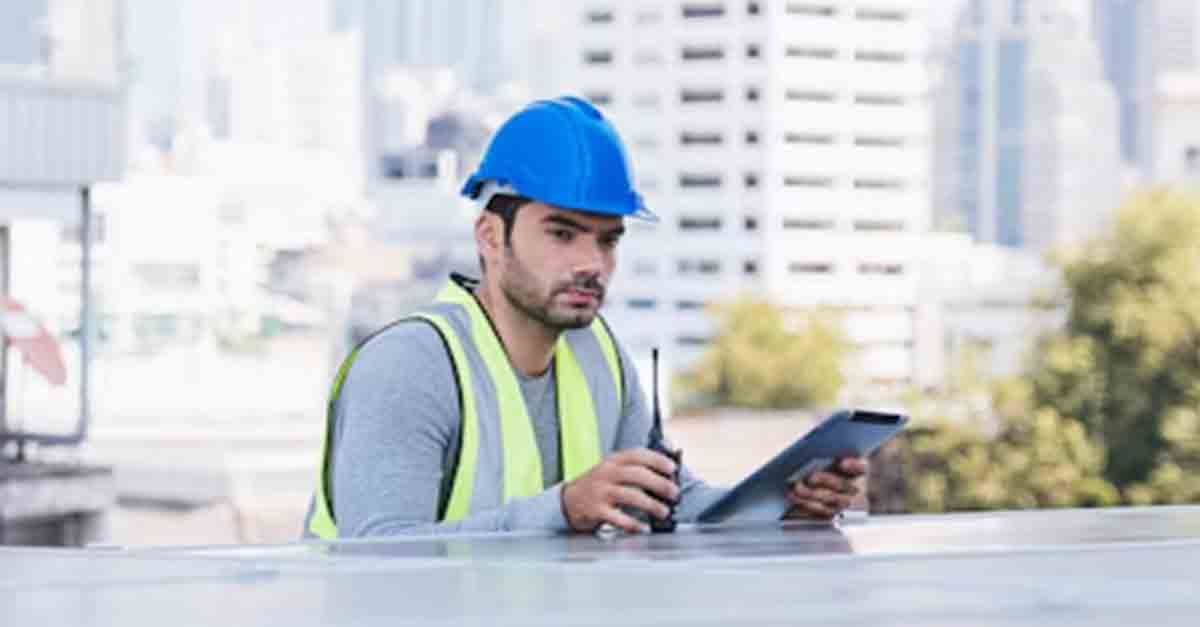
EDMS Software
Understand EDMS software basics and benefits, and how Accruent’s own EDMS platform — Meridian — can drive significant value for your business.
Solutions
Workplace Management Solutions
Real Estate Management Solutions
Maintenance Management Solutions
Energy Management Solutions
Engineering Document Management Solutions
Asset Management Solutions
Automate campus scheduling for classes, meetings, and exams with our EMS software.
Plan and manage conferences effortlessly with EMS software to impress guests and streamline operations.
Boost workplace flexibility and maximize space use with seamless desk and room booking.
Organize workplace or campus events smoothly, creating memorable experiences.
Optimize workspace, manage allocations efficiently, and reduce costs with our space management solutions.
Deliver projects on time and within budget by improving communication, collaboration, and efficiency with our software.
Streamline lease accounting for ASC 842, IFRS, and GASB compliance.
Manage leases efficiently by tracking key dates, analyzing costs, and ensuring compliance.
Centralize data and analytics for better insights, faster negotiations, and revenue growth.
Centralize facility and asset maintenance, automate work orders, and ensure compliance with our CMMS software.
Extend asset life, reduce downtime, and prevent costly repairs with data-driven monitoring.
Prevent equipment failures and extend asset life by detecting and addressing issues early.
Make sustainable, cost-efficient energy decisions by monitoring and optimizing power consumption.
Remotely monitor and control equipment with real-time data to predict issues, boost efficiency, and reduce downtime.
