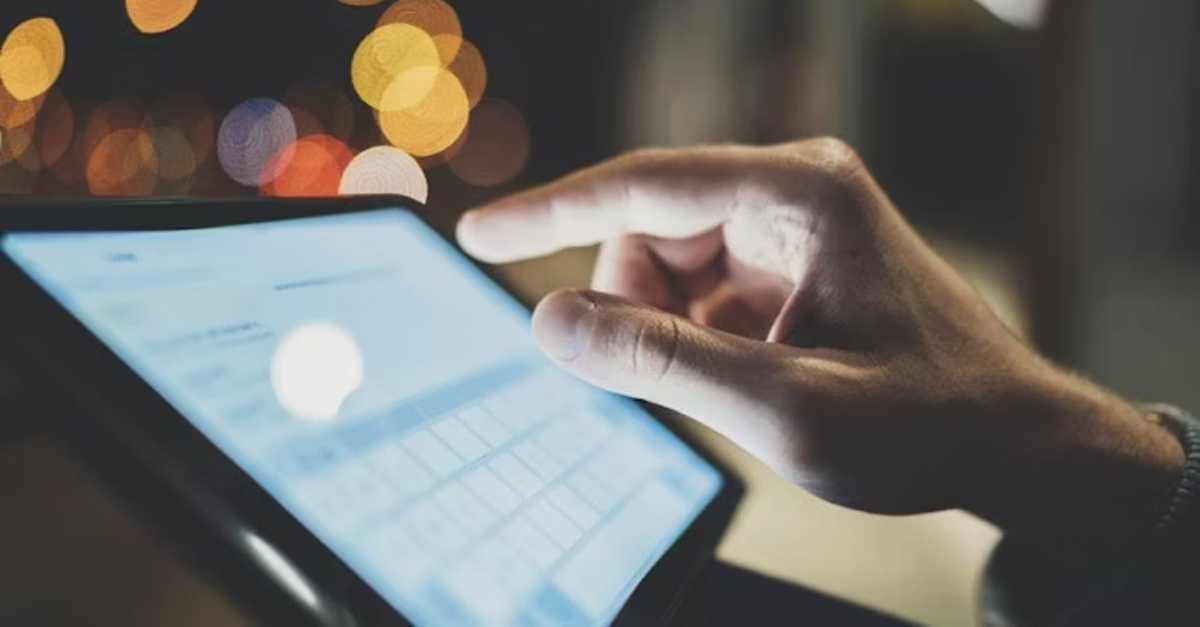
Improve Efficiency with Mobile Access to Your Engineering Document Management System
With more workers relying on their mobile devices to complete their jobs, you need to better support them with easy mobile access to your EDMS.
Solutions
Workplace Management Solutions
Real Estate Management Solutions
Maintenance Management Solutions
Energy Management Solutions
Engineering Document Management Solutions
Asset Management Solutions
Automate campus scheduling for classes, meetings, and exams with our EMS software.
Plan and manage conferences effortlessly with EMS software to impress guests and streamline operations.
Boost workplace flexibility and maximize space use with seamless desk and room booking.
Organize workplace or campus events smoothly, creating memorable experiences.
Optimize workspace, manage allocations efficiently, and reduce costs with our space management solutions.
Deliver projects on time and within budget by improving communication, collaboration, and efficiency with our software.
Streamline lease accounting for ASC 842, IFRS, and GASB compliance.
Manage leases efficiently by tracking key dates, analyzing costs, and ensuring compliance.
Centralize data and analytics for better insights, faster negotiations, and revenue growth.
Centralize facility and asset maintenance, automate work orders, and ensure compliance with our CMMS software.
Extend asset life, reduce downtime, and prevent costly repairs with data-driven monitoring.
Prevent equipment failures and extend asset life by detecting and addressing issues early.
Make sustainable, cost-efficient energy decisions by monitoring and optimizing power consumption.
Remotely monitor and control equipment with real-time data to predict issues, boost efficiency, and reduce downtime.
Easily share and collaborate on documents, creating a single source of truth for engineers and contractors.
Manage and analyze assets across their lifecycle to schedule maintenance, reduce downtime, and extend lifespan.
Improve visibility, automate work orders, and ensure compliance for efficient facility and asset management.
Resources
Browse our full library of resources all in one place, including webinars, whitepapers, podcast episodes, and more.
Support
Looking for access to technical support, best practices, helpful videos, or training tools? You’ve come to the right place.
About Accruent
Get the latest information on Accruent, our solutions, events, and the company at large.
Mobile CMMS functionality is crucial for remote, multi-site and digitally transformed operations. If you're not mobile, here's why you're missing out.
Over the past several months, remote capabilities have gone from a “nice-to-have" digital transformation feature to a foundational part of effective asset and facilities management. Modern manufacturing organizations have a lot to juggle as they move forward into the “new normal”: their technological infrastructure, the physical safety of their employees, cybersecurity and the day-to-day asset management tasks that will lead to more predictive operations, higher revenue and maximized ROI.
It’s a lot to master – and it’ll be impossible without mobile and remote tools. That’s why it’s essential that your business-critical technologies, including your computerized maintenance management system (CMMS), have robust mobile capabilities.
Here’s everything you need to know about the present and future of remote operations in the manufacturing space, as well as what features to look for in your mobile CMMS tool.
