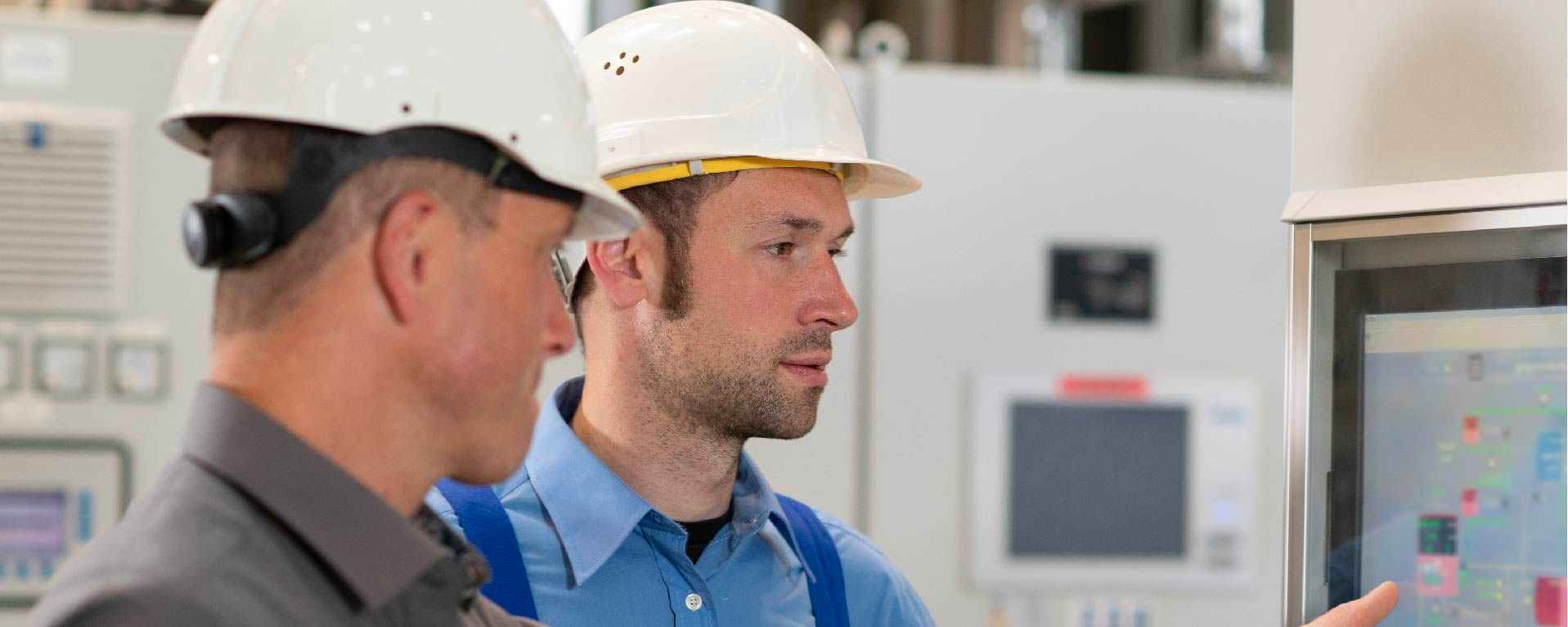
Top Benefits of Integrating CMMS with an ERP System
Integrating your CMMS and ERP systems can improve communication, maximize insight and facilitate effective data management. Read on for details.
Solutions
Workplace Management Solutions
Real Estate Management Solutions
Maintenance Management Solutions
Energy Management Solutions
Engineering Document Management Solutions
Asset Management Solutions
Automate campus scheduling for classes, meetings, and exams with our EMS software.
Plan and manage conferences effortlessly with EMS software to impress guests and streamline operations.
Boost workplace flexibility and maximize space use with seamless desk and room booking.
Organize workplace or campus events smoothly, creating memorable experiences.
Optimize workspace, manage allocations efficiently, and reduce costs with our space management solutions.
Deliver projects on time and within budget by improving communication, collaboration, and efficiency with our software.
Streamline lease accounting for ASC 842, IFRS, and GASB compliance.
Manage leases efficiently by tracking key dates, analyzing costs, and ensuring compliance.
Centralize data and analytics for better insights, faster negotiations, and revenue growth.
Centralize facility and asset maintenance, automate work orders, and ensure compliance with our CMMS software.
Extend asset life, reduce downtime, and prevent costly repairs with data-driven monitoring.
Prevent equipment failures and extend asset life by detecting and addressing issues early.
Make sustainable, cost-efficient energy decisions by monitoring and optimizing power consumption.
Remotely monitor and control equipment with real-time data to predict issues, boost efficiency, and reduce downtime.
Easily share and collaborate on documents, creating a single source of truth for engineers and contractors.
Manage and analyze assets across their lifecycle to schedule maintenance, reduce downtime, and extend lifespan.
Improve visibility, automate work orders, and ensure compliance for efficient facility and asset management.
Resources
Browse our full library of resources all in one place, including webinars, whitepapers, podcast episodes, and more.
Support
Looking for access to technical support, best practices, helpful videos, or training tools? You’ve come to the right place.
About Accruent
Get the latest information on Accruent, our solutions, events, and the company at large.
A CMMS can bring game-changing benefits to your organization — but only if you choose the right one. Here's what to look for in a system.
If your company already has a computerized maintenance management system (CMMS), you are familiar with the reasons this tool is a key component of a successful maintenance program.
With an effective CMMS in place, companies experience reduced downtime, shortened times from request to repair, effective parts inventory management and maintenance metrics that enable management to make informed decisions. However, all too often companies find that they are not getting what they need out of a CMMS because of a few common reasons. Here are a few things to consider when choosing a CMMS.