Easily share and collaborate on documents, creating a single source of truth for engineers and contractors.
Manage and analyze assets across their lifecycle to schedule maintenance, reduce downtime, and extend lifespan.
Improve visibility, automate work orders, and ensure compliance for efficient facility and asset management.
Resources
Browse our full library of resources all in one place, including webinars, whitepapers, podcast episodes, and more.
Support
Looking for access to technical support, best practices, helpful videos, or training tools? You’ve come to the right place.
About Accruent
Get the latest information on Accruent, our solutions, events, and the company at large.
An engineering document management system is a type of electronic DMS focused specifically on an organization's engineering drawings, documents, and data.
Table of contents
An EDMS is a robust engineering document management software designed to centralize an organization's dynamic and often complex assets. These may include engineering documents, drawings, and data, thereby replacing outdated, disparate, or manual systems.
Yes, and no. They are both document management systems (DMSs), and they are both electronic, but that is where the similarities end. An engineering document management system is a particular flavor of an electronic document management system purpose-built for engineering documents, drawings, and data. It optimizes the complex and dynamic documents you find in asset-heavy organizations.
In the engineering, construction, and manufacturing industries, an EDMS like Meridian can connect to and inform building information modeling (BIM) and facility and asset management tools such as Maintenance Connection to improve operational connectivity and ensure important data is accessible company-wide.
Conversely, an electronic document management system is built for storing and managing unstructured data that undergoes very little change, such as legal and financial documents or marketing collateral. An electronic document management system is not well suited for asset data and engineering drawings, such as CAD files, BIM models, and schematics.
Businesses and organizations find that a well-designed and properly implemented EDMS can help their users tackle some redundant, mundane, and error-prone tasks of day-to-day operations. Using the robust features of an engineering document management system, employees work faster and more efficiently, especially when it gives them the ability to:
And make no mistake — an EDMS is more than a digital filing cabinet. It's a document organizer, distributor, and integrator that will simplify processes and allow your team to quickly use your data rather than fumble through it.
This comprehensive pricing calculator is designed to provide you with a clear, customized cost breakdown for Meridian’s EDMS software.
When choosing an EDMS system for your organization, keep in mind that the best engineering document management systems include the following features:
Revision controls and approval processes will help you streamline workflow information like document type and the number of working copies. This can ultimately simplify collaboration and ensure everyone is working on the right page at the right time.
Automatic document version control and auditing help ensure that all versions and drafts of a document are accurately recorded and managed across different teams and devices. This type of content management can help regulatory compliance and ensure that all users have access to up-to-date, accurate information to maximize productivity and safety and ensure data integrity.
The assets and documents in both applications are 100% identical. As a result, our people have a better view of the as-built environment and, therefore, work more efficiently. Consequently, management costs have been reduced."— Rene Baron, Maintenance & Engineering Manager, BASF
A robust EDMS software will pull information from other key systems and departments — including a CRM, EAM, or CAD software — to ensure that your mission-critical data is always effectively tracked, recorded, and synchronized into a single source of truth.
By consolidating our engineering documents into one central, controlled system and syncing properties with SolidWorks, Meridian has enabled our staff to find relevant drawings and parts 93% faster than before."— Zaneb Khan, Systems Technician, MSCM
Make document storage and document sharing more user-friendly with an EDMS system. Share documents, organize your electronic files, simplify your document workflow, control your file formats, and optimize file sharing in just a few clicks.
Maintaining ongoing compliance with regulatory bodies requires easy-to-follow audit trails, strict document authorizations, and — according to ISO engineering standards — strict document version control. The right engineering document management software can help set permissions and control document access to facilitate ongoing compliance. It can also connect your documents to records retention schedules, allowing your team to turn active documents into compliant records easily.