The world of asset management has changed dramatically over the last decade, with the Fourth Industrial Revolution (4IR) and emerging trends like artificial intelligence (AI), the Industrial Internet of Things (IIoT), advanced robotics and automations widening the possibilities – and increasing expectations – for companies in asset-heavy industries.
For years, though, deployments of these new technologies have been inconsistent and varied, with many organizations preferring their “tried-and-true” legacy systems and finding their decision-makers unwilling to invest in expensive new tech that may not yield a strong return on investment (ROI).
That all changed with COVID-19. Organizations suddenly had to maintain operations in a largely (if not completely) remote environment: their technicians couldn’t be on the floor, they had to implement social distancing, they needed full transparency into their data and operations from multiple locations – and they had to move to the cloud and integrate their technologies for all this to work (bad news for all the businesses relying on standalone legacy or on-premise systems).
That said, though this change certainly fast-forwarded digital transformation for those dragging their feet, the truth is that it was a long time coming. COVID-19 simply forced a coming-to-terms with changes in tools, strategy and processes that needed to happen to achieve the transparency, ease-of-use and data-driven insight necessary to optimize operations, cut costs, reduce inefficiencies and move ever-closer toward a more reliable and predictable maintenance environment.
Now, the initial shock of COVID – and the ensuing rush to implement anything to survive – has subsided, and companies are now looking toward future-proofing their operations and their technological ecosystem. Here, two questions remain: what will asset management operations look like in the future, and does your business have the right tools and strategies in place to thrive in the “new normal”?
In short, now what?
Now that the world has largely settled into the post-coronavirus “new normal,” there are a few asset management trends that are here to stay (and you can read about more of them in greater detail here).
One of them? Remote work and the implementation of a robust remote tool like a mobile CMMS.
Remote work is here to stay, even after the pandemic is over. Statistics show that:
So, although many have returned to the office in some capacity (and others will continue to trickle in), the professional landscape will look different moving forward. For most organizations, it’ll be a hybrid workspace, and there will be necessary shifts in company culture, engagement, the way work gets done and how physical spaces are utilized.
For asset management professionals, in particular, a few concerns will remain top of mind moving into this hybrid environment:
A mobile-friendly, device-agnostic CMMS system will help asset management organizations address all these concerns – which is why it’ll be a have-to-have looking forward.
Even before COVID-19, mobile CMMS systems were becoming key solutions for companies looking to improve their efficiency, productivity and ROI. The right mobile CMMS solution can, among other things, offer:
All of this will help organizations maximize their technological infrastructure, enhance their cybersecurity, improve physical safety of employees and streamline their asset and facility maintenance tasks. That said, there are key features and functionalities of a mobile CMMS to keep top of mind.
Single sign-on (SSO) is an authentication feature that simplifies the login process, allowing employees to access various business-critical tools using one login and password. Investing in a mobile CMMS with SSO capabilities can have many benefits, helping to:
One of the biggest benefits of a responsive mobile tool is the ability to improve transparency, consistency and communication across sites or between employees and departments. A device-agnostic mobile app can help your team sidestep these concerns, accessing the functionality and the data they need on any smartphone, tablet or desktop.
If your mobile CMMS allows you to generate QR codes or barcode-enabled tracking, it can make it easier for your team members to:
These capabilities, in turn, can improve labor efficiency, increase employee satisfaction and reduce wrench time and labor-related costs.
Of course, it’s all ultimately about the CMMS system behind the mobile app. A robust CMMS will provide comprehensive functionalities like complete work order management, inventory management, labor scheduling and project-based work order management capabilities. It will also provide mission-critical, real-time insight, along with service history tracking and robust reporting and analytics.
You can learn more about how to select the right CMMS for your business’ needs here.
AI, analytics, automation – all these tools will need to be deployed effectively and strategically over the next few years if they are to increase flexibility, decrease costs, maximize transparency and support strategic growth.
This will require adoption of business-wide solutions rather than stand-alone software. This tech must be well-integrated with your broader technological ecosystem, agile and focused on personalizing the customer experience.
It will also require that many asset-focused businesses upgrade their infrastructure controls to enable digital management.
For any of this to work, though, the tools must be widely adopted and informed by strong strategies. This may require that organizations rethink their facility management playbook to include remote, data-first operations. In any case, it’s important to consider your broader technological infrastructure and to choose mobile tools that will integrate well.
If there’s one capability that COVID-19 shone a bright light on, it’s remote monitoring via sensor technology. HVAC systems, asset tagging, inventory management, equipment monitoring – it can all be done remotely using sensor technology, and more companies than ever are deploying IoT to remain operational in the face of the pandemic.
Even better? This remote monitoring technology has a wide range of applications: it can not only help with asset management, but also improve things like sanitation, health and safety.
Once again, though, effective use of these tools will depend on interoperability, integrations and effective implementation.
Remote and mobile CMMS tools with be critical moving forward into the “new normal.” The key is to get it right and find the most effective tool – with the right functionalities – for your organization and your technological infrastructure.
Plan your investment with our CMMS pricing guide and ROI calculator.
With more workers relying on their mobile devices to complete their jobs, you need to better support them with easy mobile access to your EDMS.
Remote, multi-device tools – like an offline, native mobile CMMS – are crucial in today’s connected workplace. Here’s why.
Do you know your most expensive retail work orders — and how to curb those costs? Here are our top tricks and best practices.
Subscribe to stay up to date with our latest news, resources and best practices