Most companies will need both an enterprise resource planning (ERP) application and a CMMS. Believing that having one software solution instead of two will simplify processes, they frequently choose a CMMS that is also an enterprise resource planning (ERP) system. However, the available combined solutions do not include a best-in-class CMMS. This means that purchasers are getting a watered-down version of a CMMS for the sake of combining it with an ERP.
A best-in-class CMMS will include many features that only a top-tier CMMS can execute well, such as easy-to-use mobile capability. Without mobile capability, maintenance technicians in the field spend extra time retrieving documents or on other non-maintenance tasks, resulting in inefficiencies and lost productivity. Companies who choose a CMMS that is also an ERP without realizing the features they are missing may believe they are making their lives simpler, but really, they are missing out on potential time savings.
Any powerful CMMS will have an integration path to an ERP and be highly configurable. So why not choose best-in-class? Accruent Maintenance Connection is an easy to use, best-in-class CMMS with powerful mobile capabilities that can be easily integrated with any ERP.
Some CMMS projects fail because the purchaser either did not anticipate or underestimated the challenge of setting up their system for success. A proper implementation is critical to getting your new CMMS up and running so it can facilitate the maintenance services you need.
Once a CMMS is properly set up, it can be extremely easy to use, but configuration requires professional expertise. One common mistake is leaving too many data entry fields enabled. With so many fields to fill out, users can get overwhelmed or make frequent errors. This leads to data entry errors that reverberate throughout your maintenance program, resulting in incorrect reporting and hampering management’s ability to make effective decisions.
A well-versed professional services team will be aware of this common mistake and will know to pare down the data fields initially exposed, setting you up for only your key use cases and tailoring your CMMS for the maintenance technicians in a particular field. Other data fields can be added later, after headway is made in user adoption.
The level of professional services you need varies based on your existing systems and use cases. Regardless of your needs, implementation can be a simple, inexpensive process — or it can be long, costly and painful for management. Having the implementation performed by a software vendor’s professional services team or by a trained and authorized third-party partner can ensure this process runs as smoothly and as quickly as possible, getting you to cost savings as quickly as possible.
Accruent offers codeless configuration for much of our reporting with Maintenance Connection. Where some vendors can take 9-12 months to get their software up and running, a full implementation of Maintenance Connection takes only weeks to months.
Learn how integration can happen at many different levels in our on-demand webinar, "CMMS Integration to Maximize Business Value".
A critical predictor of how successful a CMMS will be is how easy it is to use. This greatly affects user adoption and is key to ensuring you receive the return on investment you anticipate. Ask yourself: Is the software intuitive? Does it make my employees’ jobs easier, faster and better? Is the solution responsive to their day-to-day needs, or is it adding to their workload? When considering these important questions, be mindful that the CMMS you choose should consider each of your user’s individual needs in order to facilitate user adoption.
If a CMMS requires complex configuration, it can result in an overcomplicated workflow. If this is the case, you are likely to see a lag in user adoption, particularly among less tech-savvy users. When this happens, it is common for many technicians to use the system improperly, or find ways around using it entirely – both of which result in inaccurate data and reporting.
Maintenance Connection is known for being easy to use and fostering quick user adoption. Choosing a CMMS that is easy to learn and that your employees enjoy using will help you get to the benefits you expect more quickly, ultimately increasing your return on investment through more accurate data.
Another common pitfall is that companies often inaccurately estimate how much they will save with a new CMMS.
One way that savings can be overestimated involves your CMMS configuration and installation process. This step often becomes more expensive and takes longer than initially anticipated. When this happens, companies may not only pay more in professional services than they budgeted for, but must also wait longer to see the benefits of the software, sometimes missing out on months of cost savings, resulting in a real impact on the bottom line.
How much can you save with Maintenance Connection? Visit our Cost Savings Calculator and select your industry to see what this solution can do for your company.
Additionally, companies often do not get the accurate data and easy-to-digest reports that they need to spot cost savings and reach their manufacturing maintenance goals.
Does your CMMS show you the data you need to find cost overages? Do you have a clear visualization into your processes such as scheduling, work orders and inventory? A CMMS should be configured so that reporting is accurate and easy to use.
Figure 1. Common Manufacturing Maintenance Goals
Maintenance Connection’s flexible reporting allows you to define metrics, KPIs and reports that are unique to the different sites and levels within your organization. In addition to including over 150 pre-set canned reports, Maintenance Connection’s SMART Reports feature makes executing batch edits or status updates simple.
There are multitude of reasons that companies do not get the desired results out of their CMMS, many of which can be anticipated or avoided altogether. By making sure you select a best-in-class CMMS, execute a successful implementation, ensure that your software is easy to use and understand how to correctly estimate costs, you will be on your way to making sure both your maintenance team and bottom line see the full benefits of your CMMS.
Accruent’s Maintenance Connection is a purpose-built, simple and straightforward CMMS. Our professional services team can make sure your CMMs is easy to use, is configured quickly and your employees are trained so that you can get to the true cost savings you are promised.
Find out how SSAB improved user adoption and managed a successful CMMS implementation. Still not convinced? Read about Alaska Airlines, L'Oreal, The New York Times or the City of Orlando, Florida. Are you ready to see your name among these internationally recognized titans? Schedule a demo today!
Plan your investment with our CMMS pricing guide and ROI calculator.
Integrating your CMMS and ERP systems can improve communication, maximize insight and facilitate effective data management. Read on for details.
A multi-site, multi-device CMMS can help your company grow and scale with ease. Learn about other key benefits here.
For many organizations, a cloud-based CMMS is the right tool to help them scale, connect mission-critical systems, and optimize operations. Learn how!
Subscribe to stay up to date with our latest news, resources and best practices