With Meridian, we ensure compliance with Joint Commission International standards as well as other equipment and government requirements, which allows us to better serve our patients and stay focused on our mission of contributing to the future of healthcare and medical science."— Willy Baten, Information Specialist, Real Estate & Infrastructure, Radboudumc
In a COVID-19 world, organizations and team members are forced to work across facilities and devices more than ever before. Meridian EDMS offers cloud deployments and mobile capabilities to help ensure data integrity, content management, and document control across devices and locations.
Distance is irrelevant with Meridian. Whether you're an engineer at a power plant or a maintenance technician out in the field, you have reliable access to a single source of information. Meridian has significantly improved our team collaboration at all levels.— Janet Hart, Technical Services Manager, Generation Operations & Engineering, Seattle City Light
With manual data entry or disparate document management systems, only one person can access an up-to-date document, and no one else can work on the same project until that document is shared or copied. This leads to low productivity, poor execution, ineffective records management, and even injuries. The right EDMS will avoid such concerns with multi-site capabilities and widely available schematic information to help users understand the as-built environment, schedule, complete work orders, and carry out concurrent engineering.
By enabling users to easily compare drawing revisions and highlight what has changed, Meridian has improved the efficiency and quality of our engineering projects."— Janet Hart, Technical Services Manager, Generation Operations & Engineering, Seattle City Light
If the right data is missing or difficult to find, it can be difficult to execute work orders or complete workflows. The right EDMS can require completing certain fields and organizing relevant documents to ensure that the right information is in the right place at the right time.
A robust document management system will provide the capabilities and tools your team needs to modify documents and streamline updates or decision-making effectively. This includes mark-up tools like annotations, redactions, highlighting, stamps, and text boxes.
Like any filing cabinet or library, an EDMS must be effectively hierarchically structured, organized, and indexed to be useful. In Meridian's engineering document management system, your digital documents are available in a central repository. And they can be organized by any parameters you choose, including creation date, department, and more.
With an EDMS's hierarchical structure, metadata, search, and archival functionalities, finding the right information at the right time is easier than ever. These tools will help you track key milestones like creation dates, modifications, reviews, and approval statuses while effortlessly searching for and locating the files you need across folders and repositories.
Many factors — including an aging asset infrastructure, reactive maintenance practices, and incomplete document and preventive maintenance (PM) information — can lead to skyrocketing maintenance costs and inefficiencies. This is unsustainable in today's lean environment. Accruent's engineering document management system, Meridian, can reduce these maintenance costs while also extending the asset lifecycle and ensuring a safer workplace.
By connecting to other relevant data sources such as CAD, CRM, CMMS, or EAM applications, engineering document management system software can maintain the integrity of your data and help create a single source of truth for your mission-critical information. This can resolve common pain points like out-of-date information, incomplete information, or incorrect active versions.
A document management solution like Meridian makes information, documentation, and schematics easily accessible during any project or even an emergency by offering concurrent versions of documents and drawings. Meridian also maintains the integrity of data throughout the asset lifecycle and provides a comprehensive CAD software agnostic solution for engineering drawing document management, thereby creating a single source of truth for all important information.
By creating a single source of up-to-date information that removes silos and integrates with our EAM solution, Meridian has helped us reduce maintenance errors by 50% and save $20,000 annually in unnecessary rework."— Willy Baten, Information Specialist, Real Estate & Infrastructure, Radboudumc
Mistakes and redundancies caused by missing information or poor document control can cost time, efficiency, and productivity. A comprehensive EDMS will facilitate document search and offer automated document data completion and updates to reduce such mistakes and increase ROI.
Meridian helps over 350,000 professionals keep their mission-critical documentation up to date. It also ensures that data is easily accessible by the right people while maximizing staff productivity, breaking down silos between departments, and supporting personnel safety.
This widely available, comprehensive information can close the skills gap and allow for better training and knowledge management within an organization.
