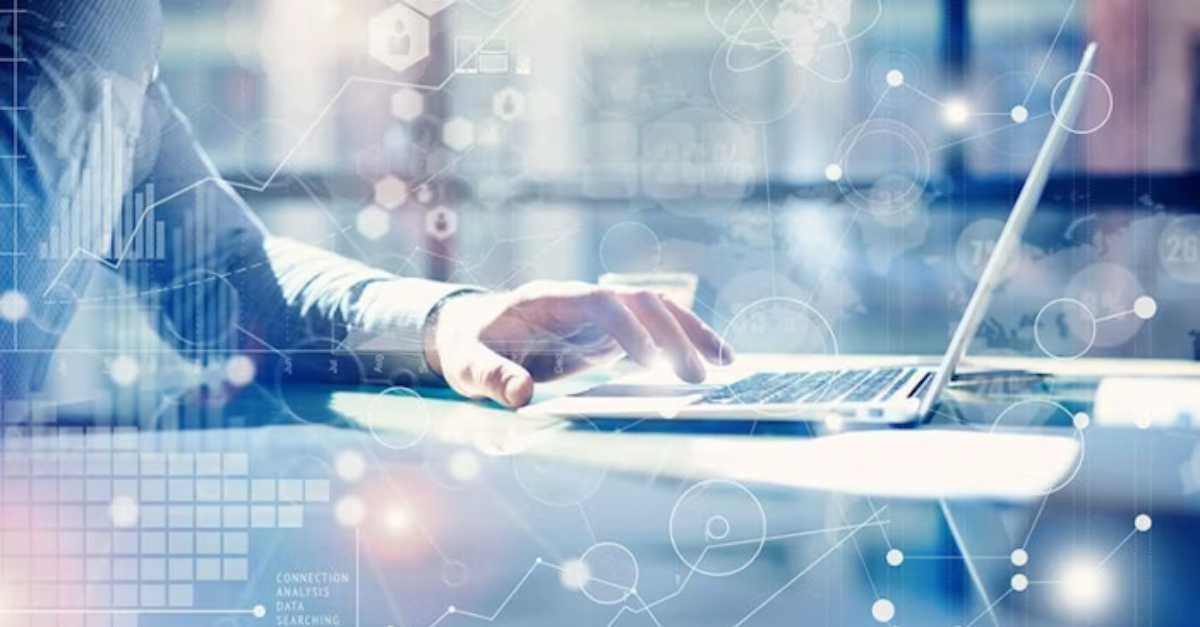
Best Practices for Implementing an IoT Remote Monitoring Solution for Facilities Management
Little inefficiencies in facility management can add up to big consequences like high downtime and poor customer service. IoT remote monitoring can ...
Solutions
Workplace Management Solutions
Real Estate Management Solutions
Maintenance Management Solutions
Energy Management Solutions
Engineering Document Management Solutions
Asset Management Solutions
Automate campus scheduling for classes, meetings, and exams with our EMS software.
Plan and manage conferences effortlessly with EMS software to impress guests and streamline operations.
Boost workplace flexibility and maximize space use with seamless desk and room booking.
Organize workplace or campus events smoothly, creating memorable experiences.
Optimize workspace, manage allocations efficiently, and reduce costs with our space management solutions.
Deliver projects on time and within budget by improving communication, collaboration, and efficiency with our software.
Streamline lease accounting for ASC 842, IFRS, and GASB compliance.
Manage leases efficiently by tracking key dates, analyzing costs, and ensuring compliance.
Centralize data and analytics for better insights, faster negotiations, and revenue growth.
Centralize facility and asset maintenance, automate work orders, and ensure compliance with our CMMS software.
Extend asset life, reduce downtime, and prevent costly repairs with data-driven monitoring.
Prevent equipment failures and extend asset life by detecting and addressing issues early.
Make sustainable, cost-efficient energy decisions by monitoring and optimizing power consumption.
Remotely monitor and control equipment with real-time data to predict issues, boost efficiency, and reduce downtime.
Easily share and collaborate on documents, creating a single source of truth for engineers and contractors.
Manage and analyze assets across their lifecycle to schedule maintenance, reduce downtime, and extend lifespan.
Improve visibility, automate work orders, and ensure compliance for efficient facility and asset management.
Resources
Browse our full library of resources all in one place, including webinars, whitepapers, podcast episodes, and more.
Support
Looking for access to technical support, best practices, helpful videos, or training tools? You’ve come to the right place.
About Accruent
Get the latest information on Accruent, our solutions, events, and the company at large.
Do you know how to effectively manage your healthcare facility? Can you reach compliance, cybersecurity, and other facility management goals? HFM can help.
The primary focus of any healthcare facilities management (HFM) department is to ensure an exceptional environment of care along with the safety and security of both patients and staff.
As the COVID-19 pandemic nears its conclusion, and as technology continues to progress, managing healthcare facilities is becoming increasingly important – and increasingly challenging to manage. Whether it's maintaining certification compliance or ensuring cybersecurity, a facilities manager's job is only getting more complex.
