which results in slower response rates, longer asset downtime and poor customer service.
Maintenance Connection provides a full suite of inventory management tools built specifically for maintenance and facilities teams. Everything is designed to help you track, manage, and optimize inventory without adding unnecessary complexity.
Set minimum and maximum thresholds for each part, so when stock levels fall below a set point, the system can automatically notify your team or even generate a purchase request. This helps prevent part shortages that delay work and ensures high-use items are always on hand.
Speed up inventory counts and part checkouts with barcode scanning. Technicians can simply scan a part to pull up details, issue it to a work order, or update inventory records in real time. It’s fast, accurate, and reduces manual entry errors.
Whether you're managing a single facility or multiple campuses, you can track inventory by location and easily transfer parts between stockrooms. This gives you visibility into what's available across your entire operation—without duplicating orders or wasting resources.
Built-in analytics let you review parts usage trends, identify slow-moving inventory, and calculate carrying costs. This makes it easier to forecast demand, optimize reorder points, and improve budget planning.
With mobile functionality, technicians can check part availability, request items, or log usage directly from the job site. It reduces downtime, eliminates extra trips to storerooms, and improves productivity in the field.
Link parts and tools directly to maintenance tasks.
By combining these tools in one easy-to-use platform, Maintenance Connection helps teams work more efficiently, cut inventory costs, and reduce downtime.
The New York Times struggled to find a way to organize its assets and track the health of equipment plant-wide. With thousands of employees spread out across the plant, the facility needed a way to report on equipment downtime, work order status, and schedule updates.
The New York Times implemented Maintenance Connection across its College Point facility to streamline asset tracking, automate preventive maintenance, and adapt to shifting equipment usage. The system also supports inventory planning by helping the team anticipate parts needs and manage inventory more effectively. Its user-friendly interface and built-in communication tools made it easy to roll out across the maintenance team.
Read more on The New York Times case study
With Maintenance Connection, we can do a lot of automated preventive maintenance based on equipment usage. So if one piece of equipment is running a lot more than another, we’re going off cycle-based counts and those PMs are being scheduled out automatically.”— Greg Zarafa, Maintenance Manager at The New York Times
Husky Rack and Wire used a very manual, email-based process and there were many errors in keeping maintenance and inventory in orders.
Husky Rack and Wire implemented Maintenance Connection’s robust inventory module, which includes barcoding of parts and inventory management. The goal is to have cross-departmental visibility into their parts and inventory warehouse to help them save money, stock correct parts, and better understand their inventory needs.
Read more on Husky Rank and Wire case study
We needed somebody that could come in and implement something very well for us. The MC implementation consultant came in and did that. Everything was scattered all over the place. Everything went great, we never had any problem.”— Stegall, Husky Rack and Wire
Even with the right tools in place, good inventory management also comes down to having consistent processes and routines. Here’s how to get the most out of your CMMS:
Schedule periodic checks to verify actual stock levels against what's listed in the system. Audits help catch discrepancies early, reduce shrinkage, and keep your data accurate—especially if you’re managing multiple stockrooms.
Standardize part names, descriptions, and codes so everyone on your team can quickly identify and locate what they need. Avoid using abbreviations or slang that may not be universally understood.
Make sure everyone—from technicians to stockroom managers—understands how to receive, issue, and return parts properly within the CMMS. This ensures accountability, reduces errors, and keeps inventory data reliable.
Use your CMMS to link parts to scheduled tasks and PMs. When you know which parts are required ahead of time, you can confirm availability, reduce last-minute rush orders, and keep maintenance work on schedule.
Use your system’s reporting tools to analyze what’s working—and what isn’t. Identify excess stock, high-cost items, or gaps in reorder settings, then adjust your processes based on the data.
Strong inventory management doesn’t just support smoother operations—it empowers your team to be more proactive, reliable, and cost-effective. With a CMMS like Maintenance Connection and the right best practices, managing inventory becomes far more strategic—and far less stressful.
IoT will continue to have a massive impact in the maintenance management field - and it's a technology that you shouldn't sleep on.
Get the ultimate guide to asset management systems and software, which covers what they are and how they can streamline operations and maximize asset ...
Help your warehouse managers overcome persistent pain points like high downtime and lost profits with a purpose-built CMMS.
Subscribe to stay up to date with our latest news, resources and best practices