By bridging the gap between maintenance and engineering and integrating with IBM Maximo, Sund & Bælt has improved efficiency of its entire maintenance operation. Our personnel find Meridian very easy to use. It's now indispensable to them."— Kurt Lauvring, Project Manager, Sund & Baelt
In asset-heavy industries and environments, preventive asset maintenance and maximized asset reliability are crucial to increased margins and effective job completion. Such reliability requires complete and easily accessible maintenance data. A powerful EDM system provides this data, allowing organizations to easily track, manage, and use all relevant asset documentation and maintenance data. This ultimately breaks down communication lifecycles, increases technician efficiency, and improves asset safety and compliance.
To increase processes and improve productivity, an EDMS can provide a 10,000-foot view of how documents are being used and how well your document-driven processes are working. Use this insight to reward employees, restructure processes, and drive ROI.
Eliminate the need to dedicate physical space, employee bandwidth, and operational budgets to maintain file storage and organization.
Data breaches, document loss, and compliance concerns are real pain points, particularly in an unorganized digital, cloud-based environment. By controlling information access and offering consistent security updates, an EDMS can help your organization effectively address and sidestep such concerns.
Immediately upon implementation, an EDMS can replace current paper archives, drastically reducing the time and budget spent managing paper records. In the long term, more effective search and automated document management can transform efficiency and release funds to other business-critical verticals.
Data extraction, implementing workflows, invoicing, contracting — all these internal processes can be complicated and slow. An EDMS's automated data extraction, search capabilities, and workflow templates can reduce such bottlenecks, improving company-wide efficiency and uptime.
An EDMS can be useful for many asset-heavy businesses, providing a single source of truth for engineering documentation that can reduce inefficiencies and improve decision-making.
An EDMS can be used in a range of asset or information-heavy industries. It's also an ideal tool for businesses that rely on paper-based operations (and notice the resulting inefficiencies or bottlenecks) or for those that have digital documents living in many disconnected systems or repositories (i.e., in Word documents, PDFs, Excel sheets, PowerPoints, emails, mobile documents, etc.)
For professionals in these industries and situations, an EDMS can help resolve common pain points, including:
An EDMS can also be an essential component of broader digital transformation. It can inform strategies and processes such as preventive maintenance and business process automation that will modernize your built environment.
By centralizing disparate information and providing a simple tool for searching documents, completing work orders, maintaining compliance, and more, an EDMS can help users across industries and verticals to:
Initially, your IT department can spearhead your EDMS initiatives and work to import data and standardize information across devices and team members. That said, implementation can often be complex – and Accruent experts are certainly here to help you begin, scale and standardize the process.
For ongoing maintenance, you can also consider hiring an electronic document controller to oversee the daily document management process. More specifically, this person will:
Accruent offers robust EDMS tailored to streamline the management of technical documents and drawings throughout their lifecycle. By providing centralized repositories, these solutions ensure that teams have instant access to the most up-to-date information, enhancing safety and operational efficiency.
RedEye is a modern, cloud-based EDMS designed to meet the needs of asset-intensive industries. It centralizes drawings and documents into a mission-critical solution, providing accurate information to both office and field personnel. RedEye enhances business processes and productivity by making data management more efficient and reliable. Notably, it offers unlimited user access without the need for additional CAD licenses, promoting seamless collaboration across teams.
Meridian serves as a centralized repository for storing, organizing, and controlling engineering documentation, ensuring that the right people have access to accurate information when needed. This system supports compliance and streamlines document changes, reducing maintenance costs, asset downtime, and project rework, while increasing employee safety.
Air Liquide, a world leader in gases, technologies, and services for both industry and health, had challenges in locating critical documents, especially engineering drawings, and had to rely on a few individuals with specialized knowledge. Recognizing these challenges, Air Liquide sought Meridian solution that could help them with:
Read more on Air Liquide’s success story with Accruent EDMS
Seattle City Light, the public utility providing electrical power to Seattle, Washington, and its metropolitan area, had challenges with managing the company’s 300,000 documents and drawings, and tracking their revisions. Without Accruent Meridian, they did not have a clear workflow processes, resulting in inefficiencies. Here are what they get after implementing EDMS:
Read more on Seattle City Light’s success story with Accruent EDMS
An electronic document management system (eDMS) is a type of software that stores, organizes, and manages documents in the form of electronic files for an organization. This system works best for documents that do not undergo much change, such as legal files, financial reports, marketing collateral, and scanned posts.