Healthcare facilities management is the maintenance and oversight of a healthcare facilities' development, maintenance, security and operations. This includes any building that provides healthcare services, such as clinics, long-term facilities, surgical centers and hospitals, and covers every aspect of facility upkeep.
The facilities management department – often abbreviated as HFM – is responsible for supervising the maintenance, operations and overall security of healthcare facilities. This ranges from overseeing large construction projects and maintaining federal compliance down to everyday cleaning, maintenance and upkeep.
The following are six essential functions and responsibilities of healthcare facilities management:
Day-to-day operations for facilities managers include:
While HFM professionals may not personally handle each of these responsibilities, they typically serve as the day-to-day manager, overseer, and final word for broad decision-making.
Maintaining certification and building compliance is critical to the success of any healthcare organization and is one of the paramount responsibilities of any facilities manager. Facility Managers are required to ensure facilities compliance with laws such as the Americans with Disabilities Act and manage the continual upkeep of certifications and accreditations, like those issued by The Joint Commission.
In line with the mission of any healthcare facility is ensuring a safe and reliable Environment of Care (EoC) for patients. This includes any healthcare site where patients are treated, for both inpatient and outpatient settings. The primary goal of the EoC is to provide a safe and efficient environment for patients and staff members.
HFM teams are tasked with performing routine inspections to identify and address any areas of concern in and around healthcare facilities, such as:
HFM teams frequently work closely with hospital leadership to craft detailed EoC plans and policies that ensure the safety and well-being of patients, visitors and staff.
While facilities management teams may not directly handle or lead construction projects, they are heavily involved throughout the construction process and responsible for ensuring that projects stay on time and budget.
Healthcare facilities professionals are also tasked with managing capital plans for future facility investment and ongoing upkeep of facilities and assets.
Within the healthcare industry at large, security continues to be a high priority. For facilities managers, this can include managing:
As the healthcare industry increases its reliance on technology and moves into the cloud, the need for increased cybersecurity skyrockets. With the Internet of Things (IoT) becoming commonplace within hospitals, facilities management teams are working alongside IT to create cybersecurity plans that will ensure patient care data is protected from hackers who may exploit equipment with older operating software as a pathway into the organization’s networks to steal sensitive patient information and research data, or to disable systems that may compromise the safety of facilities and equipment.
According to Becker’s Hospital Review, these are a significant risk for the industry, with the volume and intensity of cyberattacks on hospitals and health systems having increased during the second half of 2020 and experts believing there are more to come.
In fact, on Nov. 16, 2020, the federal government issued a cybersecurity warning to healthcare providers about "credible, ongoing and persistent" threats.
It is critical that anyone working in healthcare facilities management stay informed and aware of these types of attacks, and work closely with their IT teams to secure and monitor their devices for potentially exploitable flaws.
Hospital maintenance is a complex task for any team, especially if current methods are based on a reactive maintenance policy.
By implementing preventive maintenance programs, HFM team are able to handle routine maintenance before issues occur, reducing the number of requests they receive and extending the life of their assets, ensuring equipment is working at maximum performance. It can also lead to:
Additionally, healthcare organizations have been given authority by the Centers for Medicare & Medicaid Services (CMS) to implement defensible alternative equipment maintenance (AEM) programs, which allows a healthcare facility to adjust its maintenance, inspection and testing frequency for facility and medical equipment from what is recommended by the manufacturer based on a risk-based assessment by qualified personnel. By adopting AEM programs, providers can save significant resources without sacrificing patient safety and care throughout.
Facility maintenance and plant operations play a significant role in patient and provider safety. An exceptional facilities maintenance staff -- one that combines an understanding of patient care and technological solutions -- can help prevent the spread of disease and ensure compliance and security for any hospital.
As many organizations push for a rapid return to “normal,” hospital facility management leaders face a hard reality that they may never be a return to the old normal. For many hospitals, the path to an informed, modern facilities management team is becoming more complicated. From shrinking margins to an aging workforce, hospitals increasingly face issues that at best threaten their overall functionality and efficiency, and at worst, threaten patient care.
Healthcare systems are employing a variety of strategies to combat shrinking margins and rising costs. Many hospitals have reduced costs and efficiencies at the margins of their organizations. Still, long-term sustainability may require a fundamental digital transformation of how services are organized and delivered.
A modern healthcare and hospital facility management solution can help.
Healthcare facility management continues to be a cornerstone for providing the best patient care possible. Whether it’s by maintaining day-to-day operations or leading cybersecurity initiates, healthcare facilities managers can help move healthcare organizations into the future.
Discover the latest trends and best practices in healthcare technology. Download our white paper.
Little inefficiencies in facility management can add up to big consequences like high downtime and poor customer service. IoT remote monitoring can ...
Learn why implementing healthcare technologies brings along critical risk factors — and how facility managers and IT staff can better mitigate those ...
Accruent was recently established as a Market Leader in FeaturedCustomer’s Fall 2021 Facilities Management Software Customer Success Report. This ...
Subscribe to stay up to date with our latest news, resources and best practices