A digital engineering document management system is a type of electronic document management system purpose-built for engineering documents and drawings. It centralizes, organizes, and manages these documents while providing users with complete, actionable facilities and asset data they can use to increase efficiency and save money. It ultimately provides a single source of truth for all documentation, helps organizations maintain regulatory compliance, provides configurable workflows to streamline collaboration with all internal departments, provides comprehensive document version control, and simplifies auditing.
There are a few key features of a best-in-class engineering document management system. Above all, the right document management system must be easy-to-use, intuitive, and highly adopted by your employees. It also needs to provide a single source of truth for all mission-critical data to maintain the quality, accuracy, and completeness of your data and metadata. Likewise, it offers easy-to-configure workflows that allow for streamlined collaboration, easy document version control, and auditing of documents to maintain regulatory compliance. It also ensures that everyone is working on the correct version, provides accessible data to maximize staff productivity, and supports personnel safety.
The right engineering document management system will provide many advantages, including helping users process, store and retrieve records, simplify document version control, and streamline collaboration across departments, facilities, and devices. It can also improve project timelines, audit and inspection readiness, increase document control and security, lower costs, streamline knowledge management, and facilitate compliance.
There are key differences between an engineering document management system (EDMS) and a content management system (CMS). While both tools work to manage documents and content, a CMS is generally used to store web content from various websites, while an EDMS focuses more on engineering documentation for storage, reference, workflow management, and process improvement.
An engineering document management system delivers both immediate and long-term ROI improvements. An EDMS can immediately improve cash flow in the short term by reducing paper costs and increasing employee efficiency. Over time, ROI improvements will be seen in savings per document, reduced timelines for companies for payroll, turnaround, invoicing, and other key processes. Also, document-related cost reduction, more efficient customer service and public service, reduced storage and archival costs, and more effective collaboration and document modification.
If you're looking for examples of engineering document management systems, keep in mind that there's a lot of variety, including the functionalities and the real results they can deliver for your business. Consider your company's scale, complexity, and document management needs when evaluating these options. Here are some real examples of how Meridian EDMS helped organizations: MSCM Ltd integrated Meridian with Solidworks (one of their existing systems) to consolidate documents and streamline their document management. Zurich Airport used Meridian to improve data and plan consistency across their organization. Seattle City Light improved its engineering data integrity and, in turn, its compliance and productivity.
There are many competing standards worldwide for BIM and EDM tools, though ISO standards are essentially replacing these, which the entire world will eventually adopt. These include ISO 9001, which calls for document control. In other words, ISO 9001 tries to ensure that the right people have access to documents when needed, that those documents are up-to-date, and that no unauthorized users can access or change a document's contents. This ultimately helps ensure that essential engineering documents are up-to-date, comprehensive, and trustworthy, increasing compliance and improving operational efficiency over time.
An EDMS can provide many necessary improvements to operations and workflows, particularly for businesses with lots of documentation or those looking to digitally transform their operations. These benefits include cost savings, simplified compliance with ISO 9001, Sarbanes Oxley regulations, HIPAA, and other regulatory bodies, improved disaster recovery, employee productivity, audit management, automation of the document workflows, and security.
Understand EDMS software basics and benefits, and how Accruent’s own EDMS platform — Meridian — can drive significant value for your business.
Discover the essential role of a document control system in 2024. Learn how it streamlines document management, ensures compliance, and boosts ...
Explore the definition, benefits, and key features of a document repository. Learn how it can improve your document management process.
Subscribe to stay up to date with our latest news, resources